- 150 million parallel pins produced each year
- Co-designers of custom fasteners and manufacturer of standard products for 100 years
- From Ø1.5 to Ø25 and from 8 mm to 100 mm
- Steel (free cutting, heat-treatable, carbon, alloys...), stainless steel (CNF or DNC) aluminium, brass, etc.
Thanks to their smooth metal shaft and the precision machining process they go through, our cylindrical pins fit perfectly into complex assemblies. Their function is simple, but essential to ensure long-lasting assemblies.
Cylindrical pin - smooth shaft
Cylindrical pin - smooth shaft
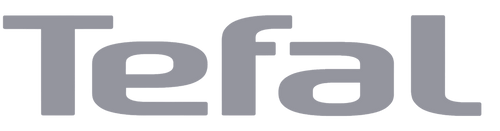
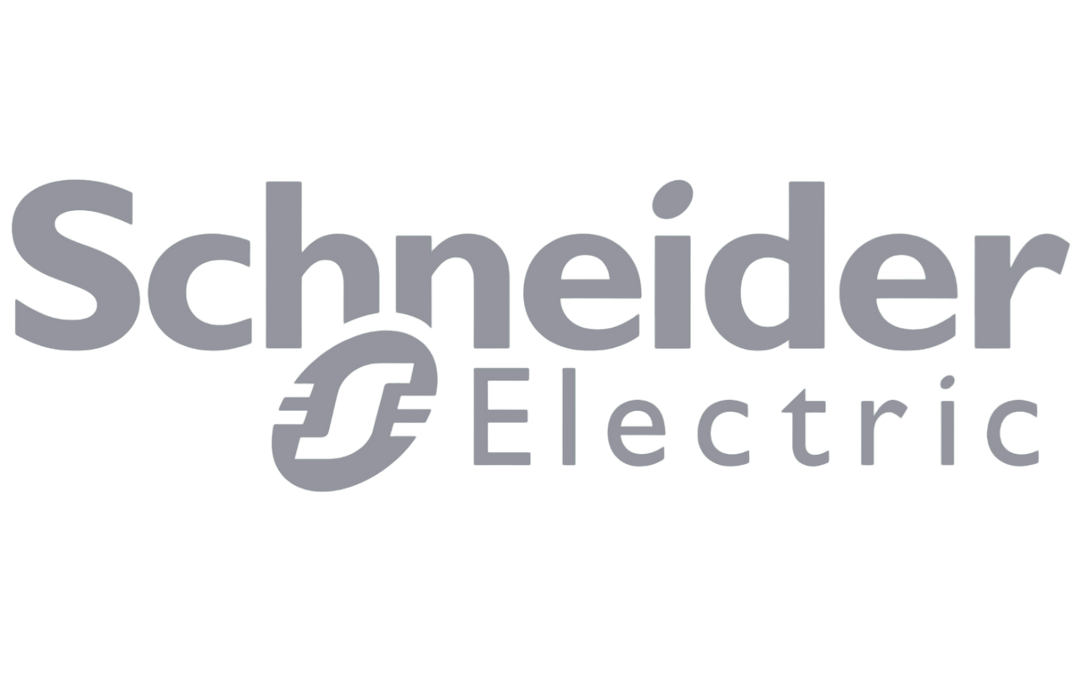
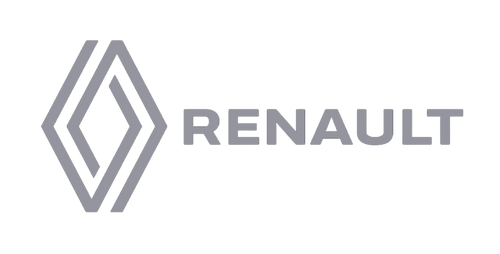
Advantages of manufacturing with LGC Industries
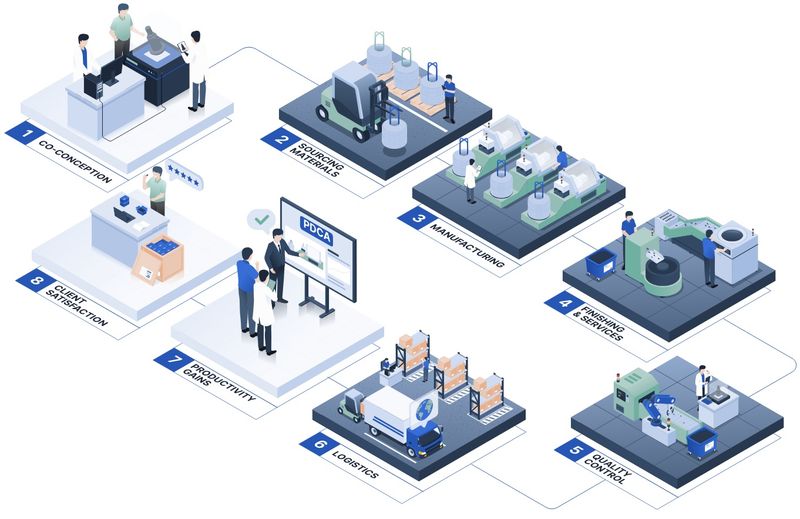
- 45 Escomatic machines
- 42 grooving machines
- 8 plunge & through-feed grinding machines






Find out more about our products' technical features
Discover other products
What is a cylinder pin?
Cylindrical pins are cylinder-shaped fasteners that look like smooth rods, without any grooves or thread. Their design allows them to be chamfered or curved depending on your specific requirements and desired application.
During the co-design process, the client can choose the material, tolerance and dimensions to best meet their own needs.
Cylindrical pins are particularly useful for quickly and reliably holding mechanical parts together. Such pins are often used in applications involving assemblies that require regular dismantling, such as industrial machines, laboratory equipment and car parts.
As the name suggests, cylindrical pins (parallel pins), do not have slots, grooves or threads on their surface. Cylindrical pins are made of steel, raw steel, stainless steel, brass, or aluminium.
Cylindrical pins come in various shapes and sizes:
- Conical cylindrical pin: Its cone-shaped tip allows for easy insertion into your assembly.
- Cylindrical pin with truncated cone: The tip of this pin makes for easy insertion while minimising the risk of slippage.
- These types of cylindrical pins have a disadvantage: they can cause the part to become dislodged.
- Smooth cylindrical pin, ISO 2338 - DIN 7: The smooth cylindrical pin is the most common form and used in many different applications. It reflects both the simplicity and effectiveness of the smooth pin.
- This is a cylindrical pin without any slots or chamfers, with dimensional tolerances predetermined by DIN 7 / ISO 2338 standards.
- Ground cylindrical pin, ISO 8734 - DIN 6325: This cylindrical pin has tighter tolerances and is used in assemblies that require the mechanical parts to be precisely aligned, in compliance with DIN 6325 and ISO 8734 standards.
What industries use cylindrical pins?
Cylindrical pins are essential assembly parts in various areas of engineering and industry. Cylindrical pins' design and their capacity to be adapted to different uses make them fundamental in many different applications, such as:
- Automotive industry: Cylindrical pins are used for fastening drive shafts and camshafts.
- Electrical: Cylindrical pins are used to fasten electrical components in their housing (small diameters).
- Aeronautics: Cylindrical pins are used to fasten various blades (e.g. inhelicopters).
How are LGC's custom cylindrical pins (ISO 2338 - DIN7) made?
The different stages of the project are the same regardless of the product, let's take the example of a cylindrical pin manufactured in compliance with ISO 2338 / DIN 7 standards:
- Understanding customer needs: Taking account of customers' needs is the first crucial step in successfully manufacturing long runs of cylindrical pins.
- Prototyping phase: LGC can provide prototypes in order to decide between several solutions put forward by the design department or to see if the final product matches the customer's requirements.
- Production: The methods office determines the tools best suited for cutting the material according to your specifications. Initial samples are produced and undergo rigorous quality checks to guarantee compliance with geometric and mechanical standards.
- Serial life: Manufacturing of the cylindrical pins begins, if the client so wishes, with continuous quality assessments to quickly detect any defects and take corrective measures where necessary.
- Final checks: Before being shipped out, our cylinder pins undergo a final series of conformity checks carried out by LGC employees and high-tech machines, ensuring an optimal level of quality, with a target of 0 PPM - just like in the most demanding industrial sectors.
Used to form the part's shape, the turning and finishing processes are what makes cylindrical pins different from other products.
What advantages do cylindrical pins offer?
Cylindrical pins are the pin of choice in many industrial and engineering environments, thanks to their distinctive properties and advantages.
Here's our detailed analysis of the main benefits of using cylindrical pins:
- Ease of use: Cylinder pins are extremely simple to install, simplifying the assembly process. This can save a significant amount of time when assembling the different components.
- Reliable assembly: Cylindrical pins allow parts to be put solidly together, thus guaranteeing the stability and durability of the assembled structures or mechanisms. This sturdy connection helps prevent any unwanted movement between the components in the assembly.
- High mechanical resistance: Designed to withstand significant loads, cylindrical pins excel in applications requiring high mechanical resistance. This ability to withstand high stresses makes them an essential asset in many rigorous industrial environments.
- Application versatility: Cylindrical pins lend themselves to a multitude of different applications, from mechanical assembly in the manufacturing industry to sectors as diverse as the automotive and aerospace industries. Their ability to adapt to different environments and requirements makes them a versatile choice, one of the reasons they are so widely used in modern industry.
In short, cylindrical pins stand out for their ease of use, reliable assembly, high mechanical resistance and versatility of applications, making them an essential component in many industrial and engineering applications.
With the right heat treatments and surface finishes, cylindrical pins can offer increased wear resistance and better adhesion in assemblies.