- Metal precision pins manufactured to the highest standards
- Wide range of dimensions and shapes available: shouldered, indented, chamfered, grooved, etc.
- Recognised know-how with 90 years of experience: IATF 16948, ISO 9001, Q1 Ford.
- Polishing and finishing for elaborate parts.
LGC Industries offers metal pins and custom precision pins designed in collaboration with our customers to meet their specific fastening or guidance requirements. Our custom parts are manufactured according to the highest quality standards to ensure their durability and reliability.
Pins: LGC, precision parts manufacturer
Pins: LGC, precision parts manufacturer
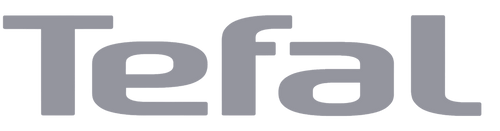
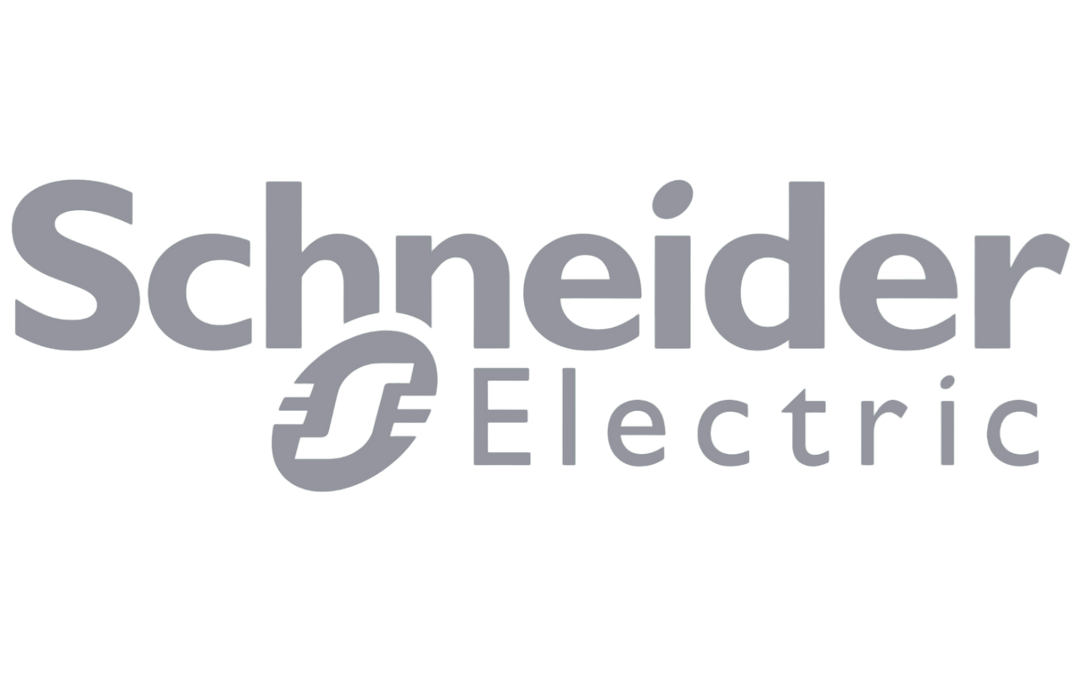
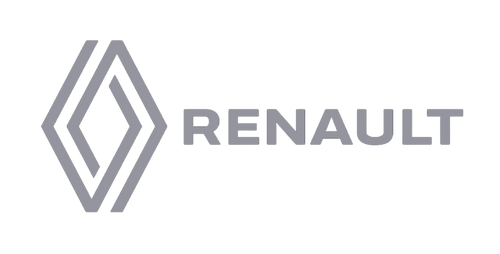
Advantages of manufacturing with LGC Industries
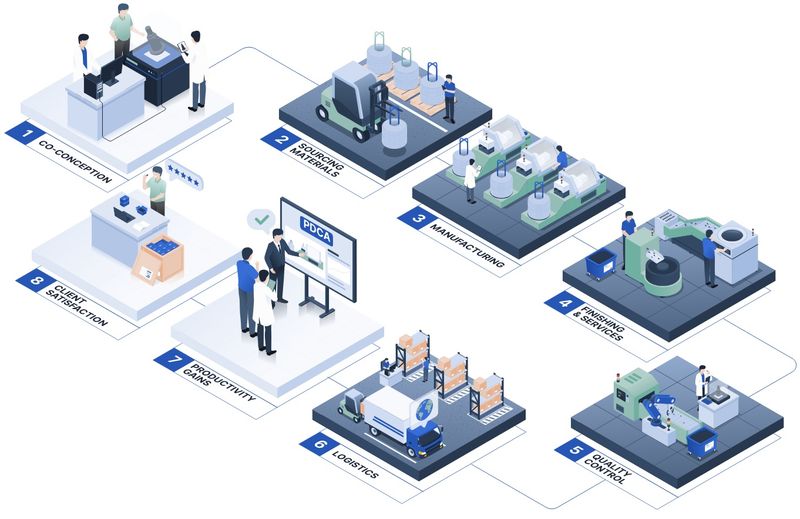
- 45 Escomatic machines
- 42 grooving machines
- 8 plunge & through-feed grinding machines






Find out more about our products' technical features
Discover other products
Precision turning and machining: from raw material to the ideal mechanical pin
The manufacture of mechanical pins is based on machining processes by removing material, transforming a raw part into a pin (metal shaft) perfectly tailored to the required dimensions and specifications.
At LGC Industries, we specialise in several machining techniques, especially in traditional mechanical and CNC processes such as:
- Turning
- Milling
- Drilling
- Bar turning on cam towers
Bar turning: a tried and tested method for precision pins
A key technique since the 18th century, mechanical bar turning on cam towers remains an essential process for manufacturing metal pins of exceptional precision. This approach, tried and tested over decades, can be suited to even the most demanding sectors, such as:
- Aeronautics
- Cars
- Electronics
This process is an ideal solution for producing precision pins with complex geometries and high quality finishes.
Historical expertise in pins manufacturing
For more than 90 years, LGC Industries has entrusted specialised mechanical equipment, such as cam towers and other traditional machines, with manufacturing our made-to-measure metal pins. Our know-how allows us to co-develop bespoke solutions with our customers - perfectly adapted to their needs, all while maintaining a constant focus on quality and precision.
Facilities dedicated to the production of metal pins
To meet even the most demanding requests, our factories are equipped with mechanical and specialised machines, including:
- High-quality cam towers
- Grinding machines for perfect finishes
- Grooving machines for specific shapes
- Equipment for assembly and quality control
Co-design and quality commitment
At LGC Industries, co-designing is at the heart of what we do. Each project is unique, which is why we work closely with our customers to design tailor-made precision pins, adapting to their requirements in terms of performance, dimensions and materials.
Our metal pins are manufactured according to the most stringent standards:
- ISO 9001
- ISO 14001
- IATF 16948
A responsible approach
In addition to our commitment to quality, we attach great importance to sustainability. We favour recyclable materials and implement practices aimed at reducing industrial waste.
With LGC Industries, you can be sure that you're getting mechanical pins that are reliable, sustainable and environmentally friendly, adapted to the requirements of even the most advanced sectors.