- 150 million grooved pins produced each year
- Co-designers of custom fasteners and manufacturer of standard products for 100 years
- From Ø1.5 to Ø25 and from 8 mm to 100 mm
- Steel (free-cutting, heat-treatable, carbon, alloys...), stainless steel (303, 316, 420...) aluminium, brass, etc.
The grooving process used to make LGC's grooved pins and nails allows for a modern fastening solution that is simple, economical, safe and easily dismantled, offering a practical solution for any possible assembly, connection, or drive issues that one may encounter in many sectors of industry.
Grooved pin: steel, stainless steel, aluminium, brass
Grooved pin: steel, stainless steel, aluminium, brass
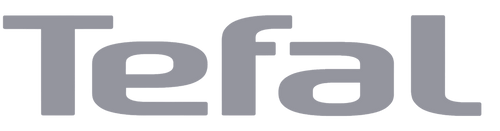
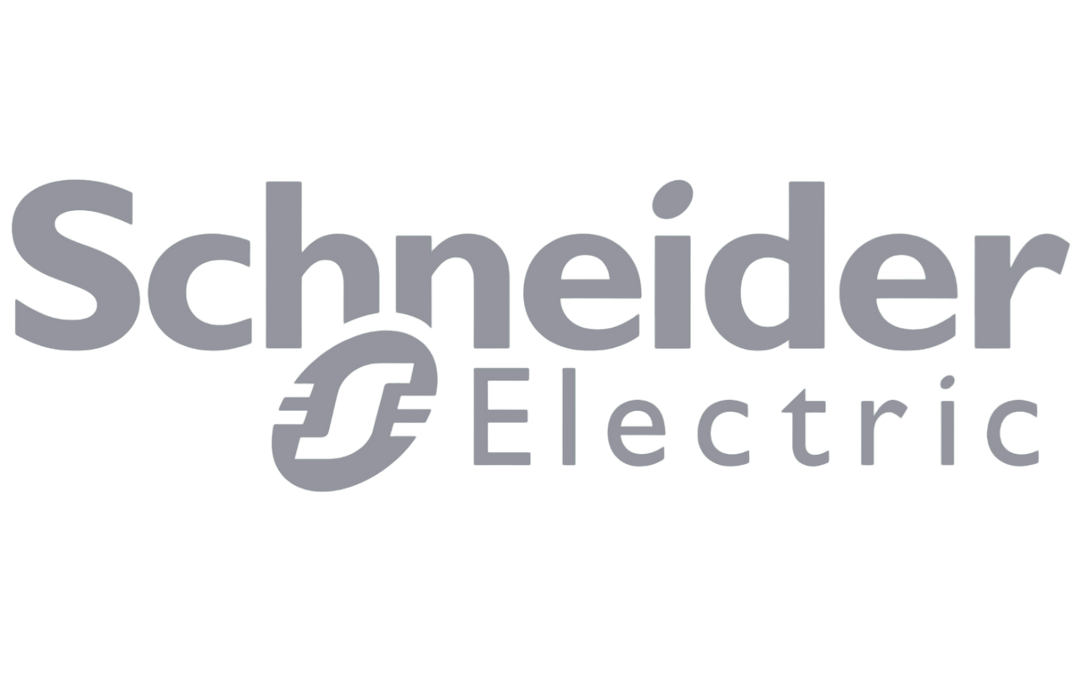
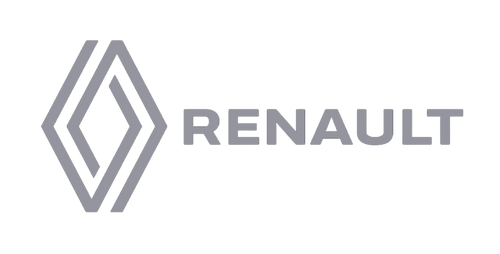
Advantages of manufacturing with LGC Industries
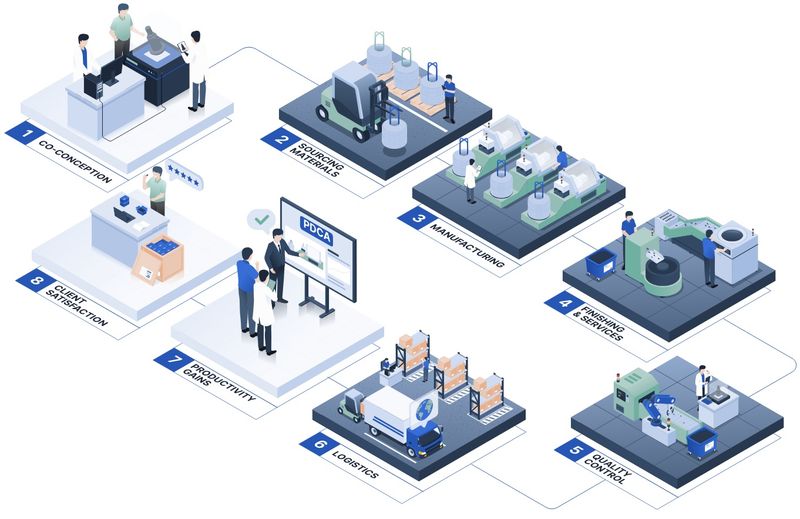
- 45 Escomatic machines
- 42 grooving machines
- 8 plunge & through-feed grinding machines






Find out more about our products' technical features
Discover other products
What does it mean for a part to be "grooved"?
A grooved part is a component with grooves on its surface. These grooves are positioned parallel to each other on the part, usually lengthways. The grooves on our parts are created by a groove machine after the bar turning process has ended.
Used in many industrial sectors, grooved pins ensure reliable and solid assemblies.
Grooved pins can have various uses:
- Solidity: Holding two parts together thanks to their machined grooves and the pressure they exert on the hole in which they are inserted.
- Connection & rotation: Grooved pins allow for pivot movement between two elements, like in door hinges.
- Positioning: Grooved pins enable two parts to be positioned relative to each other, in order to then add another fastener, e.g. a screw.
They are often used in applications where a certain holding force is needed (solidity and positioning), like in drive trains in the automotive sector.
What is a grooved pin?
A grooved pin is a cylindrical pin with grooves on its surface.
There can be 1, 2, 3, or 6 grooves on a grooved pin.
The most common type would be a grooved pin with 3 120° grooves, allowing for even distribution of forces in the receiving component. Grooving is also the easiest process to set up on a grooving machine.
The grooves clench up when the pin is inserted into its housing, which creates pressure between the grooved pin and the receiving piece. This pressure maintains a tight fit between the two parts. This can be called “elastic limit tightening” because the deformation of the groove remains in the range of elastic deformation of the material. This type of fit is more effective than a H7/p6 fit.
Fitting a grooved pin could be compared to bracing.
LGC designs and manufactures custom grooved pins but there are also industry standards for pins, allowing for easy reference:
- ISO 8739, ISO 8740, ISO 8741, ISO 8742, ISO 8743, ISO 8744, ISO 8745.
- Their DIN standard equivalents are: DIN 1470, DIN 1471, DIN 1472, DIN 1473, DIN 1474, DIN 1475, DIN 1476
How are LGC grooved pins made?
Grooved pins are some of the most technical pins to make. Fortunately, we have 90 years of expertise to help us.
The LGC method of manufacturing grooved pins consists in cutting a bar or wire - made of the desired material - to the required dimensions.
Once the bar or wire is cut, we place the pins into one of our 30 grinding machines, been custom designed to optimise performance as well as the quality of our pins.
The machine cuts to the right dimensions and creates grooves on the pins with precision using two types of tools called "nails" and "dies".
Once out of the grinding machine, the pin can be cleaned and oiled to protect it from corrosion during transport.
What types of grooved pins are there?
There are many different types of grooved pins, each one with its own particular features, such as:
- Grooved pin ISO 8739, DIN 1470: constant grooves along its entire length, with pilot point.
- Grooved pin ISO 8740, DIN 1473: constant grooves along half its length, with pilot point.
- Grooved pin ISO 8741, DIN 1474: non-through / stopped grooves along half its length.
- Grooved pin ISO 8742, DIN 1475: central grooves along a third of its length.
- Grooved pin ISO 8743, DIN 1476: central grooves along half its length.
- Grooved pin ISO 8744, DIN 1471: constant groove along its entire length.
- Grooved pin ISO 8745, DIN 1472: through grooves along half its length.
"Through" means that the mechanical groove juts out beyond the pin.
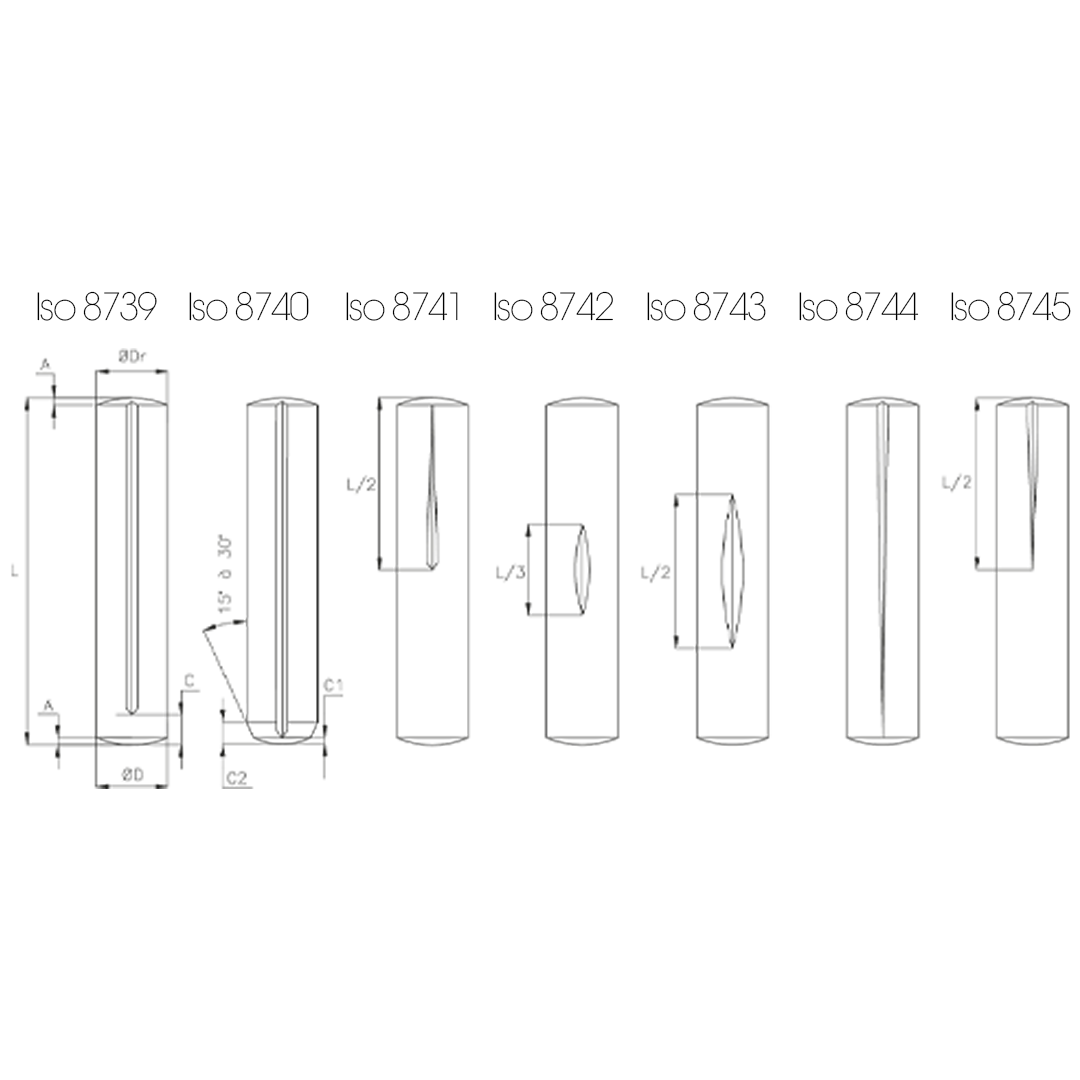
The type of pin to use depends on your needs. There are various types of grooved pins, but they all essentially offer the same advantages, such as:
- Solidity: the grooves on a grooved pin allow for solid and simple assembly since grinding and boring operations are not needed.
- Vibration absorption: grooved pins offer high resistance to vibrations, unlike simple, slotted or elastic pins which can sometimes travel (leave its housing).
- Positioning: grooved pins are used to position mechanical components at a lower cost, as precision operations are not required.
- Securing the part: the grooved pin is used as a safety element in an assembly, preventing the parts from coming loose.
How are grooved pins installed?
It is essential to properly install grooved pins in order to keep two parts together.
You must first make sure to choose the right pin for the hole's diameter and for the assembly parts' technical features.
Once you've find the right pin for your assembly, you'll need:
- A hydraulic or electric press - grooved pins are best suited for industrial applications, which means you should have at least a tonne of force at your disposal to install them.
- Something to remove the old pin with, if replacing.
Once the tools are ready, carefully prepare your parts. The holes should be cleaned of any grease, dirt or debris that may interfere with the install. In some cases, a dowel hole (boring) can be helpful for inserting the pin into the hole.
Finally, align the assembly parts in such a way that one hole is on top of another.