Improving assembly of hospital beds
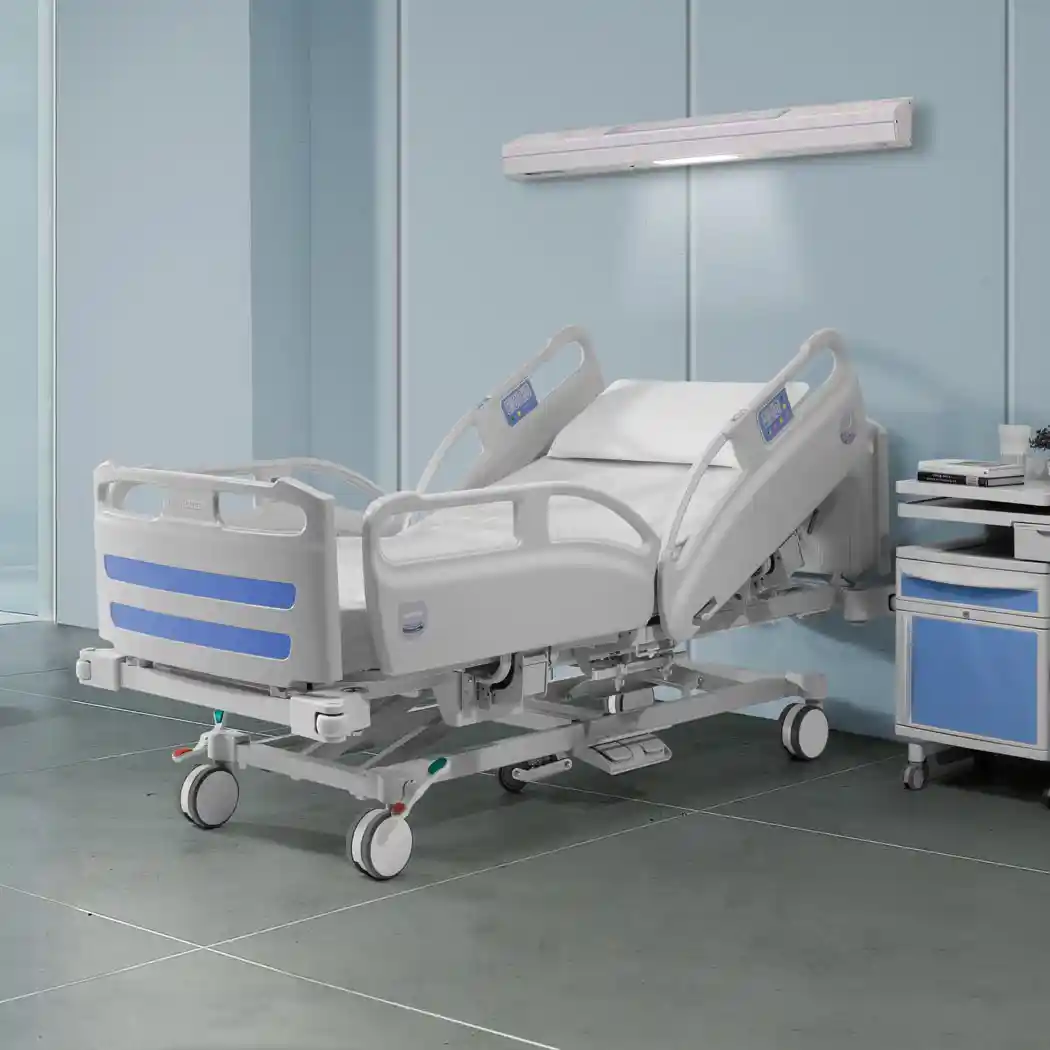
What was the context and the customer's desired application?
The customer is a manufacturer of medical equipment, producing hospital beds with adjustable mechanisms such as metal shafts with machined indents, in which two circlips are inserted to hold the parts in place. This system was used for the joints that allow the adjustment of the height, the inclination or the supports of these beds.
Although functional, this system had several limitations:
- Assembly complexity: Fitting circlips requires specific tools and prolongs assembly time.
- High cost: Each machined, indented metal shaft, combined with the circlips, constitutes an expensive solution in terms of materials and machining.
- Reliability issues: If repeatedly handled or put under heavy loads, the circlips may come loose, which can compromise stability and safety.
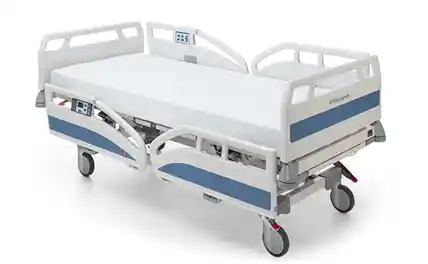
What fasteners was the customer using before contacting us?
The customer was previously using a standard metal shaft with two machined indents, in which two circlips were inserted to hold the components in place. However, this proved to be an expensive and impractical set-up, especially due to assembly defects and the possibility of a mechanical failure.
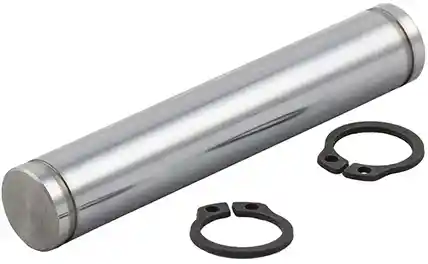
What studies did we conduct?
Analysing the issue
We worked closely with the client to understand their needs and the technical constraints of medical beds. The main topics of discussion were:
- Cost optimisation: Reducing production and assembly costs.
- Improving safety: Elimination of risks when detaching the circlips.
- Simpler assembly process: Decreasing the steps and tools necessary for assembly.
Lab testing and validation
We carried out several comparative tests between the client's existing system (axis + rings) and our solution. These tests included:
- Pull-out resistance.
- Staying position under dynamic loads.
- Durability after several cycles of use.
What was our advice to the client?
We proposed a fluted pin as a replacement for all three parts (pin + 2 circlips). This fastener offers numerous advantages:
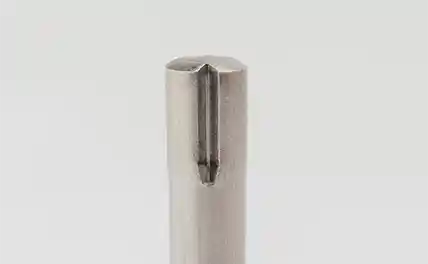
- No more circlips: The fluted pin guarantees flawless support without the need for additional elements.
- Reduced costs: Fewer parts, no indent machining, and a simpler production process.
- Quick and intuitive assembly: The pin can be installed by simply inserting it, no need for any specific tools.
- Increased reliability: The grooves prevent any unwanted rotational or translational movement.
What were the quantifiable benefits for our client?
Thanks to this solution, the client observed:
- A 27% reduction in production costs per mechanism.
- A 76% reduction in assembly time, thereby increasing the production rate.
- A significant improvement in the safety and reliability of medical beds, reducing the returns associated with this particular adjustment mechanism by 86%.
Our solution allowed the client to remain competitive in a demanding market all while strengthening their products' quality.
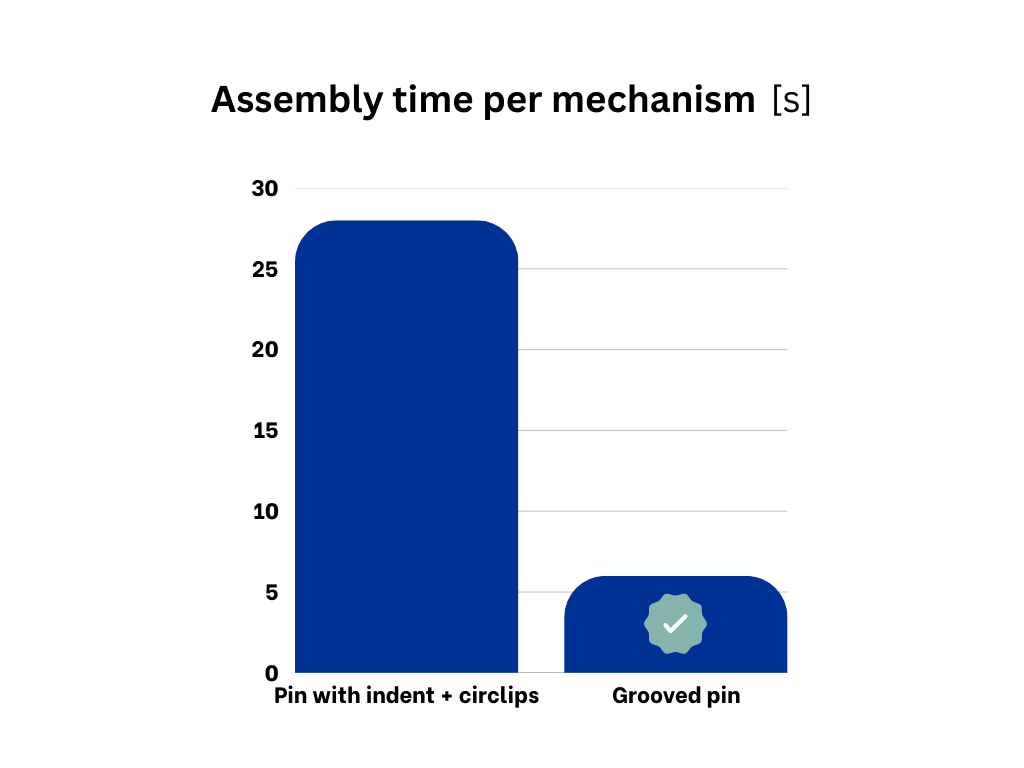
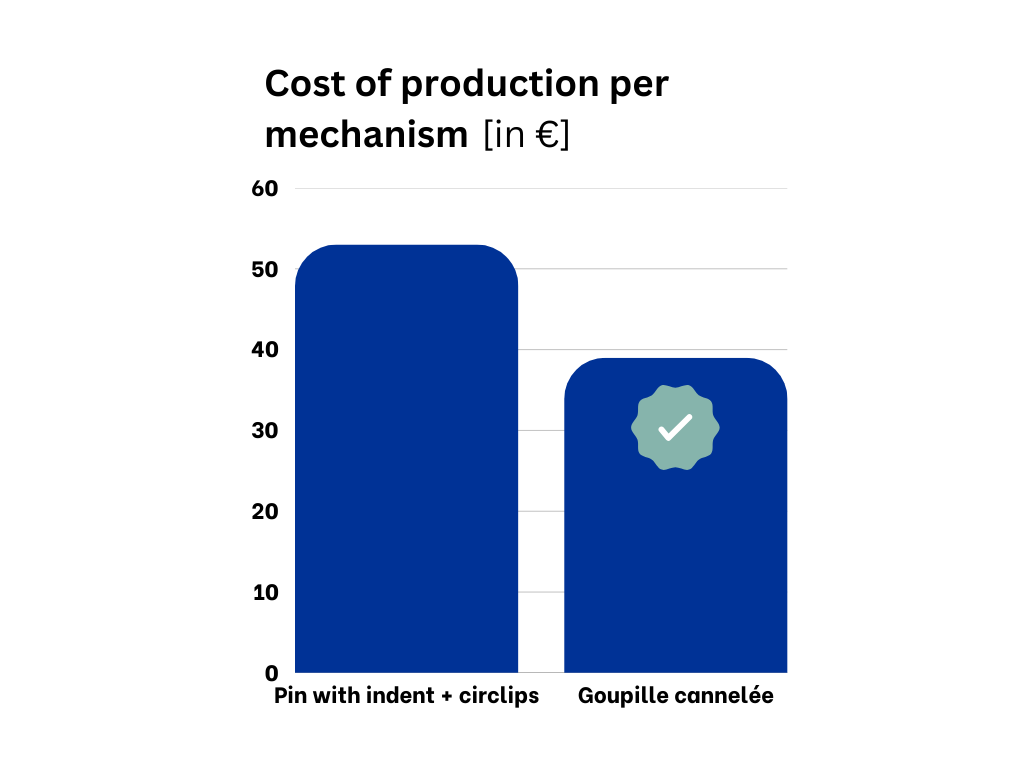
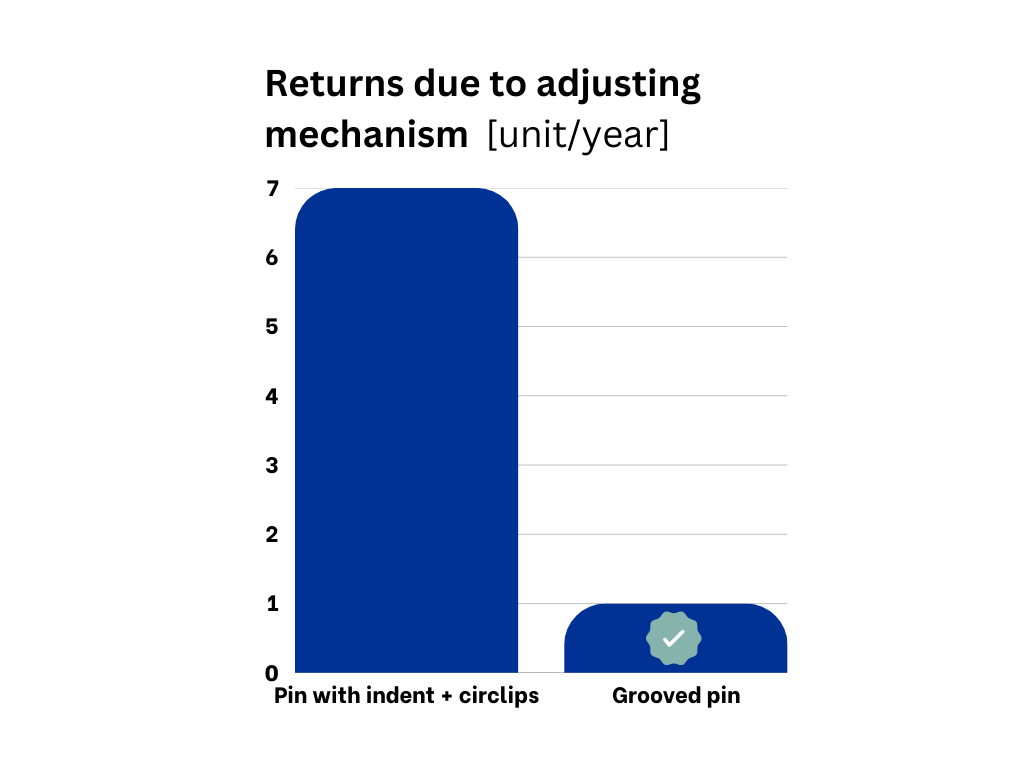