Assemblage pour système de freinage électrique
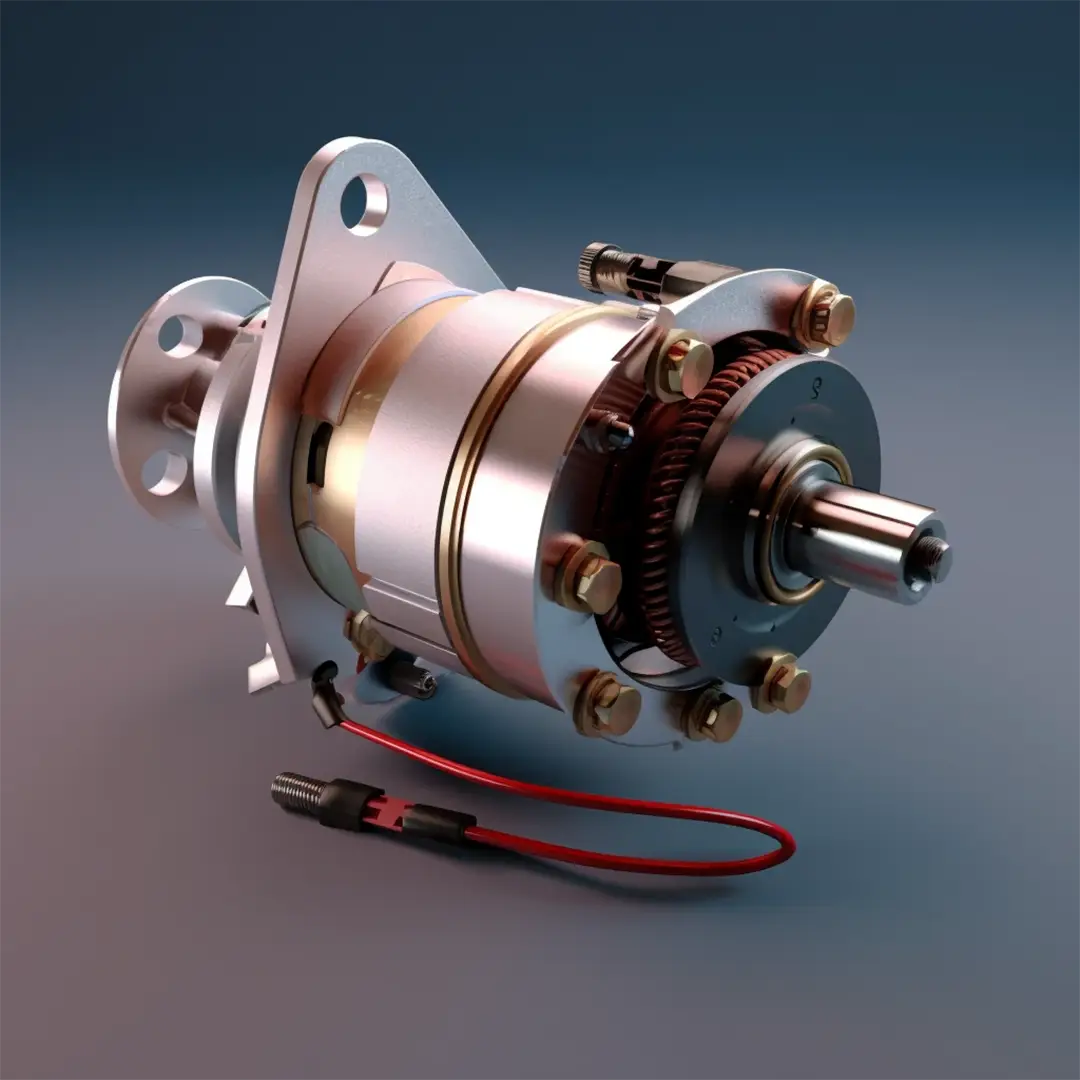
Quel est le contexte et l'application du client ?
Notre client est un équipementier international de rang 1. En 2017, il a entrepris un projet visant à développer une assistance au freinage pour véhicule électrique. Il a eu de nombreux challenges à relever comme la propreté, l’électronique embarqué ainsi que la réalisation d’une boite à vitesse accouplé à un moteur électrique.
Pour la fixation d’un couple roulement et engrenage sur une vis spéciale avec tête notre client nous a consultés en tant qu’expert. LGC ayant déjà participé au développement de plusieurs projets d’innovation, notre client nous a challengés.
Quel était le projet de fixation du client avant de venir nous voir ?
Initialement, le client est venu nous voir pour la conception d’une vis M8 à tête avec un corps de diamètre 12 devant recevoir un roulement nécessitant une précision de XX microns ainsi qu’une surface de dureté XX, une cylindricité de XX et une rugosité de XX.
En version monobloc nous pouvions partir d’un lopin de diamètre 22 puis par décolletage réaliser une ébauche du chemin de roulement de diamètre 12 avant un traitement par induction. En opération finale nous réalisions une rectification en plongée.
Le prix de revient d’un composant produit par de multiples process en faisait une pièce très complexe et peu efficace.
Quelle étude nous avons menée ?
La solution par goupille cannelée était demandée par le client. Aucune autre solution n’a été proposée car pas de meilleure proposition.
Pour cette pièce, nous étions convaincus de l'inefficacité du procédé existant et nous en avons imaginé un tout nouveau ! Le travail s'est porté autour d'un assemblage plutôt qu'un décolletage avec moins d'enlèvements de matière, plus d'automatisation et une réduction drastique des coûts.
Quelle préconisation nous avons faite ?
Nous avons proposé à notre client une version bi corps composé d'un axe à tête et d'une entretoise qui vient s'emmancher sur l'axe par un assemblage automatisé.
- L'axe à tête en M8 réalisé en frappe à froid sur lequel nous venons réaliser un cannelage de précision. La frappe à froid a l'avantage de soutenir des cadences extrêmement compétitives.
- L'entretoise emmanchée, qui après traitement thermique en lot sera rectifiée pour l’obtention de la précision sur le diamètre ainsi que la rugosité.
- Un assemblage automatisé de l’entretoise sur le cannelage de l’axe M8 permettant de conserver les précisions requises (cylindricité de XX microns, rugosité xxx ) pour le roulement grâce à la maîtrise du cannelage en grande série. Lors de l’assemblage des opérations de contrôle sont effectuées : présence et position de l’entretoise, effort mini et maxi de tenue de l’entretoise sur l’axe cannelé
- La mise en conditionnement est assurée par un robot, cet îlot d’assemblage est conduit par un opérateur
Quel bénéfice chiffrable pour notre client ?
Le bénéfice mesuré est d'abord sur le coût de la pièce avec une amélioration des coûts de 40 % au pic de production
L’empreinte carbone est réduite de plus de 50 % car aucune opération de décolletage n'est réalisée ce qui entraîne une réduction de l'énergie utilisée pour produire et de la matière sacrifiée considérable.
Des investissements réduits accompagnant le développement du projet depuis 2017 car nous nous sommes appuyés sur des techniques maîtrisées en interne avec le cannelage qui est notre spécialité, la fabrication d'une entretoise de production semi-standard et un axe M8 obtenu en frappe à froid sur machine standard en 5 postes.