- 150 million custom pins produced each year
- Co-designers of custom fasteners for 100 years
- From Ø1.5 to Ø25 and from 8 mm to 100 mm.
- Steel (free cutting, heat-treatable, carbon, alloys...), stainless steel (CNF or DNC), aluminium, brass, etc.
Custom pins are cylindrical fasteners that have undergone precision machining and bar turning. Each pin is turned to precise tolerances, ensuring the right dimensions and a perfect fit in your specific assemblies.
Custom pin - bar turning pins
Custom pin - bar turning pins
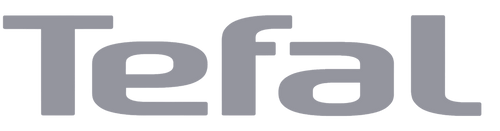
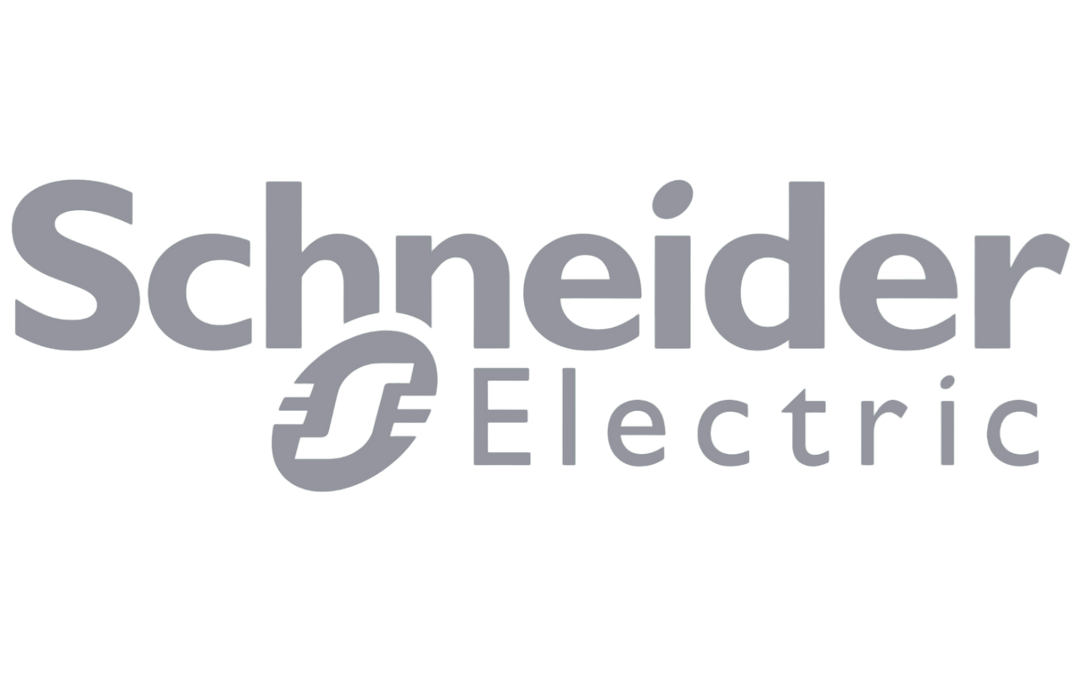
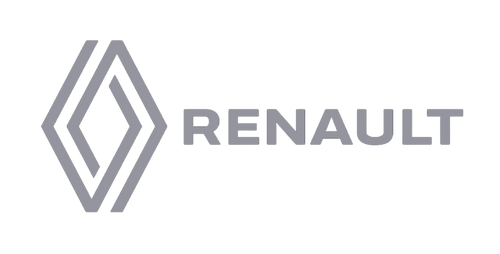
Advantages of manufacturing with LGC Industries
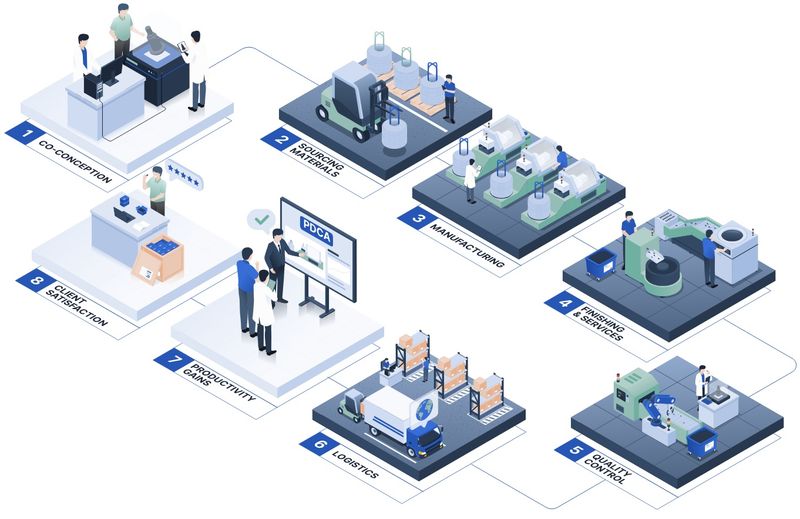
- 45 Escomatic machines
- 42 grooving machines
- 8 plunge & through-feed grinding machines






Find out more about our products' technical features
Discover other products
Custom pins are made-to-order mechanical parts that have undergone a bar turning process (an action that aims to machine a part by removing material) in order to create custom geometric characteristics (grooves, flat spots, longitudinal turning, threads, branches, milling) depending on each individual client's requirements.
Thanks to the use of CAD and CNC machining and/or conventional machining using Escomatic lathes, each custom pin is produced with precise dimensional tolerances, ensuring a perfect fit in the assembly.
This process has several names, such as micromachining, micro-turning, mechanical turning or precision bar turning. Whatever name you choose to give it, this process is part of the mechanical machining and/or precision machining family, i.e. producing small high-precision mechanical parts via turning.
Metal shafts and/or pins are used in many different sectors, from automotive and plastics to medical devices and household appliances.
Different types of pins can be used for various different applications, such as:
- Pins for fastening
- Pins for tightening
- Pins for positioning
Most of our customers use this mechanical part in metal assemblies, however the turned pin can be overmoulded (injected) into plastic. This adaptability to different materials ensures that the mechanical part is suitable for a wide range of applications, from the automotive industry to cutting-edge electronics.
How is turning used to create the part?
Machining via (bar) turning is a manufacturing technique that involves producing components by removing material. This method can be adapted to suit many different materials such as steel, titanium, aluminium, brass and stainless steel, and is used in all areas of industry: transport, household appliances, electronics, robotics, nuclear, etc.
A turned part is the result of a process called turning whereby the part is "reworked" by removing material.
LGC use this technique, which dates from the 18th century, to give parts precise geometric shapes during mass production. Turned parts come in a variety of shapes, ranging from conventional to more complex shapes.
Turning is often chosen for its speed and efficiency in batch-producing parts with strict tolerances.
The bar turning process allows the people operating the machines to combine both precision machining and repeatability.
What is a turned pin?
There are a multitude of types of pins, all of which serve different purposes, such as: grooved pins, ground pins, smooth pins and turned pins.
A pin that has undergone a specific turning process is called a cylindrical pin or turned metal shaft. This precision machining operation is carried out on a CNC lathe or a conventional lathe. The shaft/pin design is drawn up via CAD software by our design department. Eco-design is at the heart of our company's values - this is reflected, for example, in the optimisation of our machining processes, making it possible to reduce the quantity of material being removed by choosing the right raw material and tools.
This means we can adjust the shape of the turned pin to the project you have in mind.
Contact us with your requirements and we will take care of finding a solution. The turned pin offers you great flexibility when assembling your parts.
How are LGC's pins made through a specific turning process?
Several different stages go into producing made-to-measure pins through bar turning.
The first step is understanding what the client needs - the first key to the success of a project.
The second step is the prototyping phase.
LGC can provide prototypes in order to decide between several solutions put forward by the design department or to see if the final product matches the customer's requirements.
Once the solution is validated, we move on to the production stage: our process department then determines the tools best suited to cutting the material, according to the desired grade and shape.
Initial samples are produced and checked, for a quantity ranging from 100 to 50,000 units.
We assess the turned pins with our top-quality instruments and checking tools in order to be certain that the parts are fully compliant. One of the most important criteria at this stage is geometric dimensions: tolerances, surface roughness, bulge diameter; but also mechanical characteristics: hardness, chemical composition, Young's modulus, crystalline structure, crystalline structure, thickness and composition of the chemical cover. All of these criteria are evaluated and if they are found to be compliant by the quality department and the client, the manufacturing process and the entire supply chain can be validated.
That's when the product's serial life begins.
The part will be manufactured according to client's orders. Each batch is constantly monitored, allowing us to quickly detect any defects and to effectively take preventative or corrective measures.
Before shipping the turned pins, we once again subject them to compliance checks, carried out by our workers as well as high-tech machines (3D lab, proofing machine, digital profile projector). LGC is tending towards 0 PPM, a guarantee of quality for all advanced industrial sectors.
What advantages do pins offer after this specific turning process?
Custom turned pins go through a specific turning process which allows for the fixing, positioning and centring of several parts and other considerable advantages:
- Better precision: A custom turning process allows us to achieve increased dimensional accuracy for the pin, thus facilitating the assembly process and improving the fastener's precision.
- High resistance: The contact surface created by the bar turning operation between the pin and the parts increases the turned pin's shear resistance and allows for a long-lasting part.
- Reduced wear and tear: Parts are generally worn down by their components. With the turned pin, there is a reduction in friction between the pin and the parts.
- Anti-corrosion: In environments prone to corrosion, bar turning can reduce pin corrosion by over 50% by offering shapes optimised for the evacuation of fluids or the distribution of lubricant.