- 20 million slotted threaded inserts produced each year
- Co-designers of custom fasteners for 100 years and owner of the Intervis® brand
- From M2.5 to M16 and from 6 mm to 22 mm
- Steel (raw, hardened, zinc-plated), stainless steel, brass, etc.
The Intervis® self-tapping threaded insert can be screwed directly into a smooth hole drilled beforehand. The Intervis® insert cuts the thread in the part by itself. It is ideal for installation in medium-hard materials, e.g. light alloys, compressed wood or plastic materials.
Threaded insert with a specific slot - Intervis® made to measure
Threaded insert with a specific slot - Intervis® made to measure
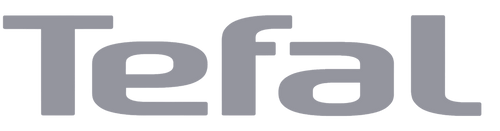
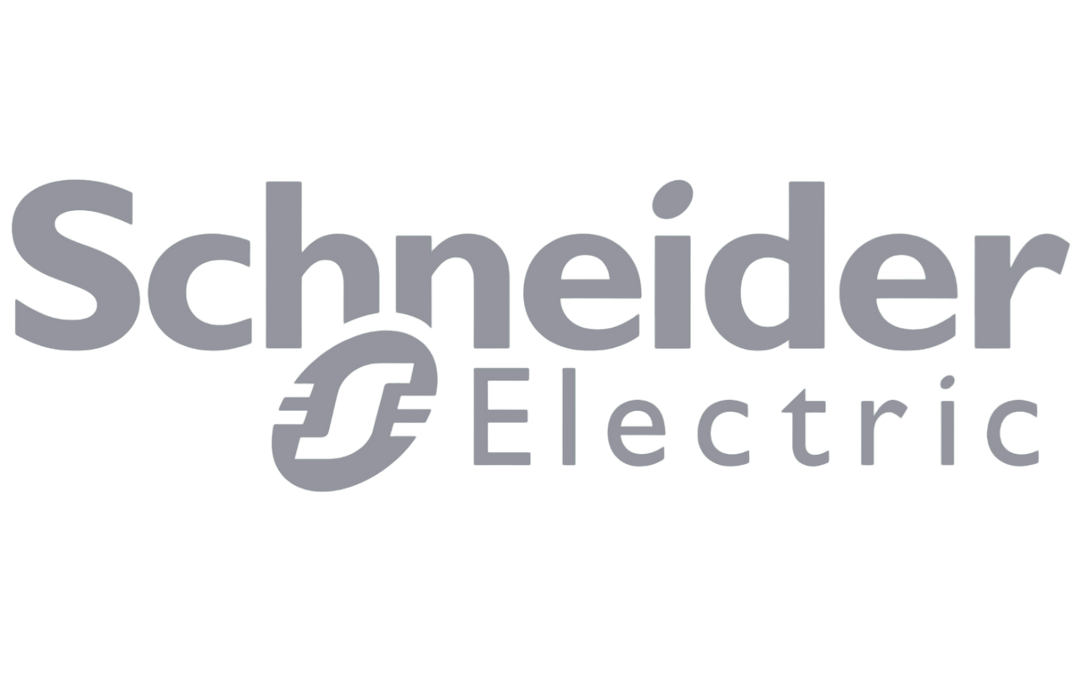
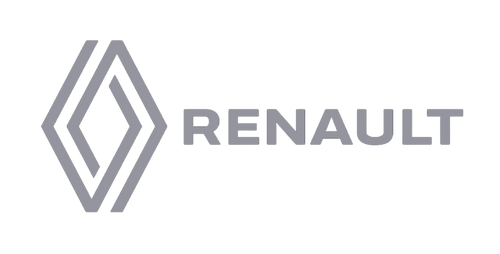
Advantages of manufacturing with LGC Industries
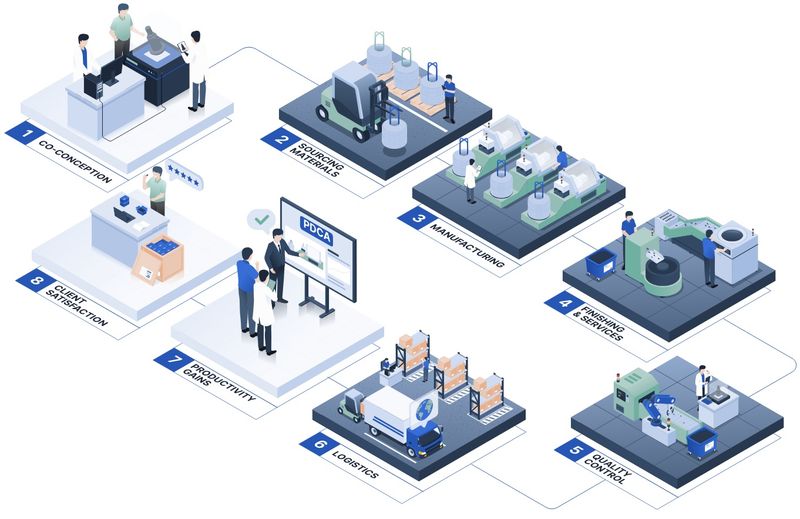
- 45 Escomatic machines
- 42 grooving machines
- 8 plunge & through-feed grinding machines






Find out more about our products' technical features
Discover other products
Choosing the right type of threaded insert
The type of threaded insert you need depends on your application and the specific stresses it must be able to deal with.
Threaded inserts serve various purposes in an assembly:
- Repair: Replacing a damaged or inexistent thread while increasing the assembly's resistance.
- Fastening in soft materials: Ensuring a solid hold in materials such as composites, light alloys and compressed wood, where traditional threads aren't very reliable.
- Instant anchoring: Creating a resistant and long-lasting thread in a material, without any need for special equipment or pre-threading when installing.
The right threaded insert can then be chosen based on these different functions, as well as the installation environment - materials, mechanical stresses, accessibility, etc. The three main insert options are:
- Standard self-tapping inserts
- 3-hole threaded inserts
- Manufacturing made-to-order inserts
Why co-design custom threaded inserts?
LGC can help you co-design your made-to-order threaded inserts so that they perfectly match your requirements.
This collaborative process between the client and ourselves allows us to optimise the insert's performance, reliability and integration into the surrounding environment.
Co-designing custom inserts offers the following advantages:
- It allows for the design of inserts that are perfectly suited to the project's mechanical, geometrical or environmental stresses. Whether it's specific materials, high mechanical resistance or compact design, every aspect is taken into consideration right from the beginning of the design phase.
- By working on the dimensions and tolerances right from the get-go, we can better ensure perfect compatibility with the other parts in the assembly, reducing the need for adjustments as well as the risk of production errors.
- By anticipating technical challenges & minimising trial and errors, co-design reduces manufacturing times. It also allows us to limit costs relating to later changes or faults.
- By involving both the manufacturer's technical experts and the client's team in the process, co-design opens up innovative new solutions and possibilities, creating products that meet current standards as well as future needs.