- 20 million inserts produced each year
- Co-designers of custom fasteners for 100 years and owners of the Intervis® brand
- From M2.5 to M16 and from 6 mm to 22 mm
- Steel (raw, case-hardened, zinc-plated), stainless steel, brass, etc.
The Intervis® self-tapping threaded insert can be screwed directly into a smooth hole drilled beforehand. The Intervis® itself carves a thread into the part. It is ideal for installation in medium-hard materials such as light alloys, compressed wood or plastic materials.
Slotted threaded insert - Self-tapping insert - Standard intervis
Slotted threaded insert - Self-tapping insert - Standard intervis
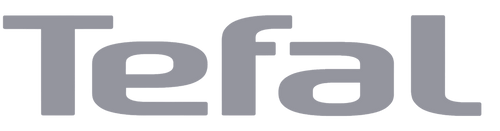
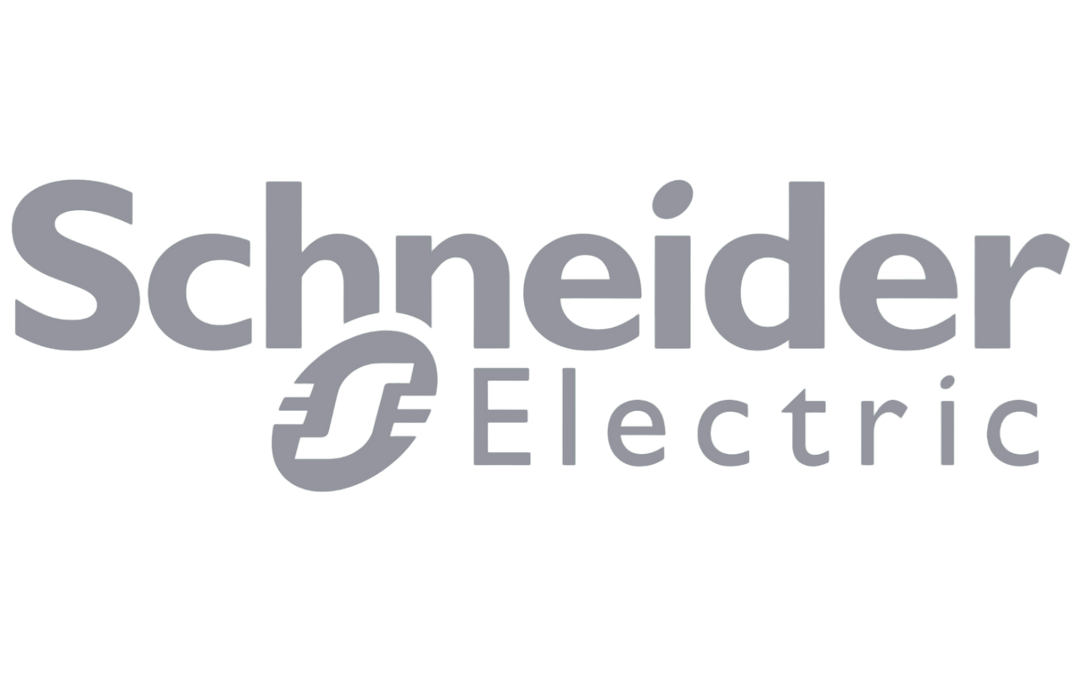
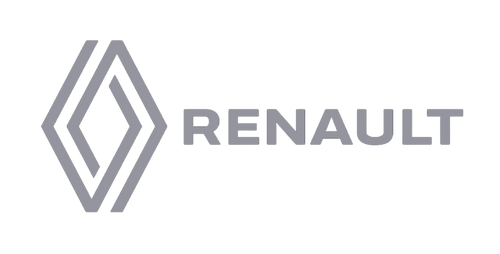
Advantages of manufacturing with LGC Industries
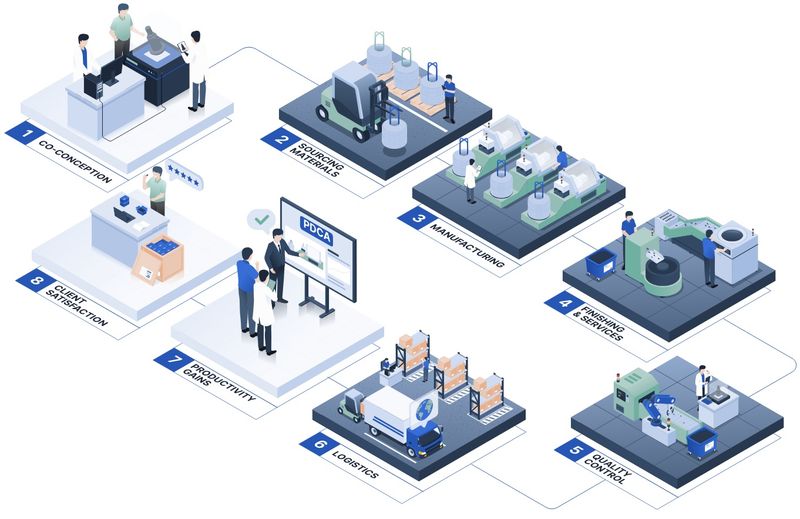
- 45 Escomatic machines
- 42 grooving machines
- 8 plunge & through-feed grinding machines






Find out more about our products' technical features
Discover other products
What is a self-tapping insert?
The self-tapping insert from Intervis® is a cylindrical fastener used to create strong and durable threads in a wide variety of materials such as plastics, composites, and soft and medium-hard metals.
Thanks to its intelligent design, this threaded and slotted self-tapping insert is a reliable and effective solution for strengthening fasteners in industrial applications that require high assembly strength.
A self-tapping insert can be used as an original fastener or to repair a broken thread.
In certain materials such as light alloys, plastic or compressed wood, classic tapping can quickly become worn out, especially when put under repeated strain. Tightening too frequently or too hard can rip out the threads, making the part unusable. This is where threaded inserts come in - they help to strengthen the threads.
Whether assembling plastic parts in the automotive industry or fastening components in composite airplanes, the self-tapping insert guarantees optimal pull-out resistance and excellent mechanical properties in even the most demanding environments.
What's different about LGC's self-tapping insert?
The LGC self-tapping insert belongs to the family of threaded inserts. What makes it different from other threaded fasteners is its extra slot: this allows for self-tapping and thus simplified installation of your insert.
Generally, the self-tapping insert is used to fasten elements into pliable materials such as:
- Wood
- Plastic
- Composites
Self-tapping inserts are used for a variety of rigorous standardised industrial applications, such as:
- Cars
- Fastening electronic cards.
- Fastening components in bikes, skis and snowboards.
- Plastics processing, e.g. overmolded elements.
What are the disadvantages of helicoils?
Although they are used in various applications to strengthen threads, helicoils also have their limitations, making them a less efficient solution than self-tapping inserts in some situations.
More complex to install
Unlike self-tapping inserts, helicoils must be installed in stages as follows:
- Pre-drilling of the materials
- Specific threading with a dedicated tap
- Implantation via a specialised tool
These extra steps increase install time, equipment costs and the likelihood of making mistakes.
On the other hand, a self-tapping insert can be installed directly into a smooth hole drilled beforehand, eliminating the need for threading and specialised tools.
Less tight fastening
Helicoils simply root themselves into an existing thread, which can result in weakened mechanical resistance, especially in the event of high tensile stress or frequent untightening.
In contrast, self-tapping inserts, with their sharp-edged slots and external threading, can be fitted straight into the material without any extra steps.
Limited materials for application
Helicoils are less suited to soft or medium-hard materials, such as wood or compressed wood, as they require solid threading in order to stay in place. Self-tapping inserts can be put directly into such materials, allowing for robust solutions even when placed on low-density surfaces.
Although helicoils may be a viable option in some cases, they remain a less practical solution than self-tapping inserts due to their fitting, resistance to soft materials and adaptability issues.
How is a self-tapping insert made?
The beginning of the manufacturing process for Intervis® self-tapping inserts is similar to that of conventional inserts.
Step 1: external threading of the raw material coil
This stage is called rolling because the tube goes between 3 rollers and the rolling system, which cold works the part by compressing it, in order to create the external threading of the self-tapping insert.
Step 2: parting the raw material tube
The tube is cut to the desired length.
It is possible to add chamfers or finishes to the material, as is the case for the self-tapping insert for wood, the self-tapping insert for plastic or the BFUP self-tapping insert for concrete.
Step 3: milling
A milling cutter cuts the part and creates our Intervis® threaded insert's characteristic slot.
Final Step: tapping
This is the internal threading of the Intervis® slotted threaded insert.
To do this, a rotating tap passes inside the insert to give it its thread. The insert then becomes a threaded insert and, therefore, a self-tapping threaded insert.
Would you like to learn more about our self-tapping inserts and how they are made?
See our technical guide on Intervis® threaded inserts
What are the advantages of self-tapping inserts?
Each type of threaded insert has distinct features, each with its own advantages both in terms of use and in their respective technical specifications.
The Intervis® self-tapping insert stands out due to several notable advantages compared to other types of self-tapping threaded inserts. The Intervis self-tapping insert guarantees:
- Increased strength: The innovative design of the threaded insert with its three slots gives it exceptional strength against tensile and shear forces. This reinforced resistance ensures robust and durable fastening, perfectly suited to applications that require maximum safety.
- Durability over time: The threaded insert's slots allow it to last longer in pliable materials, with the slots allowing the insert to be inserted easily into the material - this reduces constraints as well as the risk of breakage.
- Quick to install: As there is no need to create a tap for the receiving hole, there is one less step in the fitting process, meaning that precious time is saved by using the Intervis threaded insert.