- 150 million ground pins produced each year
- Co-designers of custom fasteners for 100 years and manufacturer of standard products: ISO 8734 or din 6325
- From Ø1.5 to Ø25 and from 8 mm to 100 mm
- Steel (free cutting, heat-treatable, carbon, alloys...), stainless steel (CNF or DNC), aluminium, brass, etc.
Ground pins are often used in applications where accurate fastening is essential, such as machine tools, measuring equipment, and medical devices.
Ground cylindrical pin - DIN 6325 - ISO 8734
Ground cylindrical pin - DIN 6325 - ISO 8734
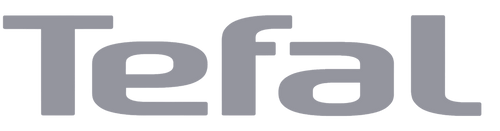
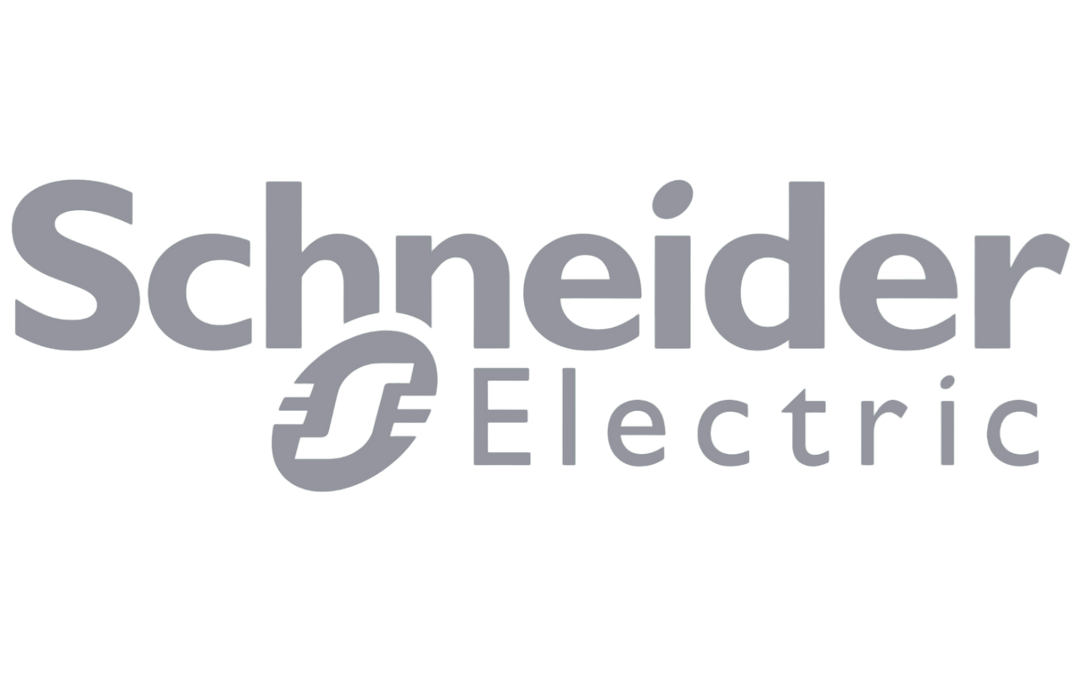
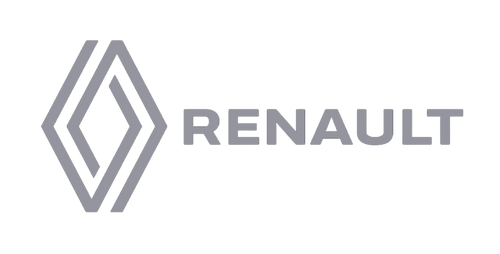
Advantages of manufacturing with LGC Industries
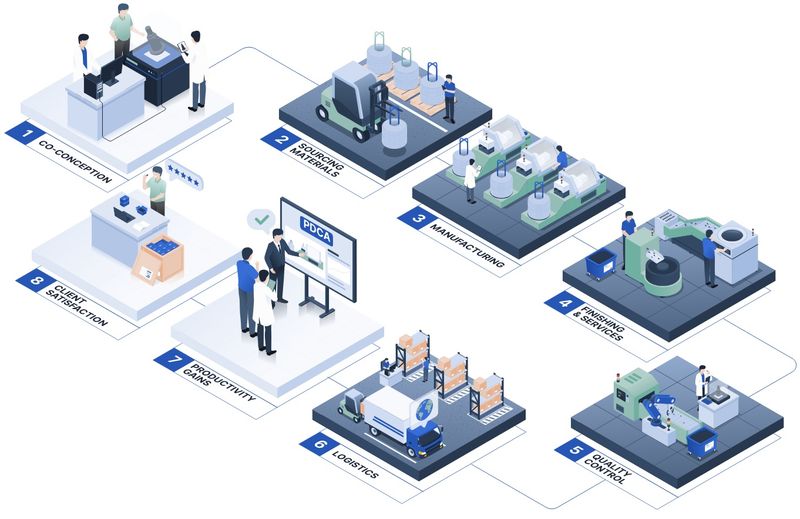
- 45 Escomatic machines
- 42 grooving machines
- 8 plunge & through-feed grinding machines






Find out more about our products' technical features
Discover other products
What is a ground part?
A ground part is a part that has undergone a machine finishing stage called “grinding”. This treatment involves removing material from the part using a grinding wheel in order to get the desired dimensions and shape.
Ground parts are synonymous with precision as they are used in cases with strict tolerances and requirements.
The grinding wheel comes into contact with the cylindrical pin. It is a disc or strip of abrasive material that can be made out of:
- Corundum: capable of machining a wide variety of materials including plastic
- Diamond: used to machine very hard materials such as ceramics or hardened steels.
- Silicon carbide: used for hard materials such as steel.
At LGC, we offer different types of grinding wheels, each of which has its own specificities when grinding:
- Cylindrical grinding wheels: for classic cylindrical surfaces, e.g. cylindrical pins.
- Conical grinding wheels: for conical surfaces, like conical pins.
- Flat grinding wheels: for flat surfaces.
Ground cylindrical pins can be of any shape but there are standards that correspond to different standard pins. For the ground cylindrical pin, for example, these standards would be DIN 6325, ISO 8734 and DIN 7.
What is a ground cylindrical pin?
A ground cylindrical pin (in some contexts, parallel pin) is a cylindrical pin that has gone through a grinding process, allowing it to satisfy customer requirements and meet to DIN 6325, ISO 8734 and DIN 7 standards.
Since this pin is used in very specific industry sectors with very strict requirements, the pin is ground right to the micron.
Ground cylindrical pins can be used for various applications, such as:
- Machine tools
- Measuring equipment
- Medical devices / instruments.
How are LGC's ground pins made?
The LGC method for manufacturing ground cylindrical pins is similar to the way other pins are manufactured since the main stages are the same:
- 1st stage: as for all pins, the first step is cutting the bars of raw material. Generally, steel is used for ground cylindrical pins.
- The 2nd step is a CNC machining process called bar turning. This process from the turning family involves rotating the material, bringing the cutting tool(s) closer until they come into contact with the rotating material. Thin layers of material are successfully shaved off in order to obtain the desired pin shape.
- The 3rd step is grinding. This is when the pin goes between the grinding wheels in order to obtain a diameter of a certain micron and a high-quality surface finish. This process allows us to produce ground cylindrical pins that are in line with DIN 6325, ISO 8734 and DIN 7 standards.
- In the 4th step, LGC carries out a quality control at the end of the ground cylindrical pin's manufacturing process, using high-tech measurement tools and our workers' know-how (tools used: 3D lab, proofing machine, digital profile projector).
Once these four steps have been completed, we ship the parts to the customer via low-CO2 emission transport.
What are the advantages of ground cylindrical pins?
When say ground cylindrical pin, we are referring to the DIN 6325 or DIN 7 ground cylindrical pin, as well as the ISO 8734 standard ground cylindrical pin or ISO 2338 cylindrical pin.
What is the difference between these two pins?
These two pins are identical, the only thing that differentiates them is the name of the standards. The DIN 6325 cylindrical pin refers to the German standard while the ISO 8734 cylindrical pin is the international standard.
These standards may have different names but the advantages of each are the same:
- Precision: the precision offered by grinding ensures precise positioning of the pin in the assembly, ideal for axes of rotation or for positioning cylinder heads for example.
- Resistance: after the grinding process, ground cylindrical pins become considerably more resistant to wear and tear, as their surface roughness decreases - this reduces friction which in turns means less maintenance.
- Comfort: the smooth surface of a ground cylindrical pin reduces noise and vibration during sliding or rotation.
- Aesthetics: one benefit of grinding is improving the pin's appearance, offering a shiny, smooth surface.
- Standard product: Although LGC can also meet any particular requirements you may have with custom-made ground cylindrical pins, the fact that this pin is recognised by DIN 6325, ISO 8734 & DIN 7, ISO 2338 standards makes it a reference of choice.
What are the existing standards for ground cylindrical pins?
Standards, whether German (DIN) or international (ISO), define certain criteria regarding the materials, dimensions and mechanical properties of cylindrical pins, thus ensuring their safety and reliability.
We can produce (ground) cylindrical pins to the following DIN and ISO standards:
- DIN 6325 or ISO 8734: ground cylindrical pin
- DIN 7 or ISO 2338: cylindrical pin