Grooving is the name we give to this essential mechanical process for producing industrial parts. This operation involves creating parallel grooves on a part's surface, increasing the part's solidity and easing positioning and security in many mechanical assemblies.
Precision grooving - Mechanical grooves
Precision grooving - Mechanical grooves
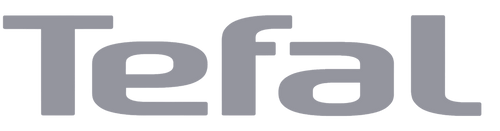
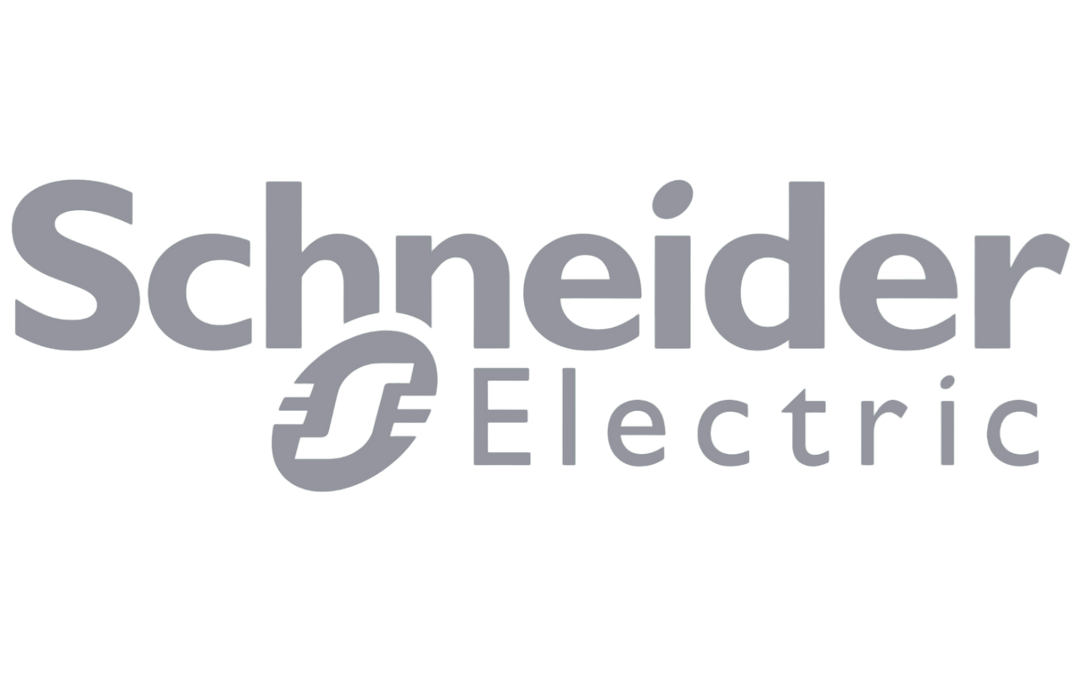
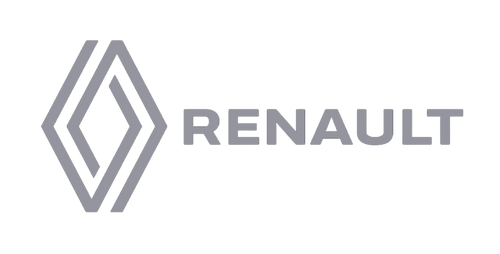
Advantages of manufacturing with LGC Industries
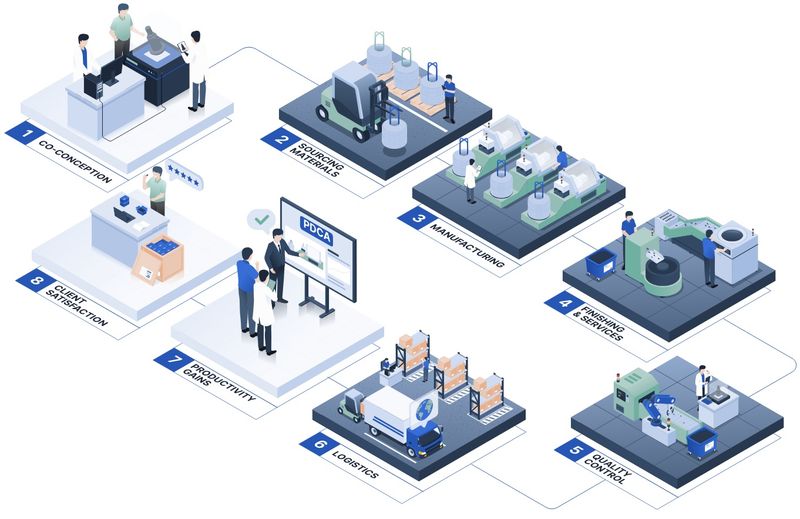
- 45 Escomatic machines
- 42 grooving machines
- 8 plunge & through-feed grinding machines






Find out more about our products' technical features
Discover other products
The grooving process: industrial precision and performance
Grooving is an essential mechanical process for manufacturing various types of industrial parts. It involves creating parallel grooves on a part's surface, increasing the part's solidity, allowing for easier positioning and more security in many mechanical assemblies.
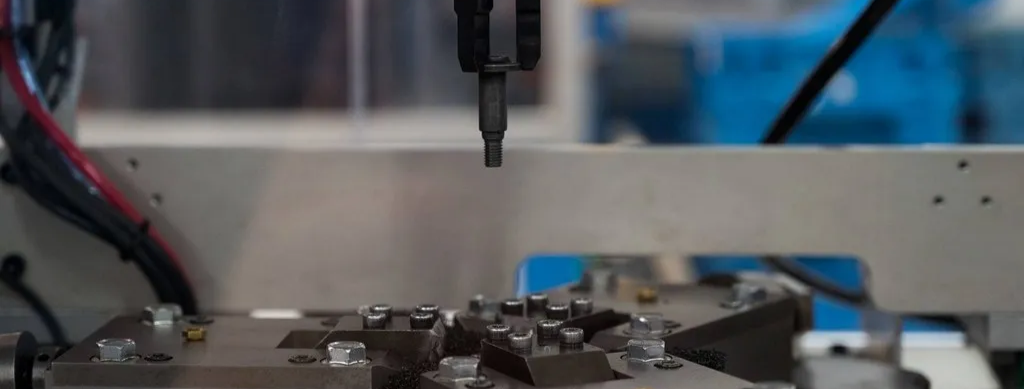
What are grooved parts?
Grooved parts are mechanical components with precise grooves on their surface. These mechanical grooves can cover the whole length of the part or be strategically positioned to meet specific assembly needs. Grooves give parts a unique ability to interlock into other components, guaranteeing solid, long-lasting fastening.
Creating grooves on a part: a high-precision operation
At LGC, grooving is carried out after the bar turning process with the help of special groove machines.
These cutting-edge machines are tailor-made to ensure the highest quality and maximum performance.
Steps in the grooving process:
- Cutting the material: A bar or wire from a coil is cut to the exact desired length. This step is crucial in order to prepare the "raw" part before moving on to the grooving phase.
- Positioning in the groove machine: The pre-cut parts are placed into one of our 30 groove machines. Each one is located right beside the lathes used for turning, meaning the parts can be treated immediately. However, our low & flat grooving machines are much larger, and are often situated away from the assembly line to deal with larger volumes or special parts.
- Forming the grooves: Under controlled pressure, our tools create constant grooves on the part's surface. This process ensures that forces are evenly distributed once the part is inserted into its housing.
- Cleaning & protection: Once the parts are out of the groove machine, they are thoroughly cleaned to remove any residue from the manufacturing process. They may also be oiled to prevent any corrosion during transport and storage.
Differences between grooving by removing material and by moving material
There are two main ways of creating grooves on a part: by material removal or by material movement.
- Grooving via material removal:
- This process involves removing material with a cutting tool (milling, broaching, etc.). This enables us to create clear and precise mechanical grooves. This type of grooves is often used in applications that require breaking-in, such as gears.
.png)
- Grooving via material movement:
- Unlike material removal, this process is based on plastic deformation of the part. Pressure simply moves the material to form grooves rather than removing it. This method is quicker, more economical and enhances the part's mechanical properties. Grooves formed by material movement are mainly used to make sure the part stays in place when inserting the grooved part into the receiving part.
.png)
Advantages of grooving for mechanical assemblies
Grooved parts are essential in the automotive, aeronautics and precision engineering sectors, among others. They ensure:
- Solidity: The mechanical parts are firmly held still thanks to precise grooves.
- Shock absorption: Reduces risk of loosening.
- Precise positioning: Simple assembly, without any need for grinding or boring.
- Security: Keeping the parts in place even when under stress.
Here at LGC, we have over 90 years' experience as grooving experts - guaranteeing high-precision grooved parts that meet even the most rigorous of standards.