In machining, grinding is a finishing process that involves removing material from a part using a grinding wheel to achieve precise dimensions and shapes. This technique is essential in sectors where strict tolerances are required.
Precision grinding - plunge, centreless and through-feed grinding
Precision grinding - plunge, centreless and through-feed grinding
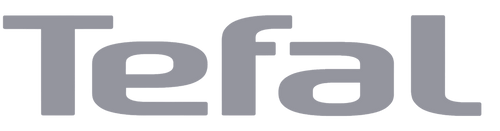
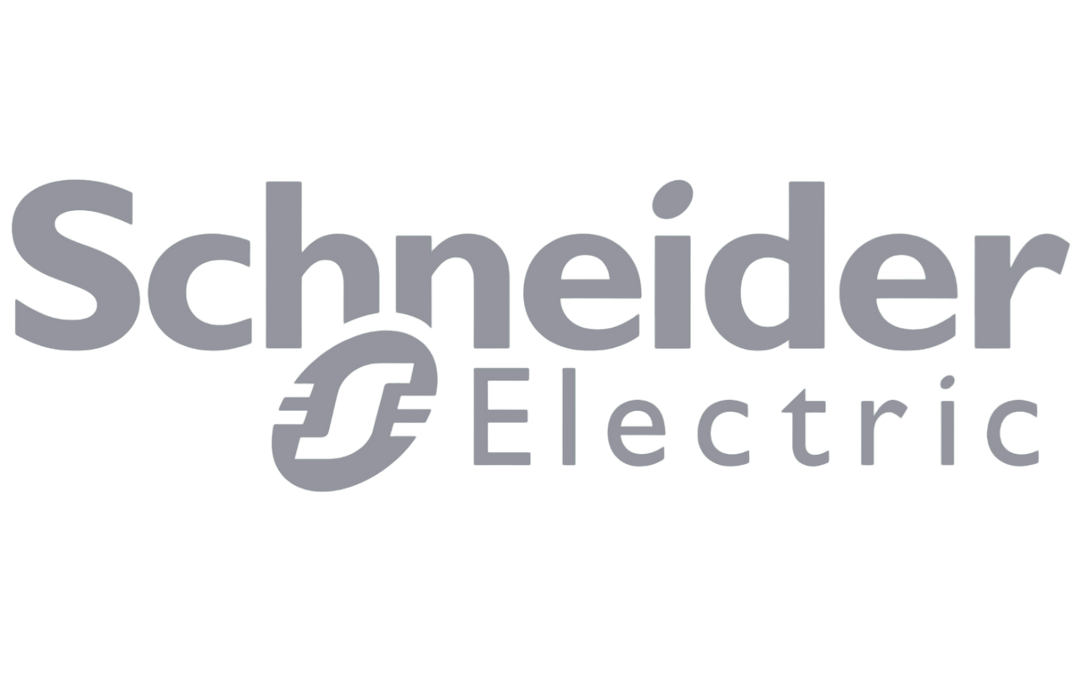
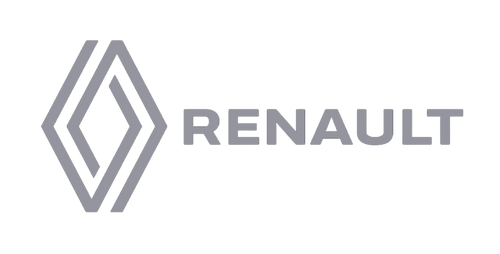
Advantages of manufacturing with LGC Industries
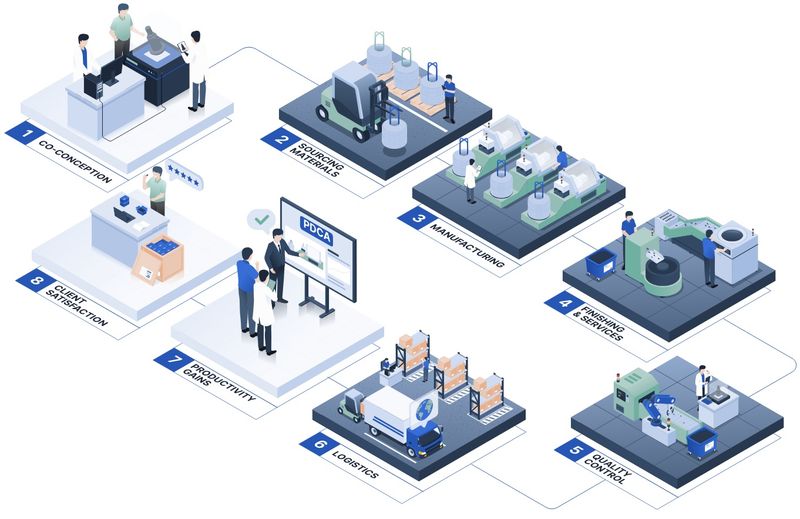
- 45 Escomatic machines
- 42 grooving machines
- 8 plunge & through-feed grinding machines






Find out more about our products' technical features
Discover other products
What does it mean to grind a part?
In precision machining, grinding is a finishing process that involves removing material from a part using a grinding wheel to reach precise dimensions and shapes. This technique is essential in sectors where strict tolerances are required.
Grinding enables us to manufacture parts with perfect dimensions and high-quality surface roughness, with minimal assembly and production errors. It is a crucial step in producing high-precision mechanical parts.
The evolution of grinding
Grinding is an ancient procedure gating back to over 4,000 years ago. Our ancestors used rudimentary millstones to grind holes into stone axes and hammers. The ancient Greeks even used millstones cooled in water or oil to increase the effectiveness of the process.
In the 15th century, Leonardo da Vinci revolutionised grinding when he invented an automated needle grinder, which was able to supply and remove needles without any human intervention. However, the first modern cylindrical grinder will only appear in 1874, introduced by Brown & Sharpe. This new machine allowed for precision as exact as 0.01mm.
This technological advancement would be a turning point in the engineering industry.
.png)
The different types of grinding
There are two main types of grinding:
- Flat grinding: Ensures a perfectly smooth & flat surface, removing material via a wheel repeatedly rolling horizontally.
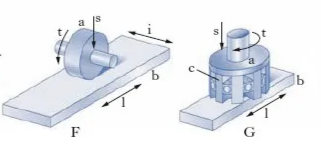
- Cylindrical grinding: Used for round or cone-shaped parts, such as shafts and pistons. The part turns while the grinding wheel moves in parallel or perpendicular to the axis.
Centreless grinding: through-feed and plunge grinding
Centreless grinding is a special grinding cylindrical technique whereby the part is not held by two tips, instead being placed on a bar which turns between two fixed wheels.
- Through-feed grinding: The part moves axially between the wheels, allowing the part to be continually machined.
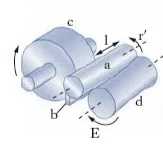
- Plunge grinding: The part stays still while the wheel comes in to remove material. Suitable for short or complex parts.
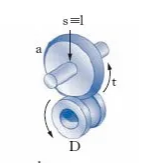
Types of wheels used in grinding
Wheels play a crucial role in the grinding process. They are made of different abrasive materials depending on the materials being machined, such as:
- Corundum: Suitable for a variety of metals and plastics.
- Diamond: Used for extremely hard materials such as ceramics and hardened steel.
- Silicon carbide: Preferable when machining hard steels.
There are several types of wheels depending on the grinding surface:
- Cylindrical wheel: For cylindrical surfaces.
- Conical wheel: For cone-shaped surfaces.
- Flat wheel: For flat surfaces.
The grinding process at LGC
At LGC, we follow a rigorous grinding process, ensuring that the final parts are in compliance with the strictest standards (DIN 6325, ISO 8734, DIN 7). The key steps are as follows:
- Preparing the raw materials:
- Cutting bars of raw material (often steel).
- Machining via CNC turning:
- Precise turning in order to reach a shape similar to that of the final part.
- Grinding:
- The part goes between the wheels to achieve tolerances right down to the micron and a perfect surface.
- Quality control:
- High-precision measuring tools (3D lab, proof machines, profile projectors) ensure that the parts are compliant.
Grinding: applications and advantages
Grinding is used in many industrial fields where maximum precision is required:
- Machine tools
- Measuring equipment
- Medical devices / instruments
The main advantages of grinding include:
- Dimensional precision: For exact positioning in assemblies.
- Increased resistance: Less wear and tear thanks to a better surface finish.
- Less noise and vibrations: Ideal for parts that move.
- Improved appearance: Shiny, smooth finish.
Grinding standards
Ground parts respect international standards, guaranteeing quality and interchangeability:
- DIN 6325 / ISO 8734: Ground cylindrical pins.
- DIN 7 / ISO 2338: Standard cylindrical pins.
These standards ensure coherence regarding the parts' dimensions, mechanical properties and reliability.
Here at LGC, we are committed to providing high-precision ground parts that live up to even the most demanding expectations from our clients.