- 35 million dowel pins produced each year
- Co-designers of made-to-order fasteners for 100 years and manufacturer of standard products
- From M2.5 to M20 and from 6 mm to 22 mm
- Steel, stainless steel, brass, etc. (Other materials available on request).
This dowel eliminates any risk of deforming the plastic and facilitates the overmoulding or post-moulding process in any type of plastic. They serve as compression limiters in industrial sectors such as the automotive industry.
Designing and manufacturing threaded dowel pins
Designing and manufacturing threaded dowel pins
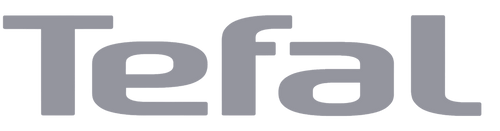
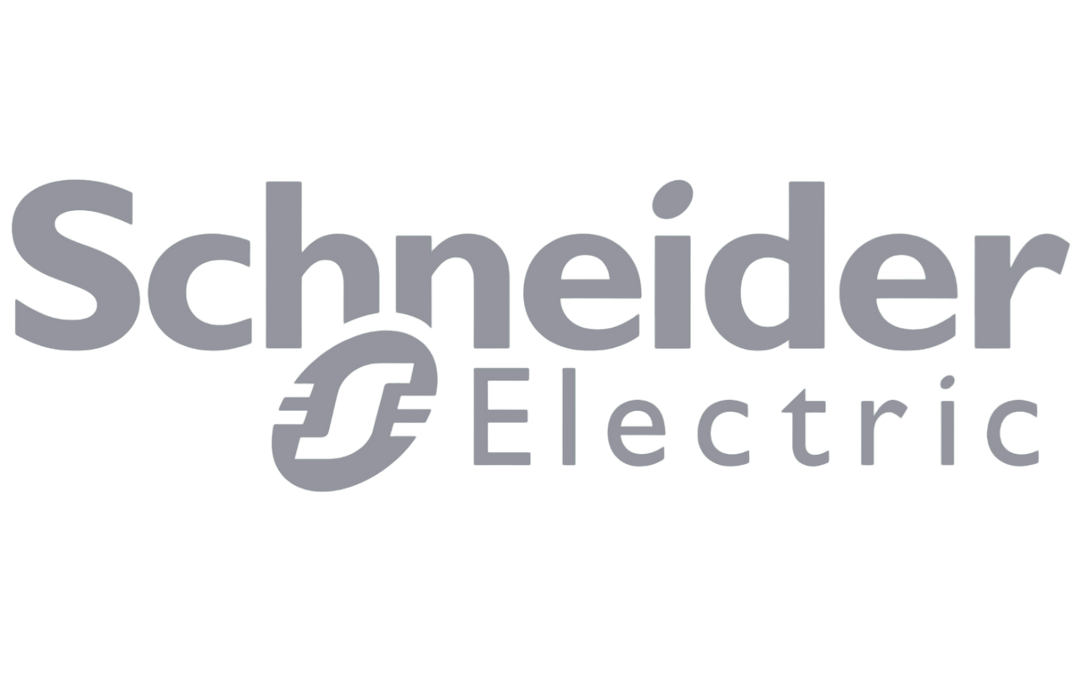
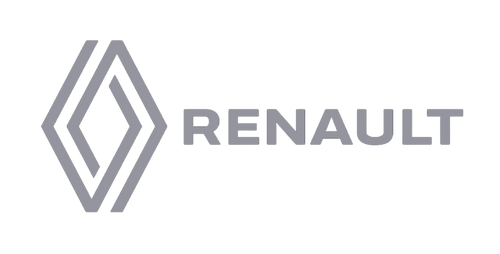
Advantages of manufacturing with LGC Industries
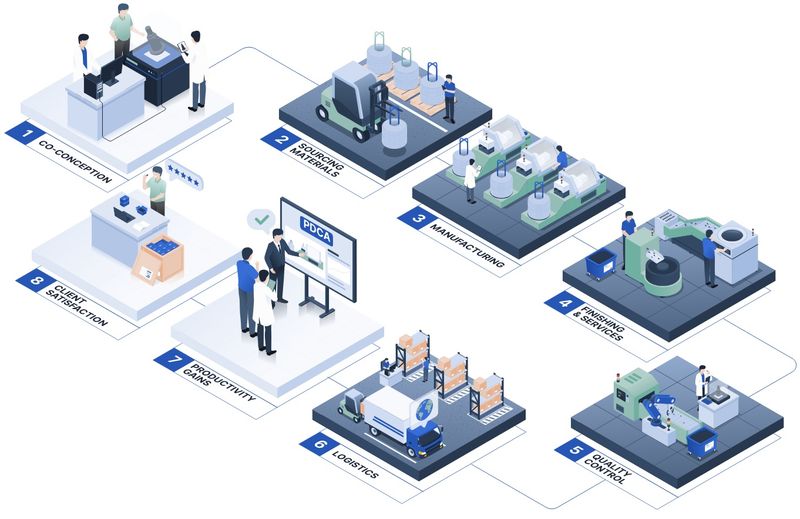
- 45 Escomatic machines
- 42 grooving machines
- 8 plunge & through-feed grinding machines






Find out more about our products' technical features
Discover other products
Threaded dowel pins: the perfect middle ground between a self-tapping threaded insert and a spacer
A threaded dowel pin or threaded spacer is a fastener with an external thread and a smooth interior, designed to be able to connect securely with other components.
Threaded dowels are essential components in the automotive industry and other industrial fields.
They are a robust and reliable fastening option thanks to their external thread, while simultaneously offering the possibility to limit compression and friction efforts with their smooth interior.
Whether it's to assemble mechanical parts, engines or suspension systems, threaded dowel pins play a key role in ensuring high-quality, long-lasting automotive assemblies.
Their detailed design and smooth operation make them essential elements for industry professionals, especially those in the automotive sector.
How are LGC threaded dowel pins made?
There are two different ways of creating a threaded dowel
From material to threaded dowel pin
The beginning of the manufacturing process for threaded dowel pins is similar to that of conventional threaded inserts.
The first step in producing threaded dowels is to thread the raw material coil on the outside.
This stage is called rolling because the dowel is put between three roller dies, with the rolling system cold working the part by compression in order to create the thread. Cold deformation increases the material's elastic strength.
This means that a rolled dowel pin / spacer will have better pull-out resistance than a laminated material.
The second step involves cutting the raw material tube in a suitable machine. The tube is then cut to the desired length.
Chamfers or surface finishing operations can be carried out on the material at this point.
It then goes through a grinding stage. A die presses the parts against a grinding wheel rotating at high speed. Thanks to abrasion from the grinding wheel, the diameter of the part is modified to reach tolerances of just a few microns (~5-6 μm).
What advantages do threaded dowel pins offer?
- Ease of assembly: Threaded dowel pins are known for being easy to assemble. Their simple design allows for quick and efficient installation, reducing the time needed to complete a project.
- Reduced friction: Thanks to their smooth internal surface, threaded dowels minimise friction within an assembly. This is particularly beneficial to avoid premature component wear and tear, and to ensure consistent performance over time.
- Precise fit: Threaded dowel pins allow for a precise fit between assembly elements. This dimensional accuracy is crucial in applications where every millimetre is important in order to maximise efficiency.
- Material versatility: Smooth dowel pins are compatible with a variety of materials, making them extremely versatile. Be it metal, plastic or composite assemblies, they can easily be adapted to different environments.
- Reduced maintenance costs: By minimising friction and providing high corrosion resistance, smooth threaded dowel pins help reduce maintenance costs. Fewer parts subject to wear and tear means a longer overall lifespan for the assembly.