La rectification est un processus d'usinage de finition qui consiste à retirer de la matière d'une pièce à l'aide d'une meule abrasive afin d'obtenir des dimensions et une forme précises. Cette technique est essentielle dans les secteurs où des tolérances strictes sont requises.
Rectification de précision : En plongée, centerless et enfilade
Rectification de précision : En plongée, centerless et enfilade
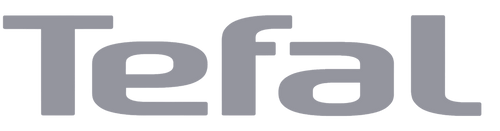
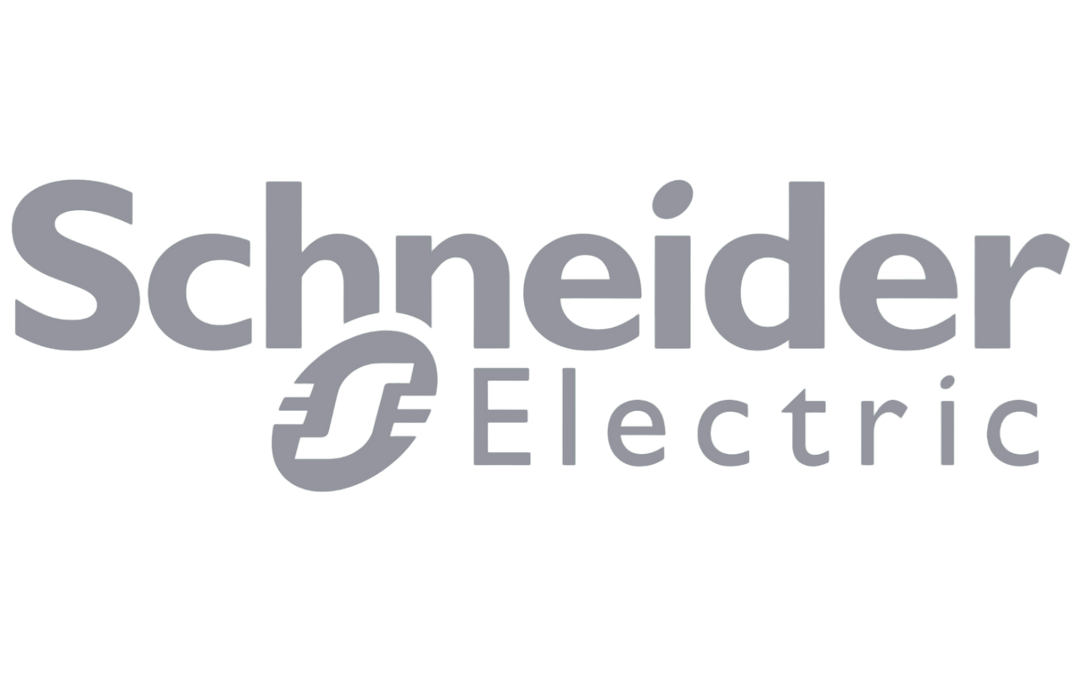
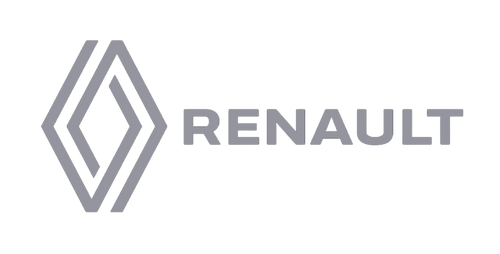
Les atouts d'une fabrication LGC Industries
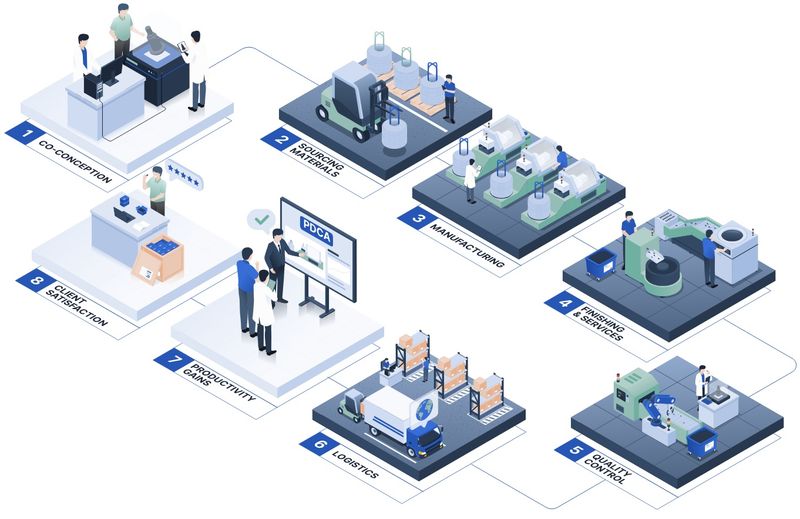
- 45 Tours Escomatic
- 42 Canneleuses
- 8 Rectifieuses plongée et enfilade






Apprenez-en davantage sur les caractéristiques techniques de nos produits
Découvrez d'autres produits
Qu'est-ce que la rectification de pièces ?
La rectification est un processus d'usinage de finition qui consiste à retirer de la matière d'une pièce à l'aide d'une meule abrasive afin d'obtenir des dimensions et une forme précises. Cette technique est essentielle dans les secteurs où des tolérances strictes sont requises.
La rectification permet de garantir des pièces aux dimensions parfaites, avec des états de surface de haute qualité, minimisant ainsi les erreurs d'assemblage ou les défauts de fabrication. C'est une étape cruciale dans la fabrication de composants mécaniques de haute précision.
L'évolution de la rectification
La rectification est un procédé ancien dont les origines remontent à plus de 4 000 ans. Nos ancêtres utilisaient des meules rudimentaires pour rectifier des trous dans des haches ou des marteaux en pierre. Dès l'Antiquité grecque, des meules refroidies à l'eau ou à l'huile étaient déjà employées pour améliorer l'efficacité du processus.
Au XVe siècle, Léonard de Vinci révolutionna le domaine en inventant une rectifieuse d'aiguilles automatisée, capable d'approvisionner et de retirer les aiguilles à rectifier sans intervention humaine. Toutefois, c'est en 1874 que la première rectifieuse cylindrique moderne fut introduite par Brown & Sharpe, permettant d'atteindre des précisions de l'ordre de 0,01 mm.
Cette avancée marqua un tournant décisif pour l'industrie mécanique.
.png)
Les différents types de rectification
On distingue principalement deux types de rectification :
- Rectification plane : Assure une surface parfaitement lisse et plane en retirant la matière à l'aide de passages successifs de la meule sur un plan horizontal.
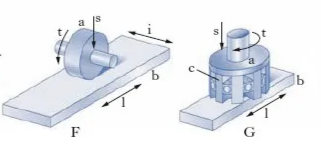
- Rectification cylindrique : Destinée aux pièces rondes ou coniques, comme les axes ou les pistons. La pièce tourne tandis que la meule se déplace parallèlement ou perpendiculairement à l'axe.
La rectification centerless : enfilade et plongée
La rectification sans centre (centerless) est une technique spécifique de rectification cylindrique dans laquelle la pièce n'est pas tenue entre pointes, mais repose sur une réglette et tourne entre deux meules fixes.
- Enfilade : La pièce se déplace axialement entre les meules, permettant un usinage continu.
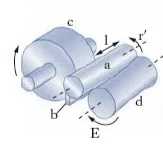
- Plongée : La pièce reste immobile tandis que la meule s'avance pour retirer la matière, adapté aux pièces courtes ou de formes complexes.
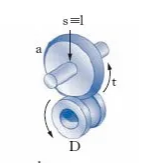
Les types de meules utilisées en rectification
Les meules jouent un rôle central dans le processus de rectification. Elles sont composées de matières abrasives différentes en fonction des matériaux à usiner :
- Corindon : Adapté à une variété de matériaux, y compris les plastiques.
- Diamant : Utilisé pour les matériaux extrêmement durs comme les céramiques ou les aciers trempés.
- Carbure de silicium : Privilégié pour l'usinage des aciers durs.
Les meules se déclinent en plusieurs formes selon les besoins de rectification :
- Meule cylindrique : Pour les surfaces cylindriques.
- Meule conique : Pour les surfaces coniques.
- Meule plate : Pour les surfaces planes.
Le processus de rectification chez LGC
Chez LGC, nous suivons un processus rigoureux de rectification afin de garantir des pièces conformes aux normes les plus strictes (DIN 6325, ISO 8734, DIN 7). Voici les étapes clés :
- Préparation des matières premières :
- Découpe des barres de matières brutes (souvent de l'acier).
- Usinage par décolletage CNC :
- Tournage précis pour obtenir une forme approchante de la pièce finale.
- Rectification finale :
- La pièce passe entre les meules pour atteindre des tolérances de l'ordre du micron et une surface parfaite.
- Contrôle qualité :
- Des outils de mesure de haute précision (laboratoire tridimensionnel, machines de contrôle 100%, projecteurs de profil) garantissent la conformité des pièces.
Applications et avantages de la rectification
La rectification est utilisée dans de nombreux domaines industriels exigeant une précision maximale :
- Machines-outils
- Équipements de mesure
- Instruments médicaux
Les principaux avantages du processus de rectification incluent :
- Précision dimensionnelle : Permet un positionnement exact dans les assemblages.
- Résistance accrue : Réduction de l'usure grâce à une meilleure finition de surface.
- Réduction du bruit et des vibrations : Idéal pour les pièces en mouvement.
- Esthétique améliorée : Finition brillante et lisse.
Les normes de rectification
Les pièces rectifiées respectent des normes internationales garantissant leur qualité et leur interchangeabilité :
- DIN 6325 / ISO 8734 : Goupilles cylindriques rectifiées.
- DIN 7 / ISO 2338 : Goupilles cylindriques standards.
Ces normes assurent une cohérence dans les dimensions, les propriétés mécaniques et la fiabilité des pièces produites.
Chez LGC, nous nous engageons à fournir des pièces rectifiées de haute précision, répondant aux attentes les plus exigeantes de nos clients.