Pins are cylindrical parts used to assemble and position two or more parts together, be it temporarily or permanently.
We manufacture solid pins and grooved pins that are part of the spring pin (AKA spiral dowel pin) family.
- Grooved pins can deal with greater mechanical shear stresses than standard spring pins.
- Solid pins are used in applications where adjustment tolerance is required to obtain a good hold.
- As they are more precise to machine, they are more expensive to use it in an assembly.
Our teams will help you make the choice between a spring pin, grooved pin and a solid, precision pin.
Pins - mechanical pins, groove pins, cylindrical pins
Pins - mechanical pins, groove pins, cylindrical pins
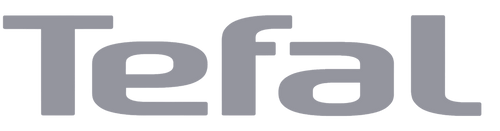
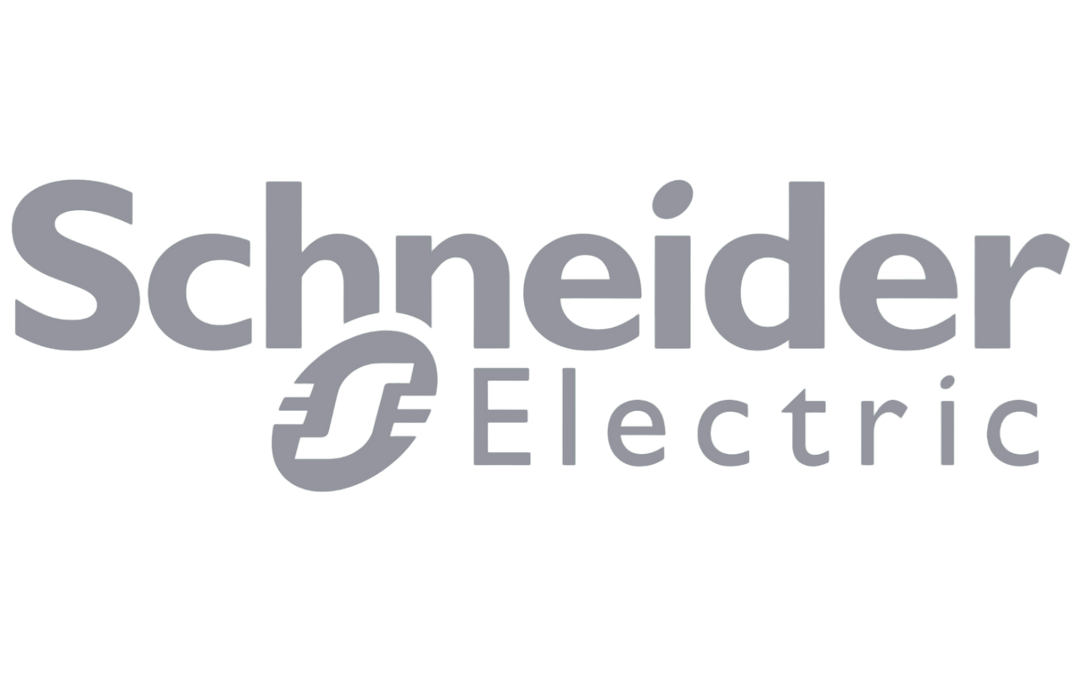
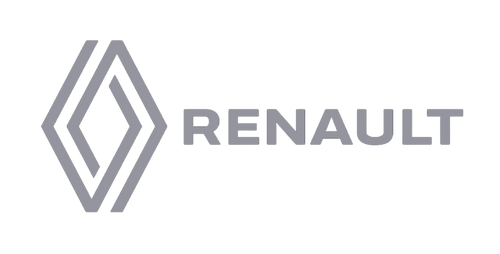
Advantages of manufacturing with LGC Industries
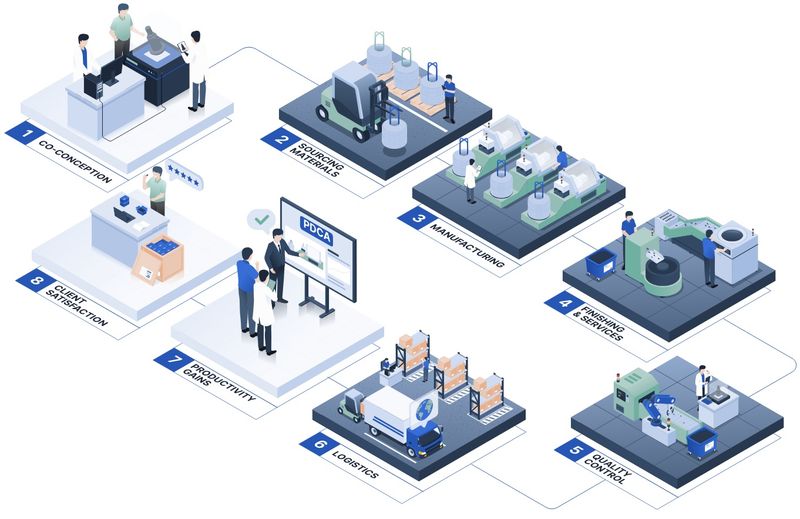
- 45 Escomatic machines
- 42 grooving machines
- 8 plunge & through-feed grinding machines






Find out more about our products' technical features
Discover other products
What are pins?
Pins are mechanical elements mainly used to keep parts together within an assembly.
Usually cylinder-shaped, pins are designed to be inserted into holes or slots in order to secure structures or mechanisms.
Thanks to their versatility, their ease of assembly and their mechanical features, pins are essential in many industries.
How are pins made?
There are many different methods and several highly efficient machines used to manufacture pins. In this section, we'll take a look at LGC's own pin design process.
To start with, one of our machines shapes the pin. The pin is shaped out of a metal bar or coil, with the metal being determined depending on your needs (pins can come in stainless steel, steel, aluminium, brass, etc.).
Stages in manufacturing a pin
- Material enters the machine (in the form of a bar or coil)
- The machine cuts the bar to the desired dimensions
- Part is submitted to one or several surface finishing operations, either internally or by external collaborators.
- The part is cleaned, and may also be oiled to shield it from corrosion during transport.
Depending on the type of pin required, other procedures can be added to the machining process, e.g. chamfers, undercut, shouldering, grooves or other specific shapes.
As well as this, the pin can also undergo surface treatments - depending on your needs and desired application. Tribofinishing and grinding allow us to reach your ideal level of surface roughness and tolerance range. Using these two surface finishing processes, we can reach tolerance ranges of just a few microns.
We also offer a wide range of heat treatments, depending once again on the pin's future application and environment. Some of the most common heat treatments include quenching and tempering, which allow us to modify the material's internal make-up, thus acquiring the desired crystalline structure and HRC / HV hardness.
Apart from these, we can also provide other surface treatments, such as:
- Phosphatising
- Chromating
- Galvinising (Zinc coating)
- Carburising
- Nitriding
- Carbonitriding
- Nitrocarburising
What purposes do pins serve?
Mechanical pins are designed to be used in response to counter relatively low shear forces.
Pins are used to:
- Immobilise one part relative to another - solidity
- Position one part relative to another - positioning
- Act as an axis within an assembly - rotation
- Serve as a safety piece in an assembly
They can be found in many different assemblies:
In the automotive sector, they are used inside planetary gearsets in order to regulate coolant flow and manage the vehicle's temperature, as well as in car door assemblies.
In the medical sector, they are used in oxygen regulator valves, for example.
What types of pins are there?
At LGC, we design and manufacture ISO-standard mechanical pins, such as:
Smooth pin or cylindrical pin DIN 7 / ISO 2338
The standard cylindrical pin par excellence - ideally suited to less rigorous assemblies, it requires good assembly tolerance. The DIN 7 / ISO 2338 pin is often used in simple assemblies that don't need extreme precision.
These pins' design means they can be machined to have chamfered or curved ends, depending on your specific requirements and application.
The choice of material, tolerances and dimensions is left to the client during the co-design phase, in order to perfectly meet their requirements.
Ground pin DIN 6325 / ISO 8734
The difference between this type of pin and a smooth (cylindrical) pin is the tolerance for toutside diameter and surface roughness.
Their extremely high precision allows the pin to be perfectly adjusted in its housing. They are manufactured with micron-sized precision, with exceptional surface roughness (0.3>Ra>0.2). DIN 6325 / ISO 8734-standard ground pins are commonly used in applications where assembly precision is paramount, such as machine tools, measuring equipment and medical devices.
Grooved pin DIN 1470 / ISO 8739 to DIN 1475 / ISO 8742
We have been experts on this extremely technical pin for over 90 years.
Groove pins are cylindrical fasteners with a series of lengthways grooves that can bend and compress the pin. Generally, these pins have three grooves, each one at a 120° angle.
Unlike ground pins, grooved pins don't require any kind of specific adjustment tolerance, since the grooves' elasticity allows them to adapt to the diameter of the hole in which they are inserted. Its bulge diameter, slightly higher than the nominal diameter, allows the pin to fit tightly and to stay firmly in place. This type of pin is often used in applications where strong holding power is needed, but also in applications exposed to strong vibrations, like drivetrains in automobiles. Want to learn more about grooved pins? Take a look at our article on the topic: Everything you need to know about grooved pins
Co-designed, made-to-measure pins; turned pins
Mechanical pins can undergo a specific bar turning operation in order to create the deal pin for the individual needs of our clients and their projects.
Through bar turning and machining operations, we can customise pins' geometric specifications - through undercuts, flat spots, longitudinal turning, threads, milling, etc., in order to meet the specific requirements of each client. Some pins, depending on how they've been turned, can be overmoulded into injected plastic in certain applications. However, most of our clients' applications mainly involve high-quality metal alloys.
How do I pick the ideal pin for my needs?
Finding the pin best suited to your need depends on several factors, such as:
- Mechanical stresses applied in your assembly
Know the type of stress the pin will be under, for example:
- Traction: opt for a smooth pin.
- Vibration: a grooved pin is best suited.
- Bending: increased diameter
- Fatigue: increased hardness
- Type of fastening - choose according to your application requirements and how the pin needs to fit into its housing
- Diameter and length
- Material used - your chosen material must be able to respond appropriately to mechanical stresses in the application and its environment (e.g. corrosion resistance)
- Assembly strength class, where applicable
Choosing the right pin means ensuring a reliable and long-lasting mechanical assembly. Need advice? Please don't hesitate to get in contact with our technical experts.
What are the equivalents of different standard pins (DIN and ISO)?
These standards, whether they are German (DIN) or international (ISO), lay out certain criteria regarding the materials, dimensions and mechanical properties of pins, ensuring that they are both safe and reliable.
Here are the different standard pins we produce, in both DIN and ISO format:
- Smooth cylindrical pin
- DIN 7 aka ISO 2338
- Ground cylindrical pin
- DIN 6325 aka ISO 8734
- Grooved pin
- DIN 1470 aka ISO 8739
- DIN 1471 aka ISO 8744
- DIN 1472 aka ISO 8745
- DIN 1473 aka ISO 8740
- DIN 1474 aka ISO 8741
- DIN 1475 aka ISO 8742
Need any more information on pins? Have a look at our basic guide to pins.