- 35 million spacers produced each year
- Co-designers of custom fasteners for 100 years and manufacturer of standard products
- From M6 to M10 and from 6 mm to 30 mm
- Steel, stainless steel, brass, etc. (other materials are available on request).
These smooth compression spacers are found in industrial fields, including the automotive industry, and particularly in intake manifolds or air conditioning connections.
Smooth spacer - compression spacer
Smooth spacer - compression spacer
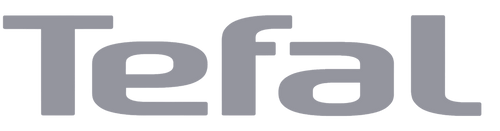
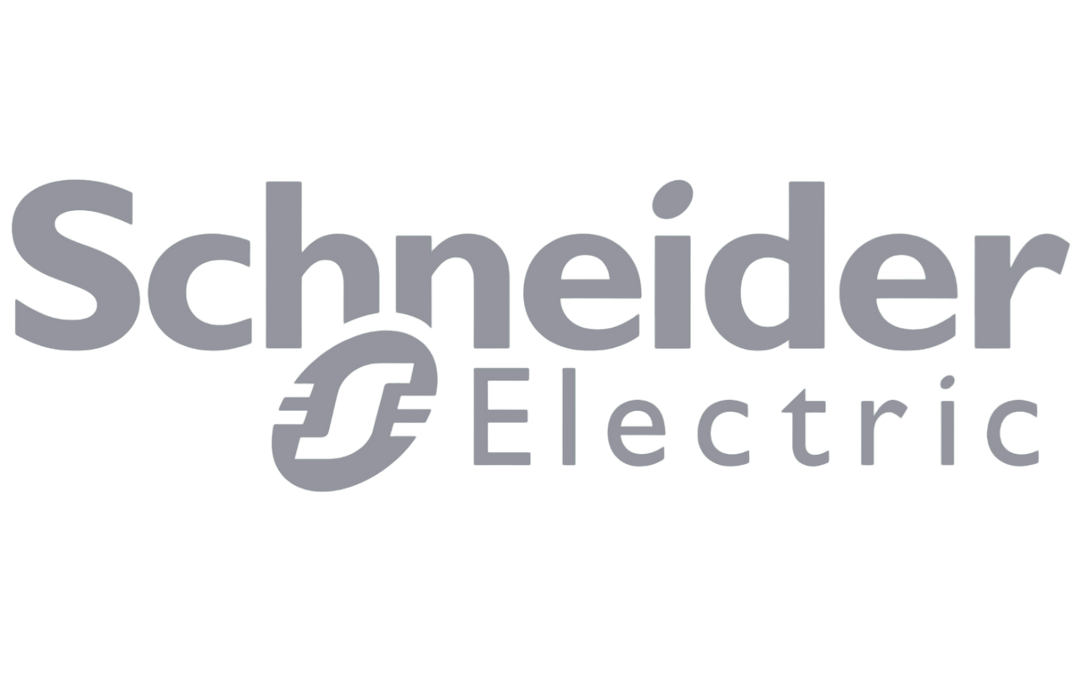
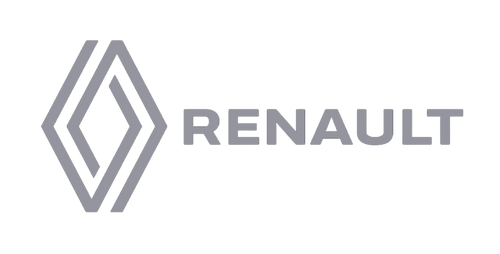
Advantages of manufacturing with LGC Industries
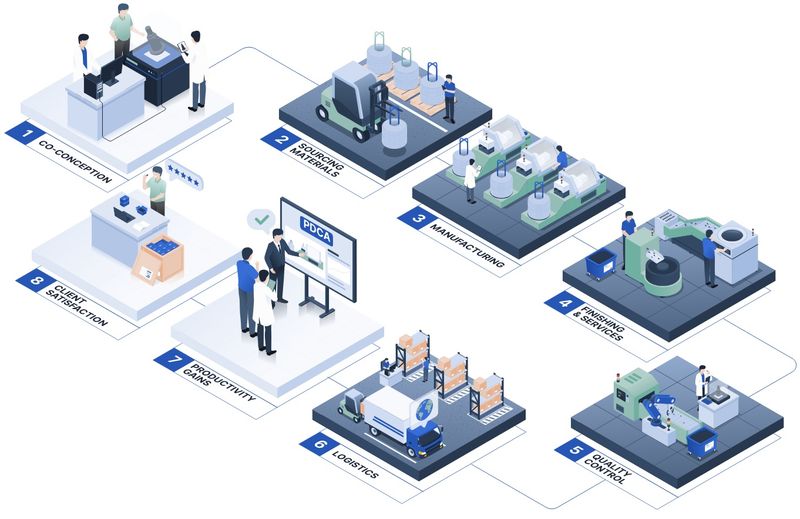
- 45 Escomatic machines
- 42 grooving machines
- 8 plunge & through-feed grinding machines






Find out more about our products' technical features
Discover other products
Protect your part assemblies with a smooth cylindrical spacer
Spacers, also commonly called “dowel pins”, "bushes" or "sleeves", play an essential role in mechanics and industrial assemblies. They guarantee the precise positioning of the components, thus reducing the risk of deformation or unwanted movement. These small parts, often overlooked, can have a significant impact on a mechanism's overall performance.
The often-underestimated smooth cylindrical spacer, smooth cylindrical spacer or compression dowel pin offers remarkable robustness.
Its cylindrical structure not only provides structural stability, but it is also highly resistant to mechanical stress.
Smooth spacers are specially designed to absorb significant loads and maintain the integrity of the parts in an assembly. Their sturdy design makes them an essential choice for projects requiring increased resistance to compression forces.
What is a smooth spacer or compression socket?
Smooth compression spacers are cylindrical fasteners designed to protect assemblies of mechanical and plastic parts against compression forces.
They are specially designed to be used after the moulding or overmoulding of plastic parts in order to prevent deformation.
Thanks to their solid and durable structure, these spacers make it possible to compensate for dimensional variations that occur during thermal shocks or mechanical forces in an assembly.
In short, smooth cylindrical spacers are a reliable and effective solution to ensure stable and long-lasting metal and plastic assemblies, all while maintaining their integrity.
These spacers are found in industrial fields including the automotive industry and particularly in intake manifolds or air conditioning connections.
How are LGC cylindrical spacers made?
There are two different ways of making a cylindrical spacer.
From pin to cylindrical spacer
It is possible to start from a solid material that has been machined in order to then give it the shape of a pin. In this case, it is necessary to drill a hole in the pin to make it hollow - this is called a bore, which complicates the process not only financially and technically, but also environmentally.
From tube to cylindrical spacer
It is also possible to make a compression spacer or socket from a tube.
We highly recommend tubes for this as they perfectly satisfy all criteria (price, quality and carbon footprint).
This is the technique we use here at LGC.
The first step in manufacturing a spacer is cutting the raw material, which comes in the form of long, hollow tubes. The material and the diameter depend on the desired final part.
The tube enters a machine which cuts it to the desired length.
The part can be further machined using specialised machines.
For example, chamfers may be required, or surface finishes may be applied to your spacers.
The part then goes through a grinding process.
A die presses the parts against a grinding wheel rotating at high speed. Through abrasion, this wheel modifies the diameter of the part to reach tolerances of several microns (~5-6 μm).
What are the advantages of cylindrical spacers?
- Load absorption: the smooth spacer / compression sleeve is designed to absorb and distribute loads effectively, reducing pressure on adjacent components. This ensures an even distribution of stresses, preventing deformations and maintaining the integrity of the assembly.
- Stability: by maintaining structural stability, the smooth spacer/compression dowel pin (bushing) helps prevent deformations and potential failures. It reinforces the overall solidity of the assembly, thus ensuring reliable performance over time.
- Vibration reduction: thanks to its ability to absorb vibrations, the smooth spacer/compression dowel improves comfort when using the assembly. This is especially beneficial in applications where excessive vibration can cause premature component wear.
- Shock absorption: smooth spacers / compression sleeves act as shock absorbers, minimising shocks and impacts. This protects fragile components from potential damage, extending the assembly's lifespan.
- Ease of installation: with their practical design, smooth spacers / compression sleeves are easy to install. This ease of installation allows for quick and efficient assembly, reducing downtime during production or maintenance.
- Material compatibility: Smooth spacers/compression sleeves are versatile and compatible with various materials, such as metal, plastic, or composites. This adaptability makes them ideally suited to a variety of industrial applications.
- Dimensional accuracy: By maintaining precise alignment between components, smooth spacers/compression sleeves contribute to maintaining the dimensional accuracy of the assembly. This is crucial in industries where tight tolerances are required.