Optimising peristaltic pumps
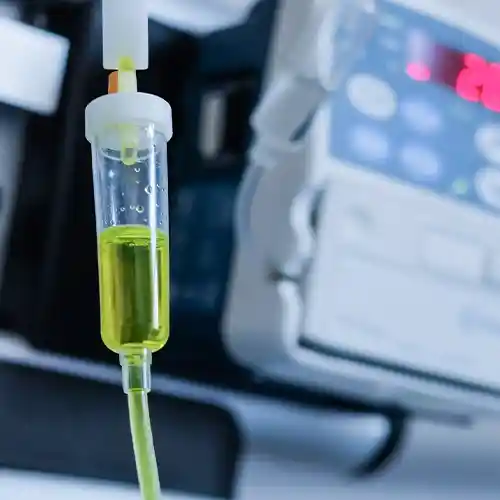
What was the context and the client's desired application?
Peristaltic pumps are used in medical devices, such as infusion and dialysis pumps. The idea is simple: a flexible hose carries the fluid, while dowel pin or rollers put pressure on the rotating pipe to move the fluid. However, this mechanism generates significant friction between the pipe and the sockets, which can lead to rapid pipe degradation and inefficiencies in pumping.
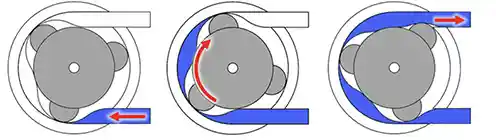
What fasteners was the client using before contacting us?
Before getting in touch with us, our client was using standard stainless steel dowel pins. Despite appearances, these dowels had quite a rough surface (Ra>0.6 µm), which amplified friction with the pipe.
Consequences:
- Pipe wear, requiring them to be changed frequently.
- Reduced engine lifespan, as excessive friction puts more strain on the engine.
- Increased local temperature, which may affect the stability of heat-sensitive fluids.
What studies did we conduct?
We carried out a series of tests in our laboratory to quantify the effects of friction and find an optimal solution:
- Friction tests: Comparing standard and polished sockets.
- Extended cycle simulations: : Tests on 100 million cycles.
- Thermal analyses: Study of temperature increases on pipes subjected to continuous pressure, containing heat-sensitive health products.
What was our advice to the client?
Upon analysis, we recommended that our client look at high-precision dowel pins, polishing their surface roughness to Ra = 0.5 µm. This modification made it possible to reduce friction while increasing the durability of the components.
Advantages of this solution:
- Reduced friction: Less heat generated and less wear on the pipes.
- Increased accuracy: The pumps maintain stable performance even after long periods of use.
- Ease of production: This solution is compatible with existing industrial processes.
- Critical industrial processes: The system guarantees the quality of the fluid circulating in the pump thanks to temperature control.
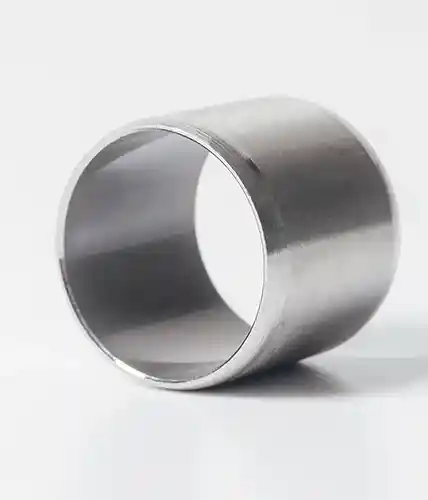
What were the quantifiable benefits for our client?
- Reduced friction: The coefficient of friction changed from 0.45 (standard dowels) to 0.3 (polished dowels), a decrease of 33%.
- Prolonged lifespan: The systems studied saw their durability increase by 60%, reaching a minimum lifespan of 50 million cycles, i.e. 5 years of normal use.
- Controlled heat stability:
- In standard dowel pins, the temperature measured over time were often near the upper limit (7.8 °C) after 1 million cycles, which can alter certain sensitive fluids.
- In polished dowel pins, the temperature became stable around 5.5 °C, remaining well within the safety range (between +2 and +8°C), and thus ensuring the integrity of heat-sensitive health products.
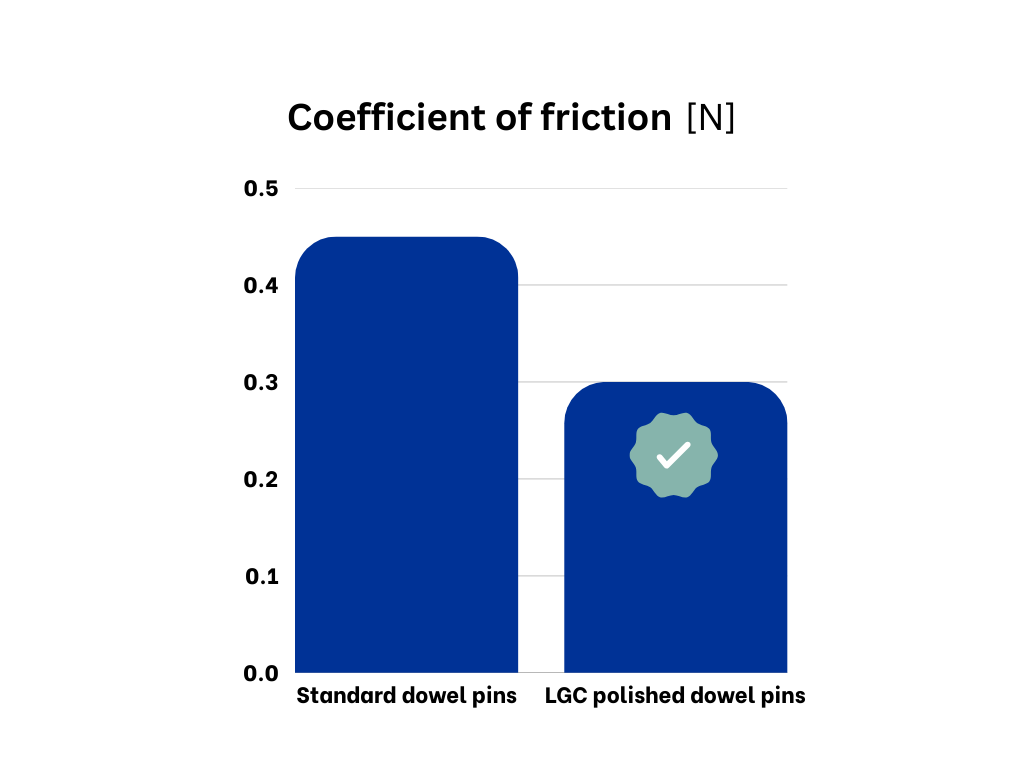
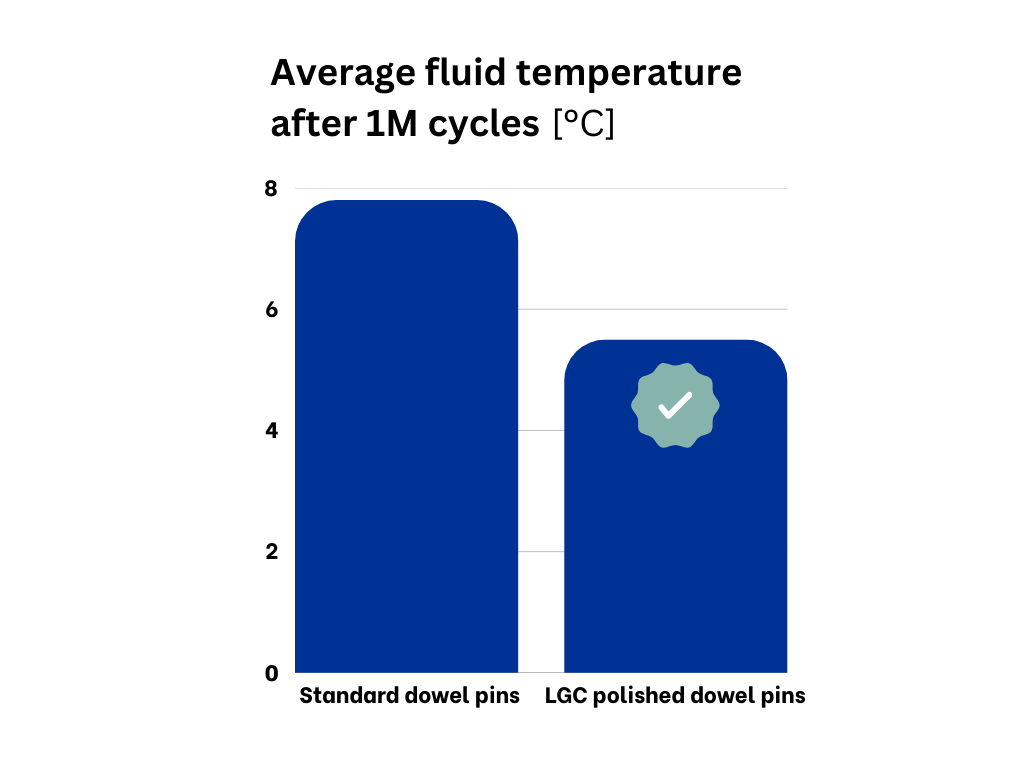
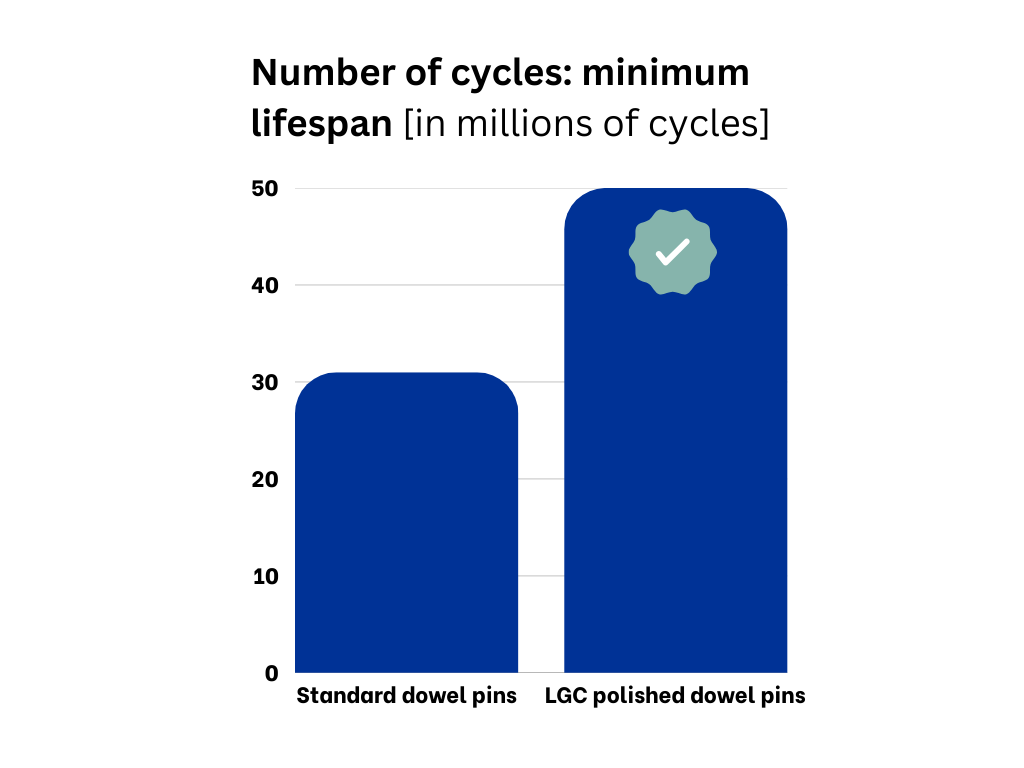