Overmoulded pins in a planetary gearset
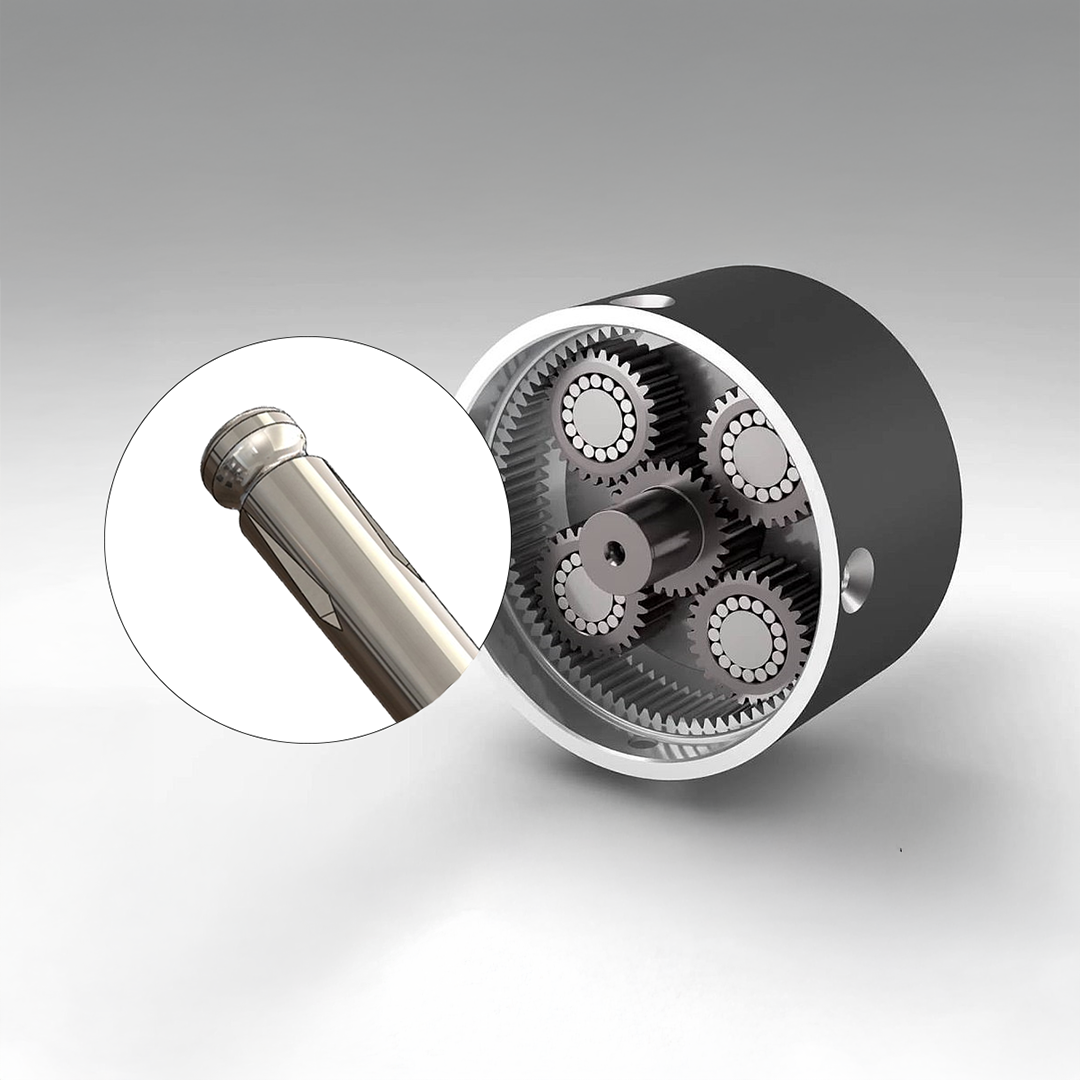
What was the context and the client's application?
The customer, a well-known automotive company, needed a reliable solution for their cooling system. The system includes a motorised valve to regulate cooling flows and manage the vehicle's temperature.
The mechanism in question was a planetary gearset or gearbox controlled by a computer that activated a valve to direct the coolant in different directions. This system's most critical components are made of metal (e.g. the planetary carriers), which are overmoulded into a plastic part (the drive shaft).
The customer encountered a major problem regarding pull-out resistance. They first decided to use a knurled pin, but it was not sufficient to ensure the safety and reliability of the system.

What fasteners was the client using before talking to us?
The client's initial fastening solution was a Ø1.5 diameter pin knurled to 1/4 of its length.
The assembly process involved overmoulding the pins when inserting the main shaft.
However, this proved to be a poor solution in terms of mechanical strength, especially when put against pull-out and torque forces, which are critical in any coolant control system.
Principle of overmoulding:
.png)
What studies did we conduct?
In our Protolab, we conducted a series of tests on the pull-out resistance of the knurled pins that our client had been using.
The results confirmed that this solution did not meet the technical requirements laid out in the specifications, i.e. 100 Newtons. We needed to find a more efficient alternative to ensure the safety and durability of the system.
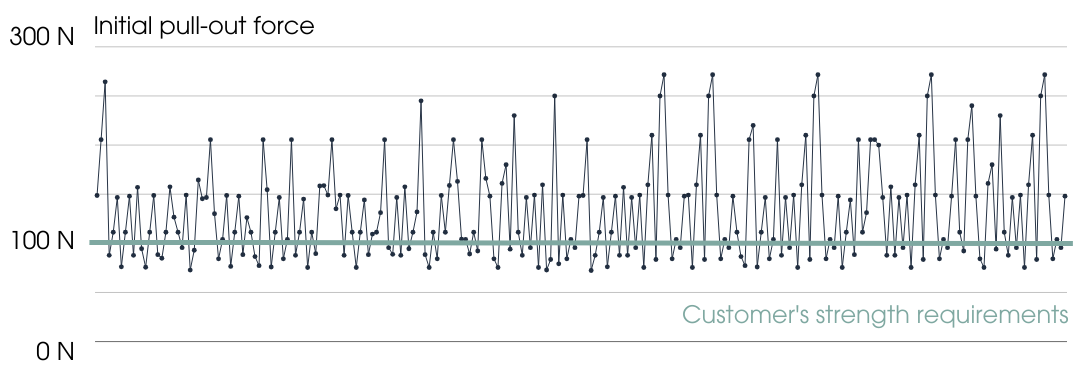
What was our advice to the client?
Upon analysis, we suggested a grooved pin with a custom indentation.
This new solution offered several advantages:
- The grooves allowed the overmoulded plastic to fit perfectly, removing any looseness.
- The custom indentation blocked translational movements, guaranteeing flawless fastening in all directions.
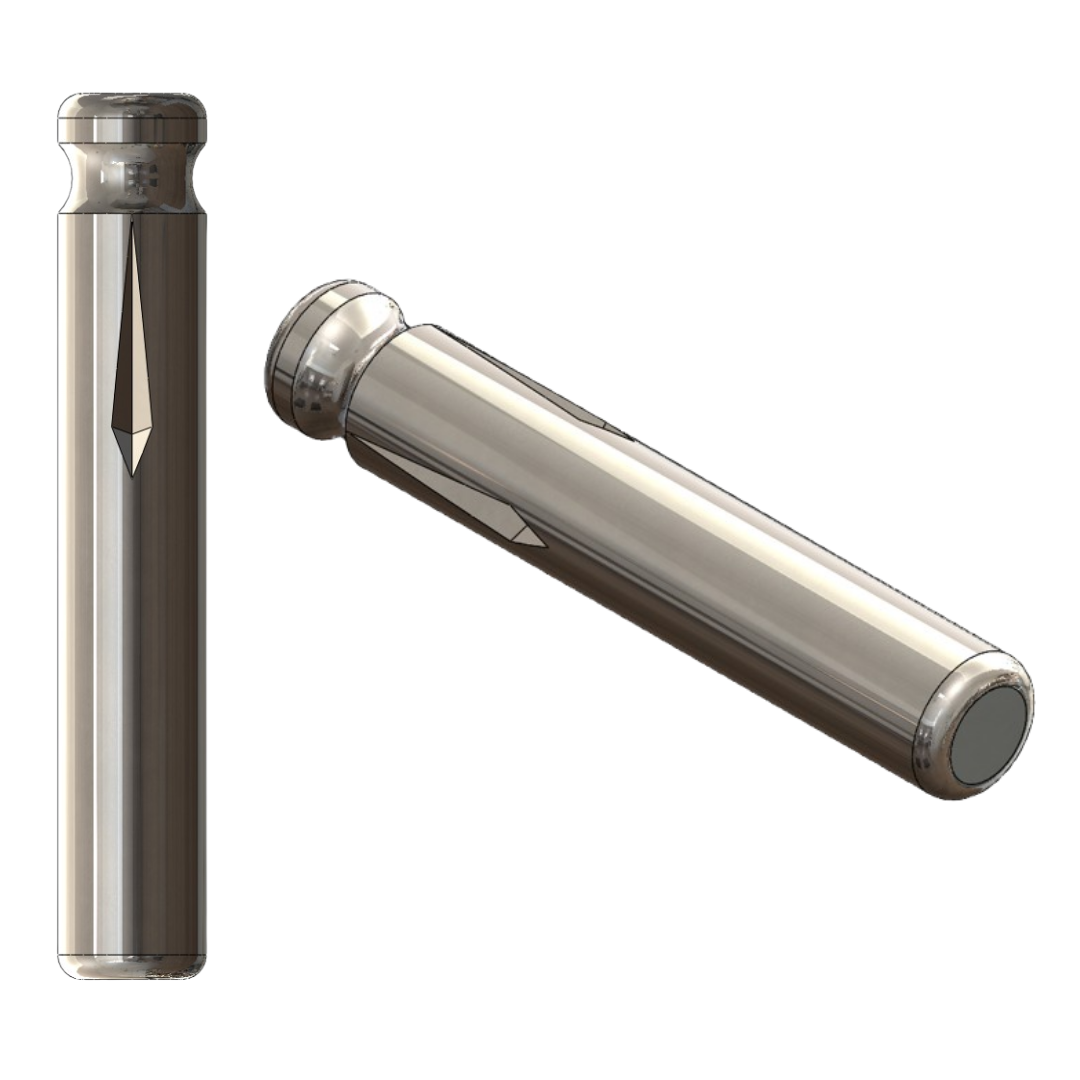
This solution multiplied pull-out resistance by 10 and allowed for the 100N mark to be reached.
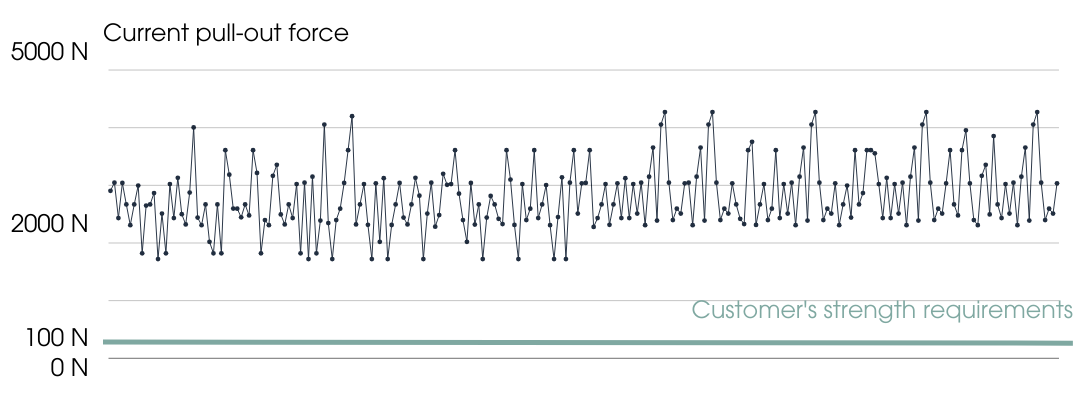
What were the quantifiable benefits for our client?
Thanks to our grooved pin with custom indentation, the customer was able to drastically reduce scrap rates.
Before talking to us, our client had had up to 20% scrap on a batch of 260,000 actuators - this amounts to a loss of nearly €300,000.
Our solution eliminated this problem, ensuring 100% quality and reliability for this system.