Bar turning is a process used in industry to manufacture high-precision parts.
It involves machining cylindrical parts out of bars or coils through turning or milling them, removing material as you go.
- Turning allows the production of complex and high-precision parts used in many sectors such as automotive, aerospace and electronics.
- Our high-speed CNC and cam lathe machines allow us to work right down to the hundredth, on both medium and long runs.
Bar turning - Precision machining - Made to order mechanical parts
Bar turning - Precision machining - Made to order mechanical parts
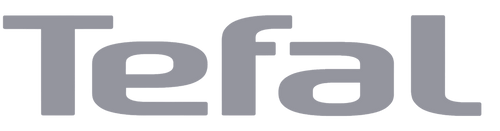
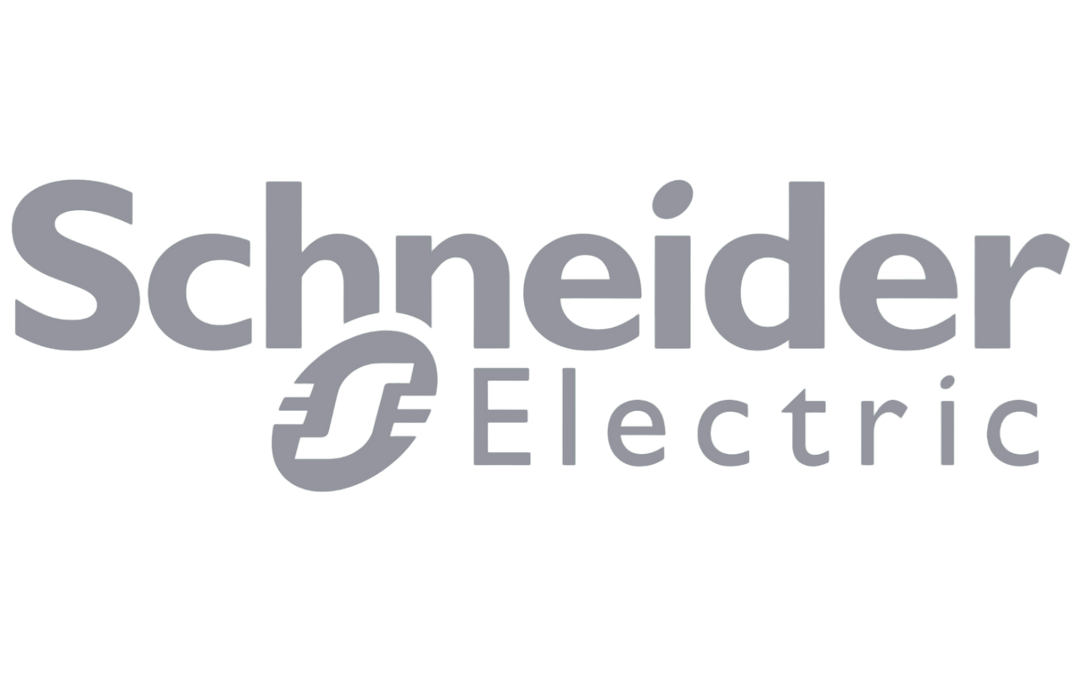
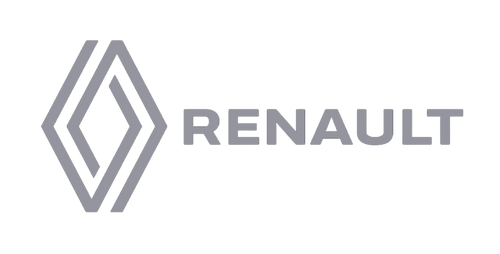
Advantages of manufacturing with LGC Industries
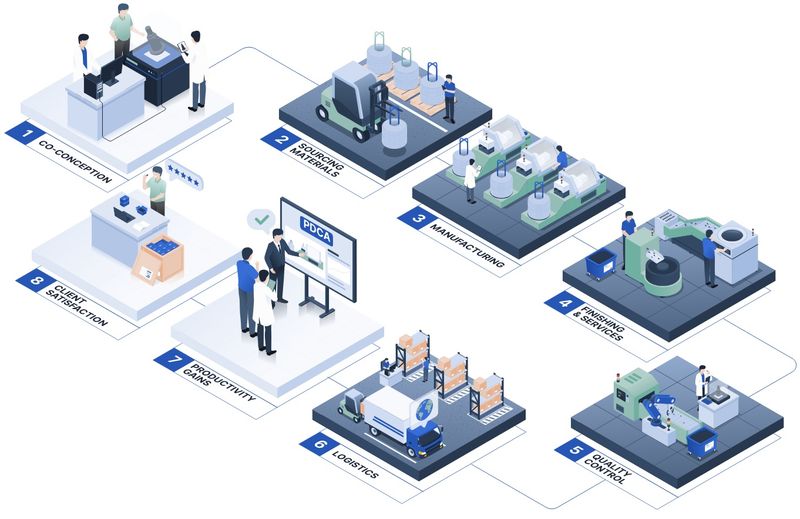
- 45 Escomatic machines
- 42 grooving machines
- 8 plunge & through-feed grinding machines






Find out more about our products' technical features
Discover other products
What is bar turning?
Bar turning is a CNC machining or traditional machining technique used to design and manufacture high-precision mechanical parts by removing material through the rotation of the material and the action of a cutting tool.
Turning is used in a wide variety of fields and on many materials (steel, stainless steel, aluminium, etc.). Turning is used in creating various specific parts for cutting-edge sectors such as aeronautics, medical, nuclear, etc.
Today, companies that specialise in precision bar turning such as LGC use numerical control machines. These new CNC turning machines are controlled by a computer programme and an operator, which makes micro-turning easier.
Turning and precision machining: from prototype to mass production
Precision turning is a highly advanced machining process that consists in giving a precise shape to a part by removing material.
This process is central to our sector and has undergone constant evolution since its beginnings in the 18th century. Over time, it has become increasingly modern with the advent of increasingly efficient and precise CNC machine tools.
Turning has become an essential machining process for creating precision mechanical parts in many different cutting-edge sectors.
At LGC Industries, we have been perfecting the art of mechanical bar turning for over 80 years, consistently exceeding our clients' expectations through our commitment to excellence and the use of new cutting-edge CNC machinery.
What does it mean to "turn" a mechanical part?
Mechanical turning is an innovative machining technique used to produce high-quality custom parts. With ever-increasing demand in many cutting-edge sectors, bar turning has become essential in order to meet constantly changing needs.
Turning - an industrial process used to make mechanical parts such as made-to-order pins, nozzles, bolts, and much more. Using this precise CNC turning technique, the material is carefully removed to transform a raw element into a specific part using a highly efficient CNC tool.
Turning is carried out thanks to our industrial facilities specialised in the design and production of parts by removing material.
These industrial facilities include many different CNC machining tools:
- 24 multi-spindle lathes
- 45 Escomatic machines
- 42 grooving machines
- 8 plunge and thread grinding machines
- 2 cold forming machines
- 3 automatic packaging lines
- 6 optical sorting and metrology machines
- 2 robotic assembly lines
- 1 vibratory finishing and polishing unit
Advantages of bar turning
- Productivity & adaptability: Our turning machines can machine parts from a single unit right up to large quantities in a short period of time.
- Quality & efficiency: Turning machines offer precise dimensions with impeccable finishes thanks to extremely accurate micro-turning machines.
- Saving material and money: The parts are continuously machined, which considerably reduces chips.
- Environment, LGC eco-design: we recycle 86% of our waste (e.g. oil and chips that escape during turning), in particular thanks to our chip extractor machine.
The different CNC machining techniques related to bar turning
Bar turning is a precision machining process aimed at shaping mechanical parts into specific pre-established shapes.
The process includes various machining operations, which we can perform in our workshops:
- Dressing: machining the raw face of a part by moving the tool perpendicularly in relation to its axis of rotation.
- Longitudinal turning: technique which aims to create a cylindrical or conical surface on the outside of the part.
- Drilling: creating holes in a part using a drill.
- Boring: creating a cylindrical or conical surface inside the part.
- Grooving: creation of internal or external grooves for various applications.
- Threading: making a thread in a male part using a specialised tool.
- Tapping: the process of creating a thread inside a hole.
- Chamfering: creating chamfers to eliminate sharp edges.
- Parting: shaping a groove up to the part's axis in order to separate it from the bar.