This process enables the creation of high-precision parts from metal bars, gradually removing material with the help of a sharp tool. It is mainly done on a cam-driven lathe (Escomatic lathe), where cams are used to cut the bars.
The bar turning experts - CNC machining
The bar turning experts - CNC machining
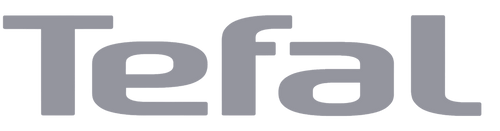
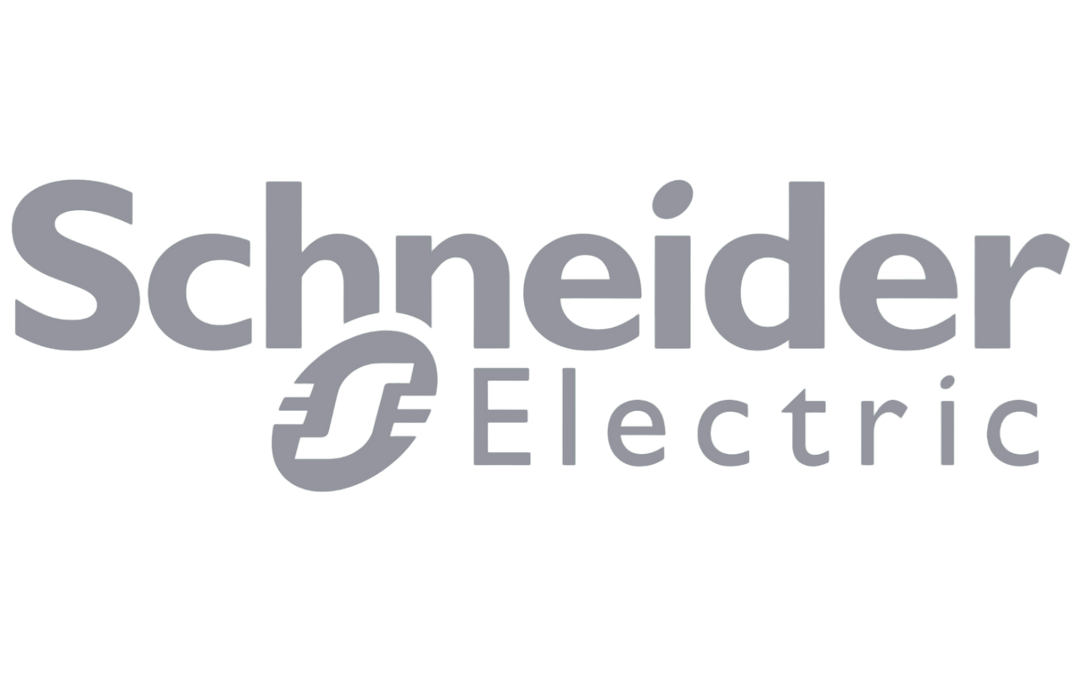
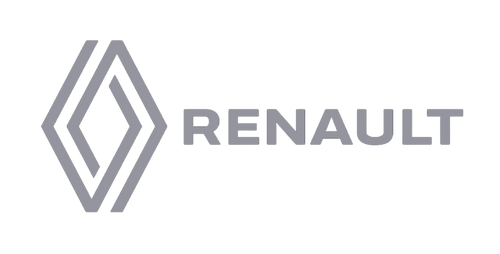
Advantages of manufacturing with LGC Industries
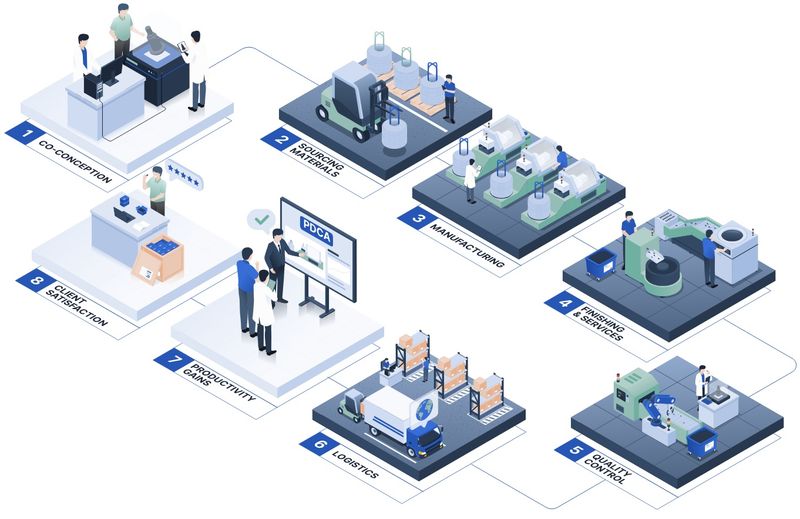
- 45 Escomatic machines
- 42 grooving machines
- 8 plunge & through-feed grinding machines






Find out more about our products' technical features
Discover other products
Bar turning: essential technology for precision machining
Bar turning traces its origins back to the 18th-century French watchmaking industry. The method, known as décolletage in French, comes from the idea of using a machine tool to get rid of the "collar" or collet as it is known in French. The term then evolved to refer to a process enabling production of small mechanical parts through turning, with these parts mainly being intended for use in the automotive, aeronautics and electronics sectors.
Nowadays, bar turning or simply turning is a high-precision machining process involving specialised machines like cam-driven lathes used to mass produce high-precision mechanical parts.
Bar turning has become an essential process in industry, mainly used to machine parts with small dimensions, especially rotating parts like screws, nuts and pins. In bar turning, material is gradually removed from a bar of metal via a cutting tool in order to create high-precision parts.
It is mainly carried on cam-driven lathes, also known as Escomatic machines, which use cams to move the tools around, enabling the bars to be cut.
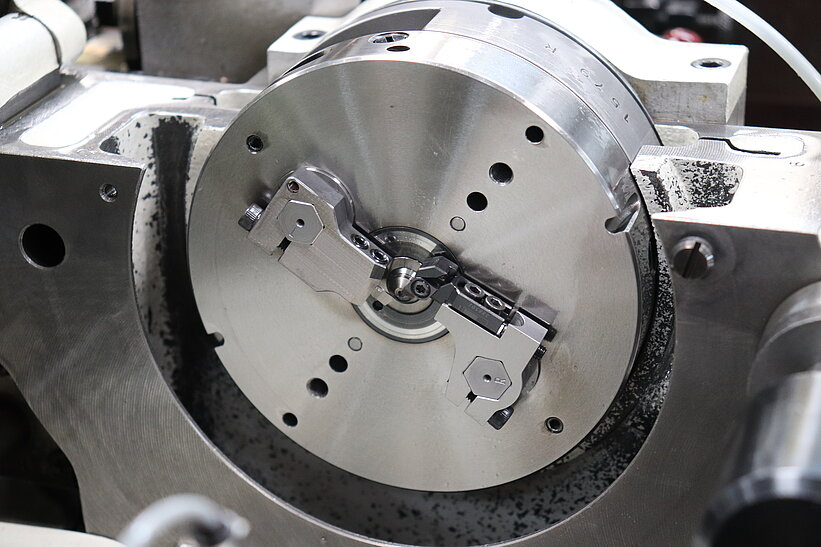
Precision machining with cam-driven lathes
Parts machined through bar turning are usually small in size, ranging from 0.1mm to 60mm in diameter, and require high precision (sometimes as precise as a thousandth of a millimetre). Cam-driven lathes are the standard for this kind of machining, offering a high level of efficiency for small, medium and large production batches.
These machines have a camshaft which generates precise movements in order to move around the tools and carry out different operations such as turning, threading and drilling.
In the case of multi-spindle lathes, several spindles are put in action at once to machine several parts simultaneously, optimising mass production. Such cam-driven lathes are particularly suited to specific series where both maximum precision and productivity are required.
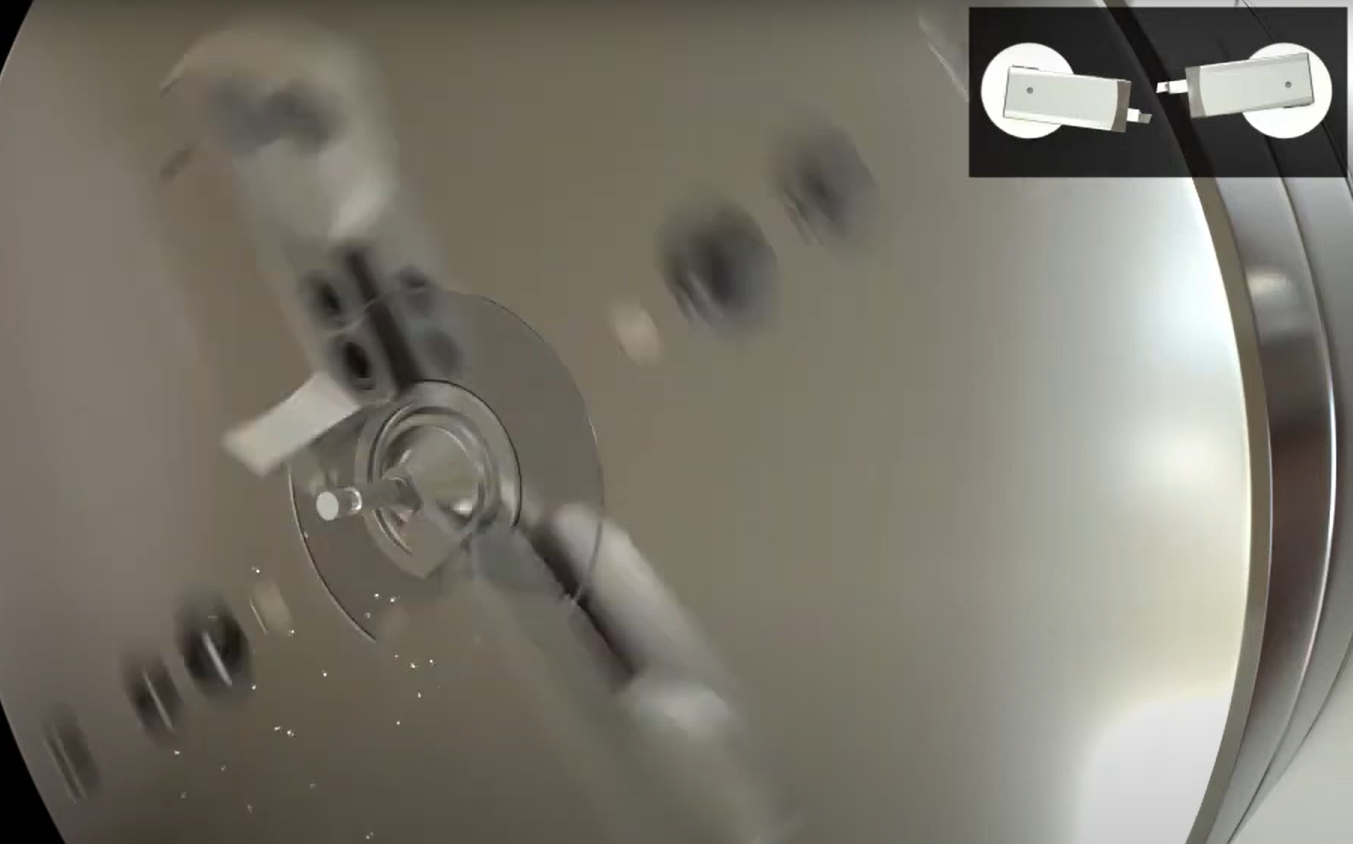
The role of machines in bar turning
Cam-driven lathes or Escomatic lathes are automatic machines used to carry out high-precision machining for small mechanical parts. Such machines can combine several different machining stages in the same cycle, reducing the need for reworking and optimising production.
These lathes operate thanks to the movement of their cams, which move the tools around, enabling operations like turning, threading and drilling, while also maximising productivity.
CNC machines are also used, although they are less widespread than cam-driven lathes when it comes to bar turning. These machines allow for greater flexibility since they are programmed by a computer, but they are not as common as cam lathes for producing small batches or specific parts.
Materials used for bar turning
Materials used in bar turning are often chosen for their machinability. Brass and steel are commonly used, often in forms specially designed for turning.
These materials are chosen not only because they are easy to machine but also for their technical characteristics, such as corrosion resistance (for medical devices) or adherence coefficient (in watchmaking).
Industrial applications for bar turning
Turning has uses in various industries, such as the automotive, aeronautics, electronics and medical sectors. Thanks to the flexibility of the cam & multi-spindle lathes, a large variety of high-precision parts can be produced in small or large quantities.
Turning is also used to manufacture components for agricultural machinery, electronic devices, and even for the nuclear industry.
Bar turning in industry
To put it in other words, bar turning has been defined as a "turning operation during which the workpiece is machined from a bar of material from which it is finally separated by a parting operation."
Bar turning began in the Arve Valley, located in the French Alps, in the 18th century. Initially a clockmaking term, it referred to the action of removing the "collet" (the collar - i.e. part of a screw) with a machine tool. From this came the French word "décolletage", which eventually made its way into English as "bar turning" or sometimes "turning" for short.
This process originally aimed to work parts of turned nuts and bolts to be used in clocks and watches.
Later on, with the advent of the automotive sector, followed by computers, bar turning once again became an important branch of mechanics and machining, being used to mass produce large batches of identical turned parts. Today, automatic machines have been developed to speed up this process of machining through material removal.