- 35 million spacers produced each year
- Co-designer of custom fasteners for 100 years and manufacturer of standard products
- From M6 to M10 and from 8 mm to 30 mm (internal diameter adapted to the passage of a screw)
- Steel, stainless steel, brass, etc. (other materials are available on request).
A spacer makes it possible to create space, position several elements or protect the integrity of an assembly by limiting the compression load exerted.
Manufacturing made-to-order spacers
Manufacturing made-to-order spacers
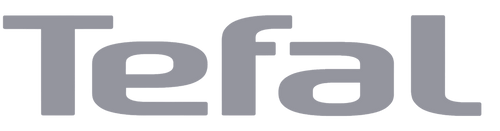
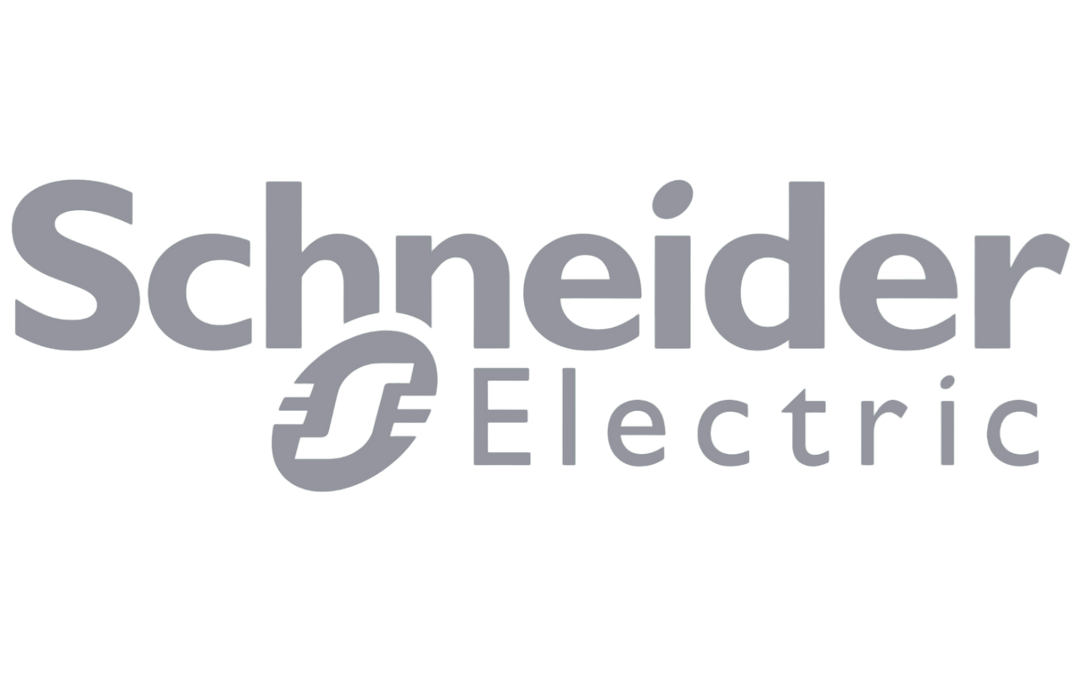
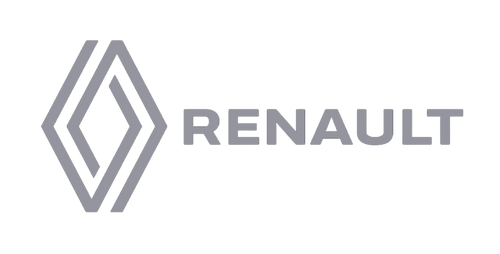
Advantages of manufacturing with LGC Industries
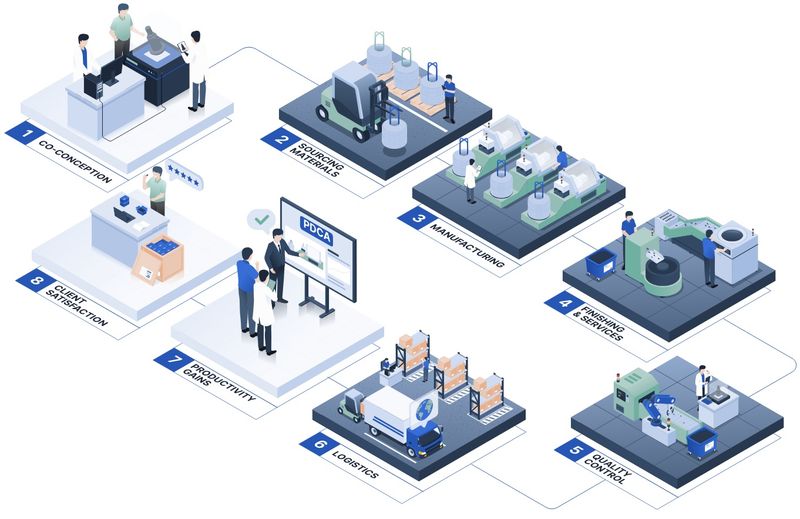
- 45 Escomatic machines
- 42 grooving machines
- 8 plunge & through-feed grinding machines






Find out more about our products' technical features
Discover other products
Co-designing and producing custom spacers
The type of mechanical spacer (aka "bush", "bushing" or "sleeve") you need depends on the purpose it will serve in the assembly.
Custom spacers are used to serve different purposes in an assembly:
- Maintaining space: Spacers can maintain a fixed, precise space between two components, ensuring the assembly's stability. It acts as a "separator" between parts.
- Precise alignment: Spacers allow two parts to be perfectly centred or aligned in relation to each other, which can be useful in moving mechanisms that require high precision.
- Reducing friction & distributing loads: Thanks to its sturdy design (metal), spacers can support and distribute loads of up to a tonne without any deformation.
The type of cylindrical metal spacer best suited to your project will depend on factors such as surface finish, material, and mechanical properties.
Stages of co-designing custom spacers at LGC
Co-designing made to order spacers is a structured process, combining technical know-how and an understanding of the client's specific requirements. Each step in the co-design process contributes to finding a solution that is perfectly suited to the assembly's mechanical and functional specifications.
The first step involves gathering any key information about the end application:
- Purpose of the spacer: Maintaining space, fastening, centring, reducing friction, etc.
- Context of use: Thermal or chemical stresses, vibrations and specific environments.
- Dimensional precision: Tolerances and requirements regarding the chain of dimensions, allowing for a perfect fit between the custom spacer and the surrounding parts, all while respecting the necessary tolerances.
Using this information, we will carry out a detailed analysis (via simulation software) of the mechanical stresses that the spacer will be subject to, e.g.:
- Compressive & tensile loads
- Shear force, bending & twisting
- Stresses related to vibrations and deformations.
Depending on the possible stresses identified for your made-to-measure spacer, we will advise you on the type of material you should use - steel, aluminium, stainless steel or brass.
Once the design is finalised, we will give technical recommendations to help produce the prototypes, which will in turn allow us to validate any technical choices and carry out tests on a machine bed in realistic operating conditions.
When everything has been validated, closely monitored production can begin on the custom spacers:
- Quality control at each step of the process
- Upholding necessary standards and certifications for producing made-to-order spacers
- Guaranteed high production rate for clients that need it