Oxygen regulator valve
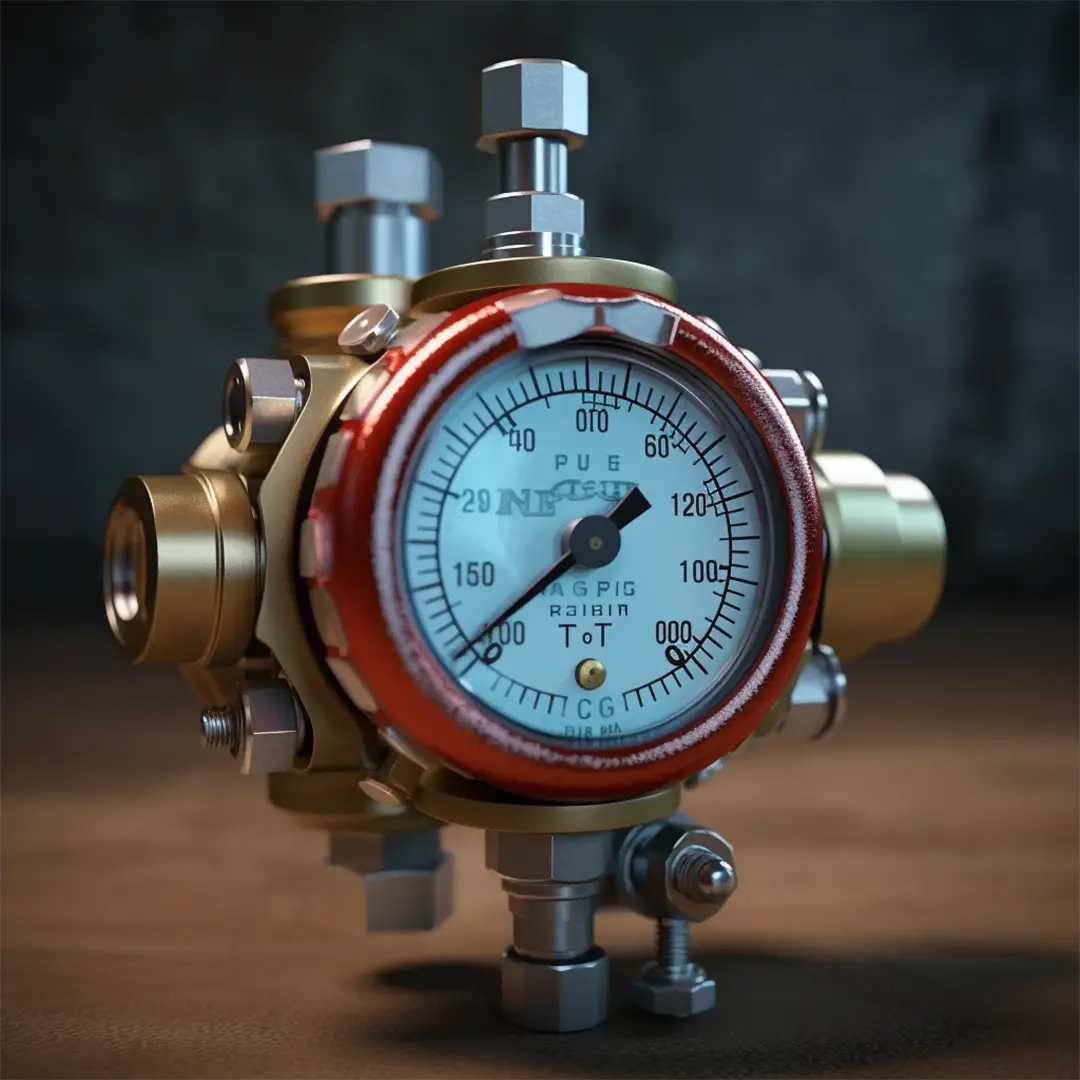
What was the context and the client's desired application?
Oxygen regulator valves are placed on oxygen cylinders in order to reduce and monitor pressure. In our case, this was for a medical application. The product's workings should therefore not be questioned or modified under any circumstances, as this could compromise the safety and lives of its users.
What fasteners did the client have in mind before contacting us?
A two-part set is held together by a pin system. At the beginning of the project, the pins used were ground pins (ISO8734). However, the dispersion in the assembly forces was too great, with a risk of pins moving in the event of low values. The construction needed to be able to withstand strong pressure to avoid any risk of an accident. This risk becomes very high once a pin is missing. The supplier of the part on which the pins were being placed told the client to try using grooved pins.
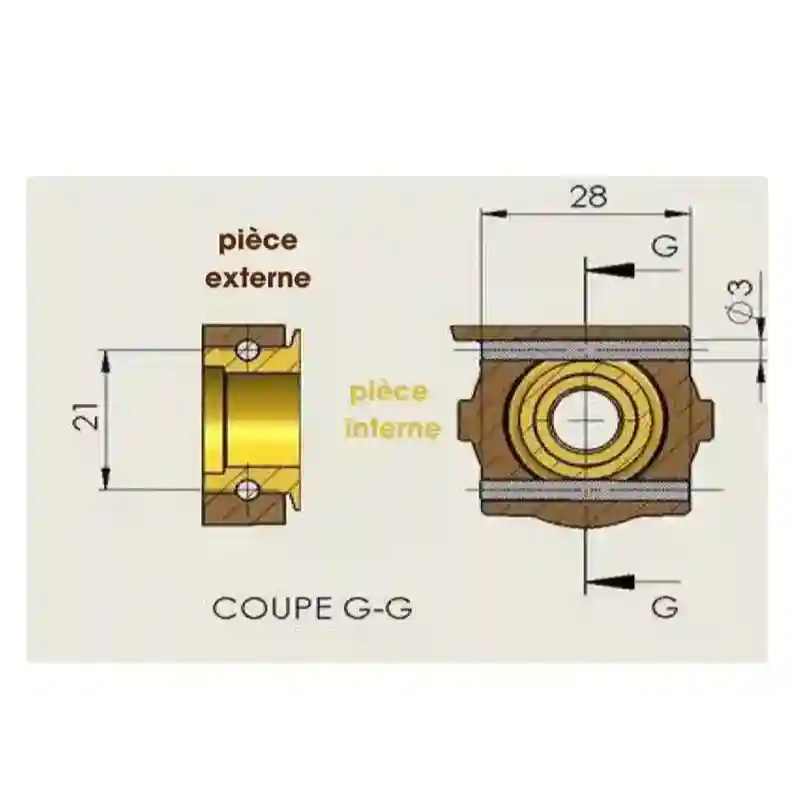
What studies did we conduct?
We carried out an analysis to determine if the original solution was a problem. A dimensional chain was created in order to check compatibility between the parts' dimensions of the parts and the desired function. Upon analysis, we realised that the material could never be tight enough, regardless of the grinding. Subsequently, our design office came up with a grooved support to reduce insertion efforts and prevent the parts from moving. Automated assembly by the client put the assembly at risk due to excessive assembly force being applied - but a reduction in such force offered a solution:
- A grooved pin requires 500 to 1000kg of assembly force.
- A ground pin requires 1000 to 1500kg of assembly force.
What was our advice to the client?
We presented our client with a design review to best advise them on their fastening challenges and requirements. This design review contained:
- A grooved pin design tailored to their needs
- A symmetrical pin with grooves on both ends. This helps with working the part on an assembly line (40% less scrap during assembly);
- ISO 8734 mechanical specifications, e.g. in terms of hardness so that the pin lasts over time.
- A recommendation on the drilling diameter: dimensional chain that determines the characteristics of the housing so that the pin fulfils its solidifying function in 100% of cases before marketing authorisation. This was the customer's biggest concern
- Adaptation to various assembly variables with:
- Maximum force amount when inserting;
- Hardness of the part;
- Cleanliness level, certifying the absence of hydrocarbons.
What were the quantifiable benefits for our client?
For our client, this LGC co-design resulted in:
- 1 less machining step in the design of this technical solution;
- 20% less swarf thanks to the elimination of grinding, improving production costs and carbon footprint;
- 100% less waste than client's original fastening solution;
- 100% market authorisation with over 100,000 units produced each year since 2017, i.e. 600,000 regulator valves sold.