- 35 million dowel pins produced each year
- Co-designers of custom fasteners for 100 years and manufacturer of standard products
- From M6 to M10 and from 8 mm to 30 mm (internal diameter adapted to fit a screw)
- Steel, stainless steel, brass, etc. (Other materials available on request).
A dowel pin designed for precise centring and alignment of assembly components. Frequently used for centring two half-cases (transmission belt housing, centre bearing, gearbox housing, etc.).
Manufacturing centring and positioning dowel pins
Manufacturing centring and positioning dowel pins
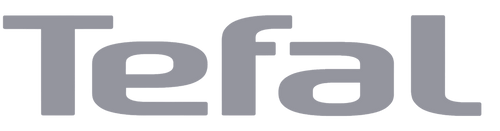
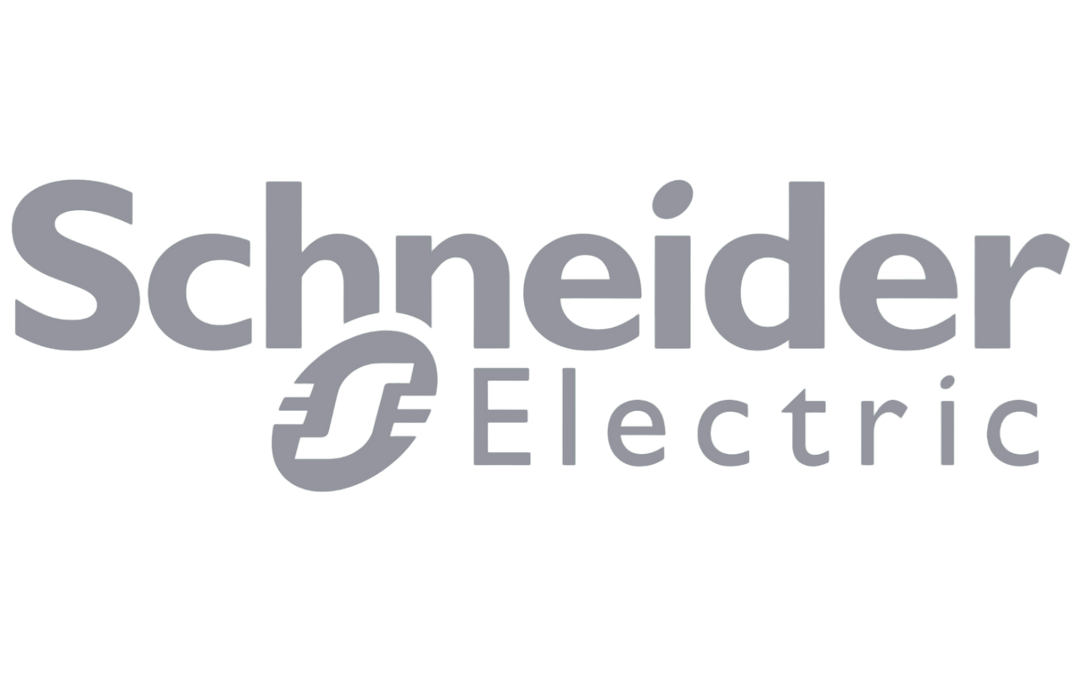
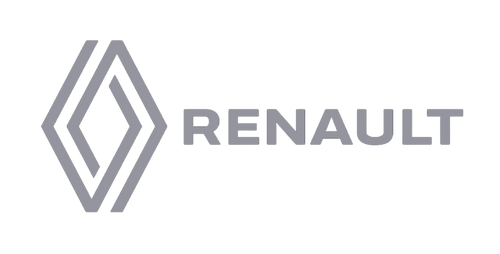
Advantages of manufacturing with LGC Industries
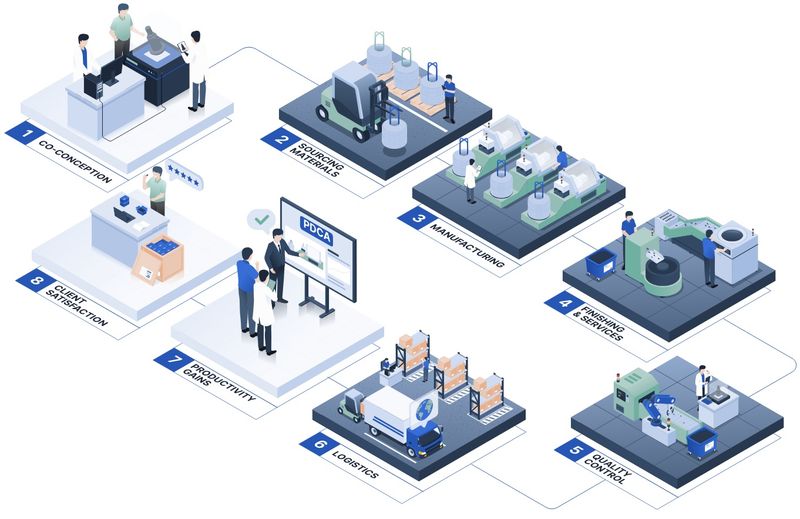
- 45 Escomatic machines
- 42 grooving machines
- 8 plunge & through-feed grinding machines






Find out more about our products' technical features
Discover other products
Optimise your assemblies with a ground dowel pin
Ground dowel pins, often called ”positioning pins" or "centring pins” play an essential role in mechanics and industrial assemblies. They guarantee precise positioning of the components, reducing the risk of deforming the parts or uncontrolled movement. These small positioning elements are often overlooked, which may explain - in some cases - the decline in the overall performance of a mechanism.
Ground dowel pins aka centring pins are the crown jewel of any assembly. Ground dowel pins ensure perfect alignment of the parts, eliminating gaps and undesirable friction. Frequently used in complex mechanical systems, this small cylindrical part will help you reach another level of precision in your assemblies.
What are centring pins?
Ground dowel pins (aka bushes / bushings / sleeves) are extremely precise cylindrical assembly elements designed specifically to ensure the precise centring and positioning of two components in an assembly.
Their innovative design eliminates any risk of entanglement, essential for automated assemblies. Thanks to our specialised production facilities, we guarantee a level of quality close to zero defects, 0 PPM.
Unlike other types of pins, ground dowels can accommodate through bolts, offering greater flexibility in applications.
How do we manufacture our ground dowel pins at LGC?
There are two different ways of producing dowel pins:
From pin to ground dowel pin
It is possible to start from a solid material that has been machined until it finally reaches the form of a pin. In this case, a hole must be drilled in the pin to make it hollow. This is called a bore, and it complicates the process not just financially and technically, but also environmentally.
From tube to ground dowel pin
Otherwise, a positioning dowel pin can be made from a tube.
The use of a tube is highly recommended because it perfectly meets all criteria (precision, price, quality and also carbon footprint).
This is the technique we use here at LGC.
The first step in manufacturing a dowel pin is cutting the raw material, which comes in the form of long, hollow tubes. The material and the diameter depend on the desired final part.
The tube enters a machine which cuts it to the desired length.
The part can be further machined using specialised machines.
For example, chamfers may be required, or surface finishes may be applied to your spacers.
The dowel then goes through a grinding process.
A die presses the parts against a grinding wheel rotating at high speed. Through abrasion, this wheel modifies the diameter of the part to reach tolerances of several microns (~5-6 μm).
What advantages do ground centring pins offer?
- Dimensional accuracy: Centring dowel pins allow for impeccable dimensional accuracy. By creating an identical space between the different components, the ground dowel eliminates potential errors linked to differences in dimensions or alignments between two parts.
- Structural stability: This sturdy centring pin offers exceptional structural stability. It is resistant to vibrations and mechanical loads, ensuring optimal performance even under the most rigorous conditions. This is why it can be found in almost all our vehicles' engines.
- Reduced friction: Thanks to its intelligent design and the grinding process, the centring dowel pin reduces friction between moving parts. This results in reduced wear and tear as well as a longer component lifespan.