- 35 million dowel pins produced each year
- Co-designers of custom fasteners for 100 years and manufacturer of standard products
- From M2.5 to M20 and from 6 mm to 22 mm
- Steel, stainless steel, brass, etc. (Other materials available on request).
Internally and externally threaded dowel inserts are fasteners with an internal tap and external thread. They enable assembly and fastening of plastic parts with high pull-out resistance. Moreover, they can be screwed and unscrewed at will. They can also be overmoulded.
Manufacturer of dowel pins with internal and external thread
Manufacturer of dowel pins with internal and external thread
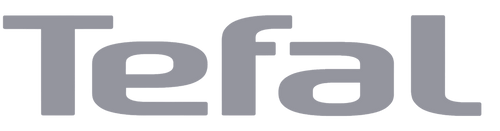
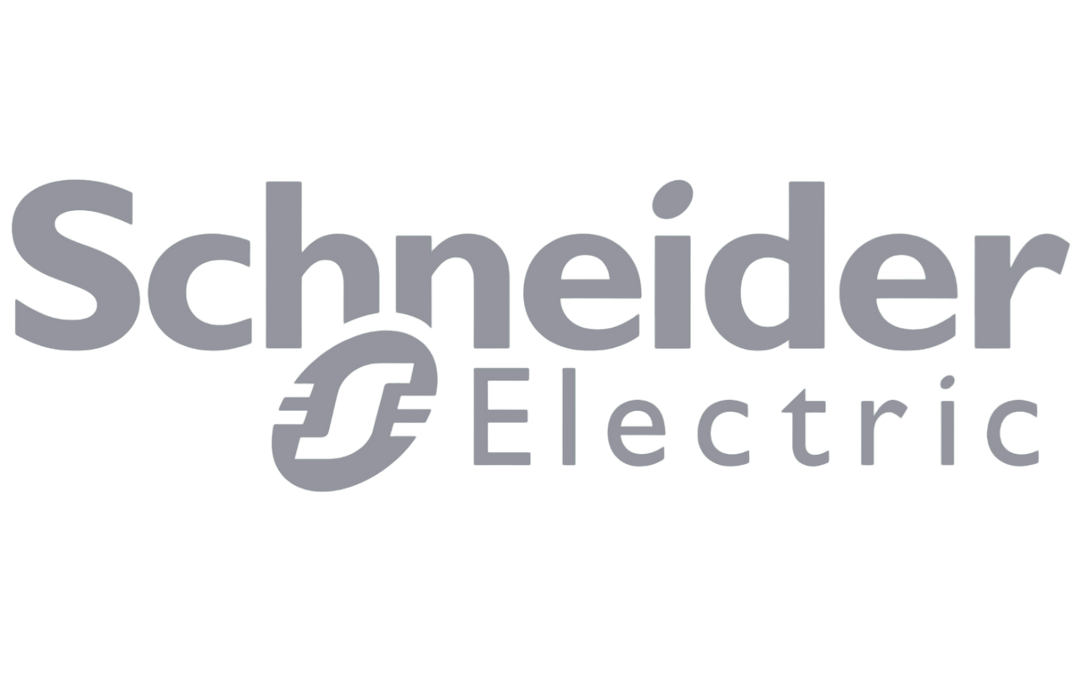
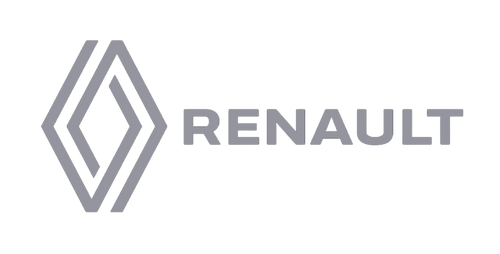
Advantages of manufacturing with LGC Industries
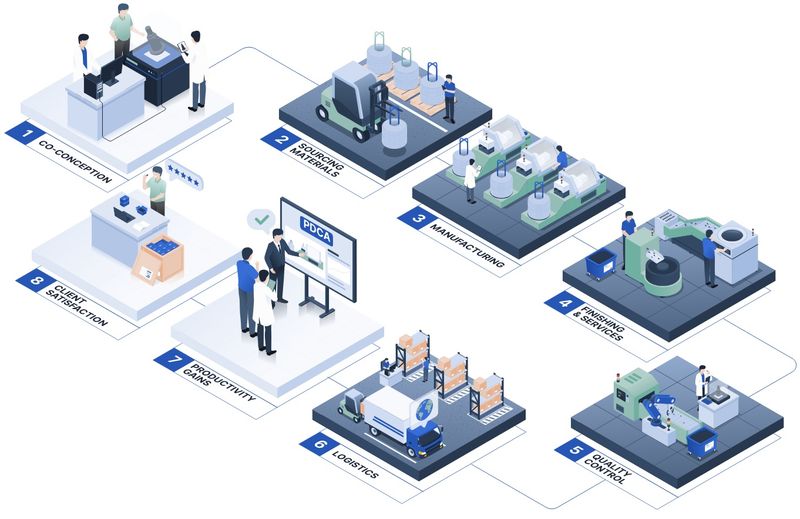
- 45 Escomatic machines
- 42 grooving machines
- 8 plunge & through-feed grinding machines






Find out more about our products' technical features
Discover other products
Dowel pins with internal and external thread: assembly and fastening all in one part
Threaded dowel pins are essential components should you wish to offer solid and long-lasting fastening to your parts. Thanks to their cylindrical design with an internal tap and external thread, they provide excellent pull-out resistance.
You can screw and unscrew them at will, which makes it much easier to put together and dismantle your assemblies.
Here at LGC, we understand the importance of designing tailor-made solutions to your specific requirements. This is why we support and advise you throughout the process, offering prototyping, measurement and pull-out resistance test services.
Our expertise means we can help you industrialise your project by offering you effective installation and assembly solutions.
How are LGC's threaded dowel pins made?
From material to internally and externally threaded dowel
The beginning of the manufacturing process for threaded dowel pins is similar to that of threaded inserts and self-tapping dowel pins.
The first step is to thread the raw material coil on the outside.
This stage is called rolling because the dowel is put between three roller dies, with the rolling system cold working the part by compression in order to create the thread.
Cold deformation increases the material's elastic strength.
This means that a rolled dowel pin / spacer will have better pull-out resistance than a laminated material.
The second step involves cutting the raw material tube in a suitable machine. The tube is then cut to the desired length.
Chamfers or surface finishing operations can be carried out on the material at this point.
It then goes through a grinding stage. A die presses the parts against a grinding wheel rotating at high speed. Thanks to abrasion from the grinding wheel, the diameter of the part is modified to reach tolerances of just a few microns (~5-6 μm).
Then it's time for tapping - a rotating tap will pass through the inside of the part to give it the desired internal thread.
What are the advantages of a dowel pin with both an internal and external thread?
- Reinforcement when used in soft materials: Internally and externally threaded dowel pins reinforce fastening elements in soft materials, giving increased strength to fasteners with screws and bolts. This is particularly useful in assemblies that are under significant loads.
- Increased lifespan: Thanks to their ability to provide a stronger thread, our internally and externally threaded dowel pins extend the lifespan of your assemblies by minimising wear and tear of the thread over time.
- Reduced risk of tearing: These dowel pins reduce the risk of taps being ripped out, ensuring stable fastening even under conditions with variable loads.
- Ease of repair: In the event of damaged tapping, a dowel pin with internal and external threads is an efficient repair option, eliminating the need to replace expensive components.
- Application in demanding environments: Internally and externally threaded dowels are well able to withstand highly demanding environments, and are a dependable solution even in conditions where other types of fasteners are not.