Baugruppe für elektrisches Bremssystem
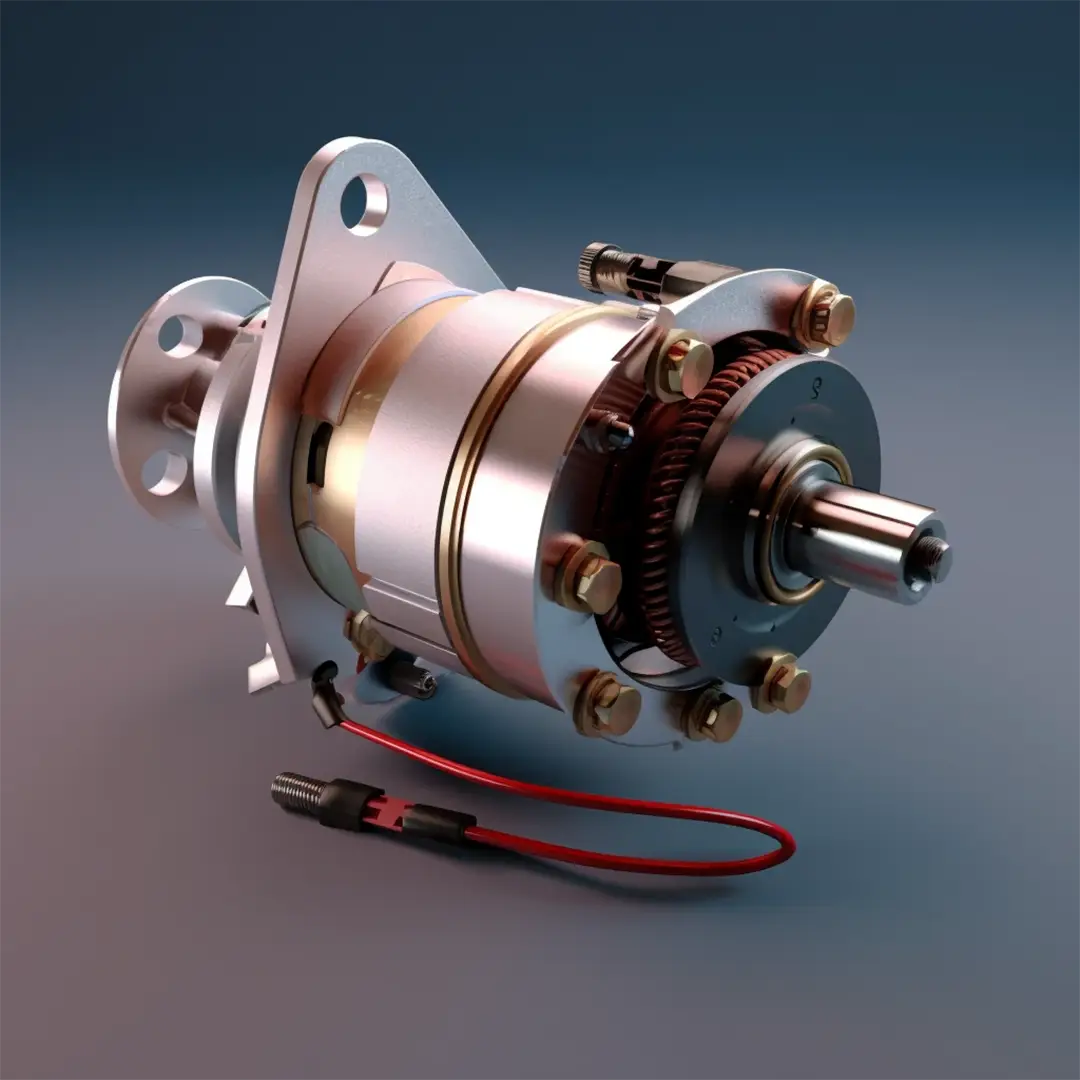
Was ist der Kontext und die Anwendung des Kunden?
Unser Kunde ist ein internationaler Tier-1-Gerätehersteller. Im Jahr 2017 führte er ein Projekt zur Entwicklung von Bremsassistenten für Elektrofahrzeuge durch. Er hatte viele Herausforderungen zu bewältigen, wie zum Beispiel Sauberkeit, eingebettete Elektronik sowie die Entwicklung eines Getriebes, das an einen Elektromotor gekoppelt war.
Um ein Lager- und Zahnradpaar an einer Spezialschraube mit Kopf zu befestigen, konsultierte uns unser Kunde als Experten. Nachdem LGC bereits an der Entwicklung mehrerer Innovationsprojekte beteiligt war, forderte uns unser Kunde heraus.
Was war das Befestigungsprojekt des Kunden, bevor er zu uns kam?
Zunächst kam der Kunde zu uns für die Gestaltung eine M8-Schraube mit einem Kopf mit einem Durchmesser von 12, der ein Lager aufnehmen muss, das eine Präzision von XX Mikron sowie eine Oberfläche mit der Härte XX, einer Zylindrizität von XX und einer Rauheit von XX erfordert.
In der Monoblock-Version könnten wir mit einem Stück mit einem Durchmesser von 22 Zoll beginnen und dann vor der Induktionsbehandlung durch Drehen einen groben Umriss der Laufbahn mit einem Durchmesser von 12 Zoll erstellen. In der letzten Operation führten wir eine Tauchkorrektur durch.
Der Selbstkostenpreis einer Komponente, die in mehreren Verfahren hergestellt wurde, machte sie zu einem sehr komplexen und ineffizienten Teil.
Welche Studie haben wir durchgeführt?
Die Lösung von geriffelter Stift wurde vom Kunden angefordert. Es wurde keine andere Lösung vorgeschlagen, da es einen besseren Vorschlag gab.
Für dieses Stück waren wir von der Ineffizienz des bestehenden Prozesses überzeugt und haben uns einen völlig neuen vorgestellt! Die Arbeit konzentrierte sich eher auf eine Montage als auf Dekollettieren mit weniger Materialabträgen, mehr Automatisierung und einer drastischen Kostensenkung.
Welche Empfehlung haben wir ausgesprochen?
Wir boten unserem Kunden eine Bibody-Version an, bestehend aus einer Kopfwelle und einem Strebe das durch automatische Montage auf der Welle befestigt wird.
- Die Achse mit einem in Kaltkopf gefertigten M8-Kopf, auf der wir gerade eine Flöten von Präzision. Die Kaltumformung hat den Vorteil, dass sie äußerst wettbewerbsfähige Preise ermöglicht.
- Der ummantelte Abstandhalter, der nach der Chargenwärmebehandlung geschliffen wird, um sowohl den Durchmesser als auch die Rauheit genau zu bestimmen.
- Eine automatische Montage des Abstandhalters auf der Keilverzahnung der M8-Achse ermöglicht es, dank der Steuerung der Keilverzahnung in großen Serien die erforderliche Präzision (Zylindrizität von XX Mikron, Rauheit xxx) für das Lager beizubehalten. Bei der Montage werden folgende Kontrollen durchgeführt: Vorhandensein und Position des Abstandshalters, minimale und maximale Haltekraft des Abstandshalters auf der Keilwelle
- Die Verpackung erfolgt durch einen Roboter, diese Montageinsel wird von einem Bediener angetrieben
Was sind die quantifizierbaren Vorteile für unsere Kunden?
Der gemessene Vorteil ergibt sich in erster Linie aus den Kosten des Bauteils, wobei bei Spitzenproduktion eine Kostenverbesserung von 40% zu verzeichnen ist.
Der CO2-Fußabdruck wird um mehr als 50% reduziert, da kein Gewindeschneiden durchgeführt wird, was zu einer erheblichen Reduzierung des für die Herstellung verwendeten Energieverbrauchs und des Materialopfers führt.
Die Entwicklung des Projekts wurde seit 2017 durch geringere Investitionen begleitet, da wir uns auf Techniken verlassen haben, die wir intern mit der Riffelung beherrschen. Unsere Spezialität ist die Herstellung eines halbstandardisierten Produktionsabstandhalters und einer M8-Achse, die durch Kaltumformung auf einer Standardmaschine in 5 Stationen hergestellt werden.