- 150 million grooved pins produced each year
- Co-designers of custom fasteners for 100 years and manufacturer of standard products
- From Ø1.5 to Ø25 and from 8 mm to 100 mm
- Steel (free cutting, heat-treatable, carbon, alloys...), stainless steel (303, 316, 420, ...) aluminium, brass, etc.
Grooved pin iso 8744 - din 1471 - Cylindrical pin
Grooved pin iso 8744 - din 1471 - Cylindrical pin
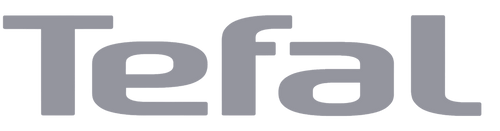
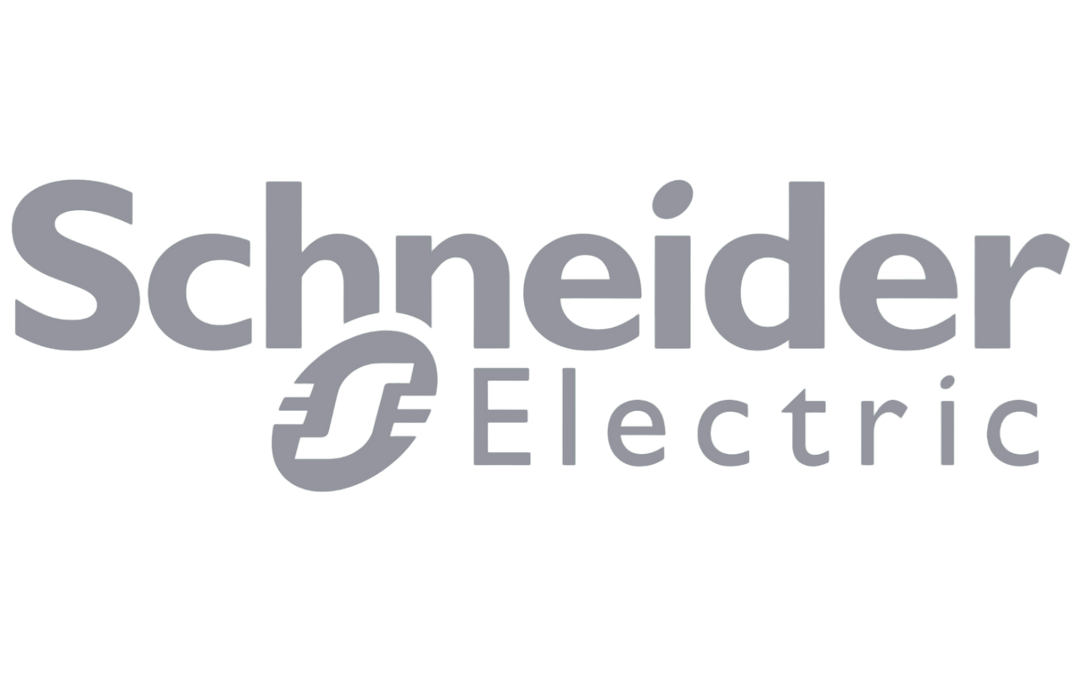
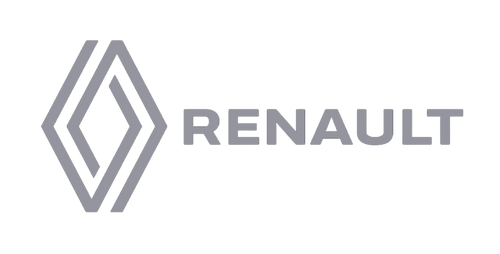
Advantages of manufacturing with LGC Industries
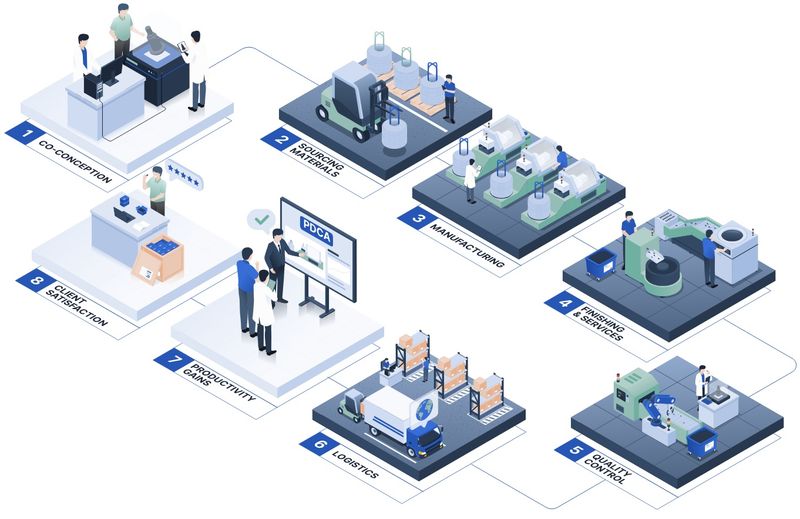
- 45 Escomatic machines
- 42 grooving machines
- 8 plunge & through-feed grinding machines






Find out more about our products' technical features
Discover other products
Using grooved pins - ISO 8744 / DIN 1471
The type of grooved pin you need depends on what specific purpose it will serve.
Grooved pins can have various uses in an assembly:
- Solidity: Holding two parts together thanks to their machined grooves and the pressure they exert on the hole in which they are inserted.
- Connection & rotation: Grooved pins allow for pivot movement between two elements, like in door hinges.
- Positioning: Grooved pins enable two parts to be positioned relative to each other, in order to then add another fastener, e.g. a screw.
Based on these three functions, we can recommend the type of pin best suited to your needs.
In most cases, we would recommend using ISO 8744 / DIN 1471-standard pins to meet connection needs in assemblies where one part must be able to rotate relative to another.
To ensure both parts are solidly fastened, blocking any and all degree degrees of freedom, pins with grooves along their entire length are to be used. The grooves allow the pin to fit tightly into the two parts.
Three types of pins can be used in this case:
- ISO 8739 / DIN 1470
- ISO 8740 / DIN 1473
- ISO 8744 / DIN 1471
Constant grooves, like on these ISO 8744 / DIN 1471 standard pins, allow the pin to be pre-positioned thanks to a slight bulge (a few millimetres) in its diameter. This keeps the pin in place before it is totally pressed inside.
ISO 8744 or DIN 1471-standard pins have grooves all along their length, allowing for the part to be pre-positioned in the assembly on the side where bulge diameter is smallest.
Once in place, a press is used to ensure the pin is installed snugly with the help of its grooves.
This is what makes this grooved pin different from the other two, which have constant grooves all along their length.